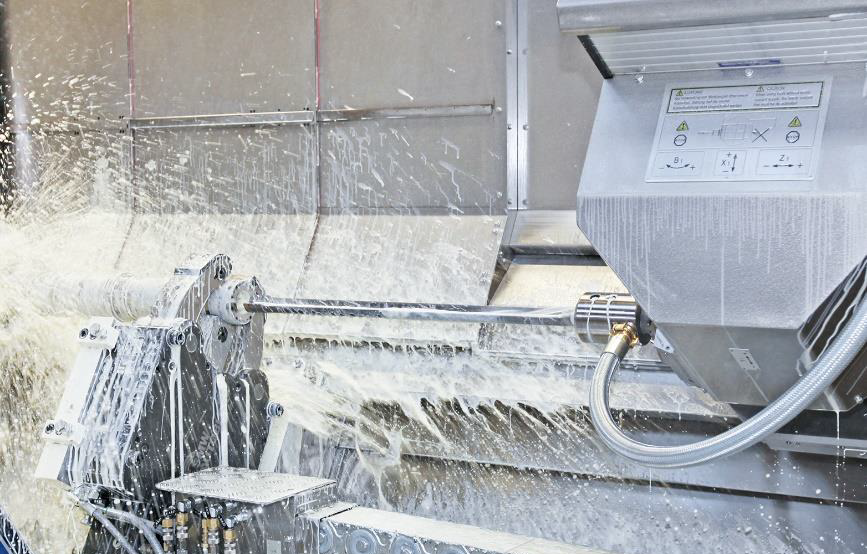
Deep-hole drilling counts among the special disciplines within the field of machining, particularly as these kinds of machining steps usually require special equipment in terms of both tools and machines.
As a machine manufacturer, WFL equips the machine in such a way that it has several decisive advantages over a classic deep-hole drilling machine.
Deep hole drilling
Almost all industries that utilize complete machining have workpieces that require deep-hole drilling. Ultimately, it is the tasks performed in the respective industry that give rise to differences in the process. In the aerospace industry, it is necessary to machine materials such as titanium, Inconel, and other heat-resistant alloys.
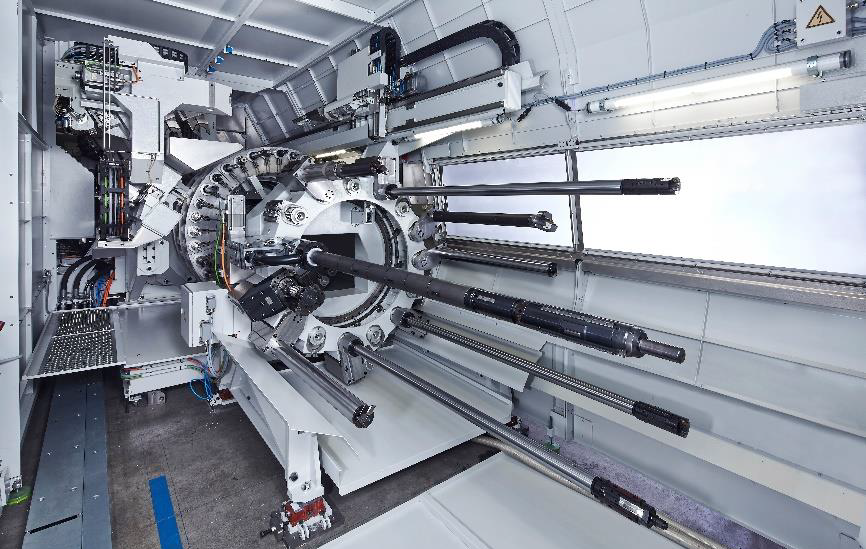
Deep hole drilling is particularly difficult with these materials because the tools are subject to heavy wear and controlled chip breakage requires special measures. As a machine manufacturer, WFL Millturn Technologies Inc. requires comprehensive expertise when it comes to using the right tools and selecting the optimum cooling lubricant.
Deep holes in the plastics industry must exhibit extremely high cylindrical dimensional accuracy. Some of these workpieces are subsequently honed to ensure the required quality can be achieved. When performing deep hole drilling in the crankshaft industry, on the other hand, accessibility is vitally important because the oil holes are manufactured in a wide variety of angular positions.
The decisive factor here is a flexible machine concept, which facilitates reaching a wide range of angles without setup work for drilling the corresponding holes. Perfect accessibility is possible here thanks to the swiveling B-axis of the Millturn machines.
First-class results
WFL develops special tool accommodations - partly to ensure stable tool clamping, but above all to deliver the correct coolant pressure and volume directly to the cutting edge of the tool. In a fully automatic sequence, it is also possible to change long deep-hole drilling tools. With WFL, an automatic tool change can be performed using a pick-up magazine and prismatic tool changer.
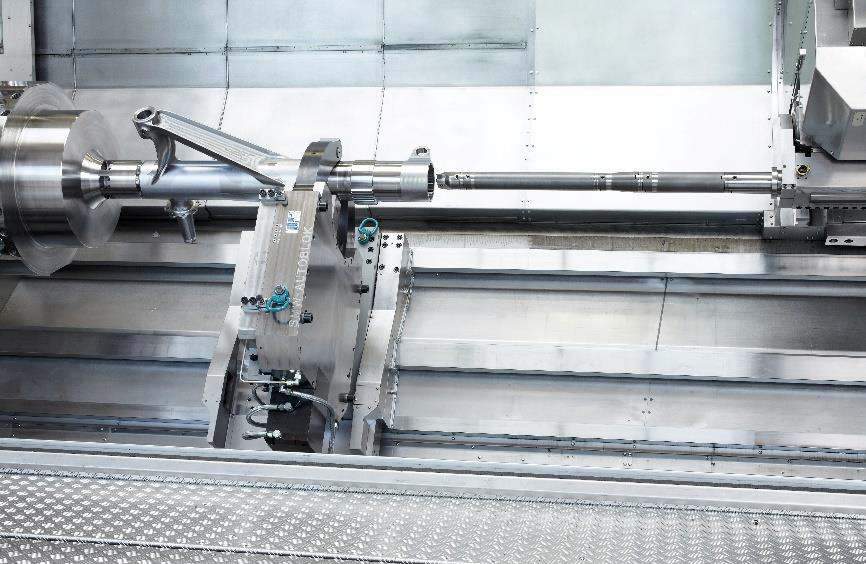
A precise pilot hole forms the basis for good results in deep hole drilling, whereby WFL forms a pilot hole directly in the workpiece to guide the long, unstable drill. These pilot holes are produced with an oversize of < 20μm to a depth of 1.5x the hole diameter. The utmost precision is guaranteed, thanks to workpiece measurement and WFL measuring cycles.
When producing centric holes, the workpiece and tool can be rotated in opposite directions to further improve the quality in terms of hole center deviation.
Coolant pressure versus coolant volume
Millturn machines offer different options when it comes to the coolant supply. For small hole diameters, for example, the cooling lubricant is fed directly through the milling spindle at a coolant pressure of up to 200 bar, while the coolant volume is conversely decisive for larger hole diameters. It is fed automatically to the tool accommodation via a bypass line. The enclosed working area of the WFL machines is essential with such high coolant pressures and volumes.
Automatic workpiece measurement
Due to the long tool exposure, deep drilled holes are subject to hole center deviation that increases with the hole depth. These machining errors cannot be fully eliminated, even when machining on Millturn machines. A particularly interesting machining method is therefore employed here.
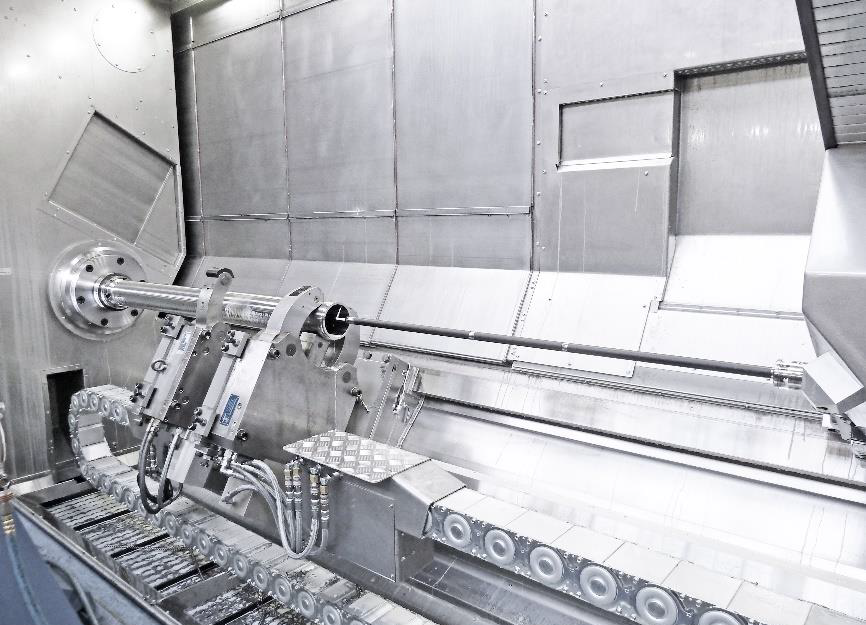
Hole center deviations are measured by intelligent in-process measuring following the completion of deep hole drilling. This is performed either with an extended measuring probe or using ultrasonic wall thickness measurement. This involves measuring the thickness of the wall at various circumferential positions and calculating the middle of the center hole. New clamping points are then produced on the workpiece concentrically to the defective deep drilled hole using turn-milling. This allows the completion of all subsequent machining processes with close form and position tolerance to the deep drilled hole.
The specially developed process monitoring system WFL iControl is used to detect tool breakages or tool wear at an early stage. Such monitoring systems are important in internal machining because the operator has no view of the machining point. The system, therefore, prevents tool breakages - which endanger the tool and the workpiece - or keeps their effects on the workpiece and the machine to a minimum.
The advantages at a glance:
- Complete machining in one machine
- Fully automatic process due to automatic tool change
- Optimum production method for the respective machining situation
- Integrated, automatic measurement
- Finish machining using rolling or honing on the same machine on which drilling was performed
- The cooling lubricant, which is essential for deep hole drilling, can be fed right up to the cutting edge of the tool. This results in a lengthy tool life and reliable discharge of the chips from the hole during the process.
- High feed forces of up to 50kN in the Z-axis ensure the drilling of large hole diameters.
Contact Details
Related Glossary Terms
- alloys
alloys
Substances having metallic properties and being composed of two or more chemical elements of which at least one is a metal.
- coolant
coolant
Fluid that reduces temperature buildup at the tool/workpiece interface during machining. Normally takes the form of a liquid such as soluble or chemical mixtures (semisynthetic, synthetic) but can be pressurized air or other gas. Because of water’s ability to absorb great quantities of heat, it is widely used as a coolant and vehicle for various cutting compounds, with the water-to-compound ratio varying with the machining task. See cutting fluid; semisynthetic cutting fluid; soluble-oil cutting fluid; synthetic cutting fluid.
- drilling machine ( drill press)
drilling machine ( drill press)
Machine designed to rotate end-cutting tools. Can also be used for reaming, tapping, countersinking, counterboring, spotfacing and boring.
- feed
feed
Rate of change of position of the tool as a whole, relative to the workpiece while cutting.
- gang cutting ( milling)
gang cutting ( milling)
Machining with several cutters mounted on a single arbor, generally for simultaneous cutting.
- milling
milling
Machining operation in which metal or other material is removed by applying power to a rotating cutter. In vertical milling, the cutting tool is mounted vertically on the spindle. In horizontal milling, the cutting tool is mounted horizontally, either directly on the spindle or on an arbor. Horizontal milling is further broken down into conventional milling, where the cutter rotates opposite the direction of feed, or “up” into the workpiece; and climb milling, where the cutter rotates in the direction of feed, or “down” into the workpiece. Milling operations include plane or surface milling, endmilling, facemilling, angle milling, form milling and profiling.
- tolerance
tolerance
Minimum and maximum amount a workpiece dimension is allowed to vary from a set standard and still be acceptable.