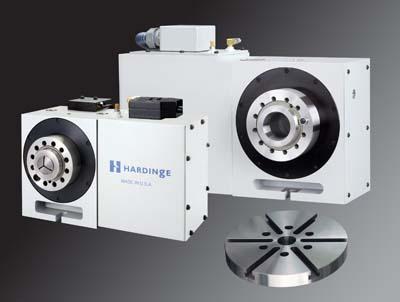
"Back in 2008, Hardinge introduced a low-profile rotary table as a standard, no-frills unit to compete against other 210mm tables on the market," states Al Comstock, Rotary Product Manager at Hardinge Inc. "Now, by customer demand, we've redesigned the model to include the infamous Hardinge collet-ready 16C spindle that provides the high-precision gripping options for which Hardinge is known. We've also extended the spindle nose for additional tooling clearance."
Part quality begins at the spindle. Minimal overhang from the spindle bearings assure that spindle accuracy is transferred directly to the part being machined. Most brands of rotary tables use a collet adaptation chuck, moving the cutting several inches away from the spindle bearings. Hardinge rotary spindles are collet-ready for gripping parts of all shapes, sizes and materials. High-precision gripping options for the GD210LP include standard 16C collets, step chucks for larger diameters, Sure-Grip expanding collets and custom collets with the use of an optional collet closer. Special accuracy FlexC collet systems, chucks and the precision-ground faceplate (included) will mount on the A2-5 spindle.
What does this mean to the programmer and machine operator? Higher accuracy jobs can be run, less tooling interference, length control options, internal gripping capability, no time-consuming fixtures, and lightweight alternatives for a heavy chuck. The added versatility and the ability to share tooling with other machines in the shop is highly advantageous.
The Hardinge enhanced GD210LP rotary table indexer provides rigidity, speed, accuracy, repeatability and flexibility in an affordable package. High stiffness and super rigidity are accomplished with large diameter bearings and a fail-safe clamp system allowing part weight of up to 220 pounds. Radial load testing indicated a stiffness of 4x greater than a competitive model. The GD210LP uses up to 233ft-lb/315Nm of clamping torque to handle off-center drilling, cross-axis milling and other high-force cutting applications. A fast clamp and release in milliseconds reduces cycle time. Hardinge's hardened and ground steel cross-axis helical gear provides a longer life and continued accuracy when compared to softer gears and worm gears found in other brands. Based on true bidirectional testing, Hardinge guarantees +/-15 arc-second accuracy and 10 arc-second repeatability.
"With this redesign, all of our rotary products incorporate the collet-ready spindle," states Al Comstock.
The GD210LP operates with a Hardinge servo control or it can be integrated to the machine via 4th axis. Options include a left- or right-hand motor mount, pneumatic collet closer, tailstock and a plate or cube trunnion for machining multiple parts. For smaller part production, look at the 160mm rotary table indexer with the Hardinge collet-ready 5C spindle.
Contact Details
Related Glossary Terms
- chuck
chuck
Workholding device that affixes to a mill, lathe or drill-press spindle. It holds a tool or workpiece by one end, allowing it to be rotated. May also be fitted to the machine table to hold a workpiece. Two or more adjustable jaws actually hold the tool or part. May be actuated manually, pneumatically, hydraulically or electrically. See collet.
- clearance
clearance
Space provided behind a tool’s land or relief to prevent rubbing and subsequent premature deterioration of the tool. See land; relief.
- collet
collet
Flexible-sided device that secures a tool or workpiece. Similar in function to a chuck, but can accommodate only a narrow size range. Typically provides greater gripping force and precision than a chuck. See chuck.
- gang cutting ( milling)
gang cutting ( milling)
Machining with several cutters mounted on a single arbor, generally for simultaneous cutting.
- milling
milling
Machining operation in which metal or other material is removed by applying power to a rotating cutter. In vertical milling, the cutting tool is mounted vertically on the spindle. In horizontal milling, the cutting tool is mounted horizontally, either directly on the spindle or on an arbor. Horizontal milling is further broken down into conventional milling, where the cutter rