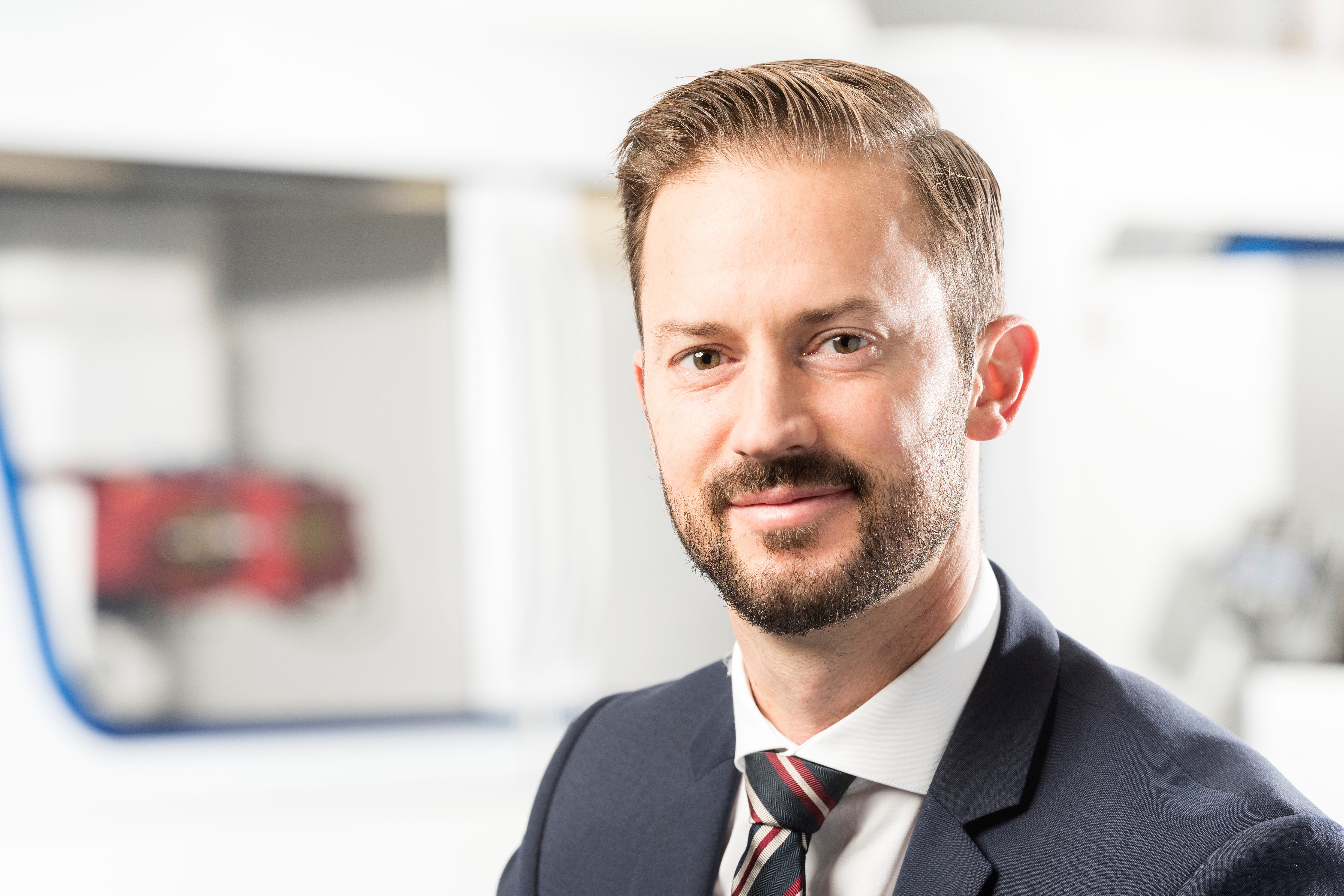
Mobility change will not cause the sharp drop in production initially feared in the machining sector. The specialists at grinding machine manufacturer Studer in Thun are convinced of this. As Sandro Bottazzo, Chief Sales Officer (CSO) at Studer, said, the range of components to be produced will slowly and continuously change over a number of years or even decades. To illustrate this, he cites the expected quantities of passenger cars sold worldwide and the shares of the respective drive technologies. “Based on various analyses, we assume that the combustion engine will continue to play an important part over many years and in numerous regions of the world”, said Bottazzo. “The general demand for individual mobility is continuing to increase worldwide, which offers corresponding opportunities”, said Bottazzo.
Wide variety of drive technology keeps market stable
In the coming decades a wide variety of drive technologies will be available in parallel. In addition to purely battery-powered electric engines, diesel engines with exhaust gas cleaning, hydrogen engines, hybrid engine technology (a combination of combustion and electric engine) and electric drives with power generated by fuel cells will still be used to power cars and trucks. Further drive technologies will even be added where possible. For production companies this means that there is still a great demand for precision components for the drive train. This includes shafts, axles, bushings, gear wheels and compressor wheels, camshafts and crankshafts. In addition, the autonomous vehicles currently under development will soon be produced on a larger scale. For these, the automotive industry additionally requires a wide range of different precision components in large series.
Complex systems increase demand
Efficient drive technologies usually require very complex systems. This applies to hybrid and electric drives, for example, which recover electrical energy during regenerative braking. For machining, this also means the production of an increasing number of usually very complex components. “This opens up additional opportunities. We will continue to monitor the market carefully, so that we can further develop our products accordingly”, said Bottazzo. The already well-known applications for innovative grinding technology include components for CVT transmissions (used primarily in hybrid drives), rotor and gear shafts for electric engines, shafts for turbochargers, compressor shafts for fuel cells, shafts and valves for hydrogen engines, ball screws for electric steering systems as well as various precision tools for cost-effective machining of housings for electric engines. There is likely to be significant growth in the latter.
Productive and cost-effective with sophisticated grinding concepts
As Bottazzo reported, Fritz Studer AG offers safe and reliable grinding technologies for the specified components. On a CVT transmission, for example, the primary and secondary shafts must be ground. This is done in a high-precision process with the shortest machining and processing times on Studer S41 grinding machines, in a single clamping. Even the ball track grooves in the shafts and in the holes of the sheaves can be ground in a single clamping. A vertical spindle, which is mounted on the proven Y-axis, is used on the S41 grinding machine for this purpose. A special unit developed by Studer is used for high-precision grinding of the ball tracks in the sheaves. Grinding in a single clamping, together with fully automated processes, ensures extremely cost-effective production. This applies to the loading, unloading and measurement of workpieces, as well as adaptive control of grinding processes. The latter in particular contributes to the highest precision and reliability. Bottazzo said, “Studer provides manufacturing companies with complete systems of matching components”.
Toothed racks for electric steering systems
Electric steering systems, which are specifically required for autonomously controlled vehicles, operate with precision-ground threaded rods. The steering motion is driven by balls rolling inside. This “ball screw” is advantageously ground from the solid on Studer grinding machines. Compared to other machining technologies a significantly better surface quality is achieved, with comparable machining times. The resulting advantages are reduced steering noise and a considerably longer lifetime of the steering gear. The dressing unit exclusively developed by Studer, WireDress® (wire erosion of the profile), is used for dressing. WireDress® enables completely new possibilities when grinding with metal-bonded CBN and diamond grinding wheels: Not only does this electro-erosive integrated dressing technology save a huge amount of downtime, it also enables sintered metal bonds to be dressed with the highest precision in the grinding machine at full wheel speed.
High-speed compressor wheels for fuel cells
Fuel cells require electrically driven compressors, which operate at very high speeds. The integrated shafts and sheaves must therefore be manufactured with high precision. In addition, they comprise materials that are difficult to machine. Studer has developed its own grinding concept for these requirements. The shafts can be pre-machined at high speeds on an S41cylindrical grinding machine by means of peel grinding. The CBN wheels are dressed with the WireDress® technology exclusively developed by Studer. Thanks to a synchronizable tailstock, the universal cylindrical grinding machines can reliably accept components of different dimensions.
