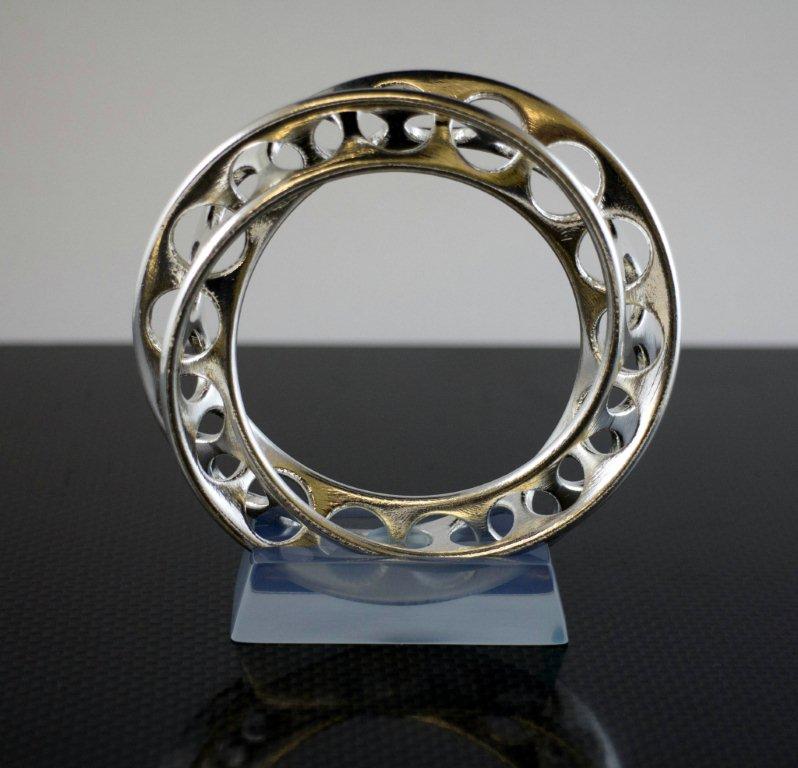
Depending on whom you ask, you’ll receive wildly different unravelings of the acronym DFAM.
To music aficionados, DFAM might mean “drummer from another mother,” clever branding from Moog Music Inc. to describe its newest line of percussion synthesizers. I wish I’d thought of that phrase. DFAM could mean the Darlington Farmers Auction Mart but probably only to those who live near there in England and are interested in buying a cow, goat or sheep. At The Walt Disney Co., DFAM refers to the extended family of employees who share the stress of working at the Magic Kingdom—as in, “I’m going to chill this weekend with my DFAM before the big Labor Day rush.”
Then there’s the DFAM that manufacturers care about—or rather the additive manufacturers. That’s because DFAM is short for “design for additive manufacturing,” an acronym every bit as relevant to machinists as it is to people in 3D printing.
Granted, it’s a bit of a knockoff. Design for manufacturability (DFM), design for assembly (DFA) and design for manufacture and assembly (DFMA) have been around for several decades.
DFMA is a registered trademark of Boothroyd Dewhurst Inc., which developed a suite of software products for making manufactured parts of all kinds easier and more cost-effective to produce.
Ironically, BDI founders Geoffrey Boothroyd and Peter Dewhurst released the first versions of their DFM and DFA software for the Apple II Plus—remember that?—during the 1980s, right around the time that Chuck Hull introduced stereolithography 3D printers.
I’m not sure who invented the term DFAM, but the practice is clearly important for the same reasons that DFMA is important to traditional manufacturing. In some ways, DFAM is even more necessary, as 3D printing requires a fair amount of topology optimization and no small amount of nontraditional thinking if one is to take full advantage of it.
Here’s the problem with all this: Additive and subtractive manufacturing should not be considered separate technologies but different tools in the same toolbox. They have always complemented one another and are doing this more as 3D metal printing’s capabilities evolve.
Just as milling/turning centers and multitasking machine tools—many of which now have additive capabilities—are slowly breaking down the wall between the milling and turning departments, DFAM and DFMA can and must join together at some point.
It’s a problem ripe for the solving. However, until someone takes the “design for” bull by the horns, designers, engineers, machinists and programmers will have to continue doing the best they can with the tools they’re given. Just remember that there’s more than one way to skin the manufacturing cat.
Related Glossary Terms
- centers
centers
Cone-shaped pins that support a workpiece by one or two ends during machining. The centers fit into holes drilled in the workpiece ends. Centers that turn with the workpiece are called “live” centers; those that do not are called “dead” centers.
- chuck
chuck
Workholding device that affixes to a mill, lathe or drill-press spindle. It holds a tool or workpiece by one end, allowing it to be rotated. May also be fitted to the machine table to hold a workpiece. Two or more adjustable jaws actually hold the tool or part. May be actuated manually, pneumatically, hydraulically or electrically. See collet.
- gang cutting ( milling)
gang cutting ( milling)
Machining with several cutters mounted on a single arbor, generally for simultaneous cutting.
- milling
milling
Machining operation in which metal or other material is removed by applying power to a rotating cutter. In vertical milling, the cutting tool is mounted vertically on the spindle. In horizontal milling, the cutting tool is mounted horizontally, either directly on the spindle or on an arbor. Horizontal milling is further broken down into conventional milling, where the cutter rotates opposite the direction of feed, or “up” into the workpiece; and climb milling, where the cutter rotates in the direction of feed, or “down” into the workpiece. Milling operations include plane or surface milling, endmilling, facemilling, angle milling, form milling and profiling.
- turning
turning
Workpiece is held in a chuck, mounted on a face plate or secured between centers and rotated while a cutting tool, normally a single-point tool, is fed into it along its periphery or across its end or face. Takes the form of straight turning (cutting along the periphery of the workpiece); taper turning (creating a taper); step turning (turning different-size diameters on the same work); chamfering (beveling an edge or shoulder); facing (cutting on an end); turning threads (usually external but can be internal); roughing (high-volume metal removal); and finishing (final light cuts). Performed on lathes, turning centers, chucking machines, automatic screw machines and similar machines.