Components for electrically driven turbochargers
Small, powerful and extremely efficient combustion engines can be achieved using turbochargers alone. However, these only work with an adequate exhaust gas flow and pressure, i.e. with sufficiently high speeds of the combustion engine. Only then can the compressors build up the necessary pressure to convey high quantities of combustion air into the cylinders. Insufficient air flow and pressure at low engine speeds is commonly referred to as “turbo lag”. In order to prevent or reduce this, engine manufacturers are increasingly using so-called e-boosters, i.e. electrically driven charge air compressors. The integrated engine shafts can be advantageously ground on universal cylindrical grinding machines, such as a Studer S31, for example. First of all the rotor shaft is ground on the diameter and at the shoulders. This requires a special clamping device to carry the workpiece. After grinding, the magnets are affixed. A titanium alloy sleeve is then pressed on by the magnets. The sleeve must now be externally ground to the precise diameter. This can be advantageously carried out on an S33 universal cylindrical grinding machine.
As Bottazzo added, increasing electromobility means that tools in particular must be ground with high precision, in addition to the actual vehicle components. Studer has developed a suitable concept for this too. In order to achieve the required accuracies, the relevant Studer grinding machine is equipped with the LaserControl in-process measuring system. This is an optical and contact-free system. The “Closed Loop Process” adaptive control controls the grinding process.
Contact Details
Related Glossary Terms
- cubic boron nitride ( CBN)
cubic boron nitride ( CBN)
Crystal manufactured from boron nitride under high pressure and temperature. Used to cut hard-to-machine ferrous and nickel-base materials up to 70 HRC. Second hardest material after diamond. See superabrasive tools.
- cylindrical grinding
cylindrical grinding
Grinding operation in which the workpiece is rotated around a fixed axis while the grinding wheel is fed into the outside surface in controlled relation to the axis of rotation. The workpiece is usually cylindrical, but it may be tapered or curvilinear in profile. See centerless grinding; grinding.
- dressing
dressing
Removal of undesirable materials from “loaded” grinding wheels using a single- or multi-point diamond or other tool. The process also exposes unused, sharp abrasive points. See loading; truing.
- grinding
grinding
Machining operation in which material is removed from the workpiece by a powered abrasive wheel, stone, belt, paste, sheet, compound, slurry, etc. Takes various forms: surface grinding (creates flat and/or squared surfaces); cylindrical grinding (for external cylindrical and tapered shapes, fillets, undercuts, etc.); centerless grinding; chamfering; thread and form grinding; tool and cutter grinding; offhand grinding; lapping and polishing (grinding with extremely fine grits to create ultrasmooth surfaces); honing; and disc grinding.
- grinding machine
grinding machine
Powers a grinding wheel or other abrasive tool for the purpose of removing metal and finishing workpieces to close tolerances. Provides smooth, square, parallel and accurate workpiece surfaces. When ultrasmooth surfaces and finishes on the order of microns are required, lapping and honing machines (precision grinders that run abrasives with extremely fine, uniform grits) are used. In its “finishing” role, the grinder is perhaps the most widely used machine tool. Various styles are available: bench and pedestal grinders for sharpening lathe bits and drills; surface grinders for producing square, parallel, smooth and accurate parts; cylindrical and centerless grinders; center-hole grinders; form grinders; facemill and endmill grinders; gear-cutting grinders; jig grinders; abrasive belt (backstand, swing-frame, belt-roll) grinders; tool and cutter grinders for sharpening and resharpening cutting tools; carbide grinders; hand-held die grinders; and abrasive cutoff saws.
- parallel
parallel
Strip or block of precision-ground stock used to elevate a workpiece, while keeping it parallel to the worktable, to prevent cutter/table contact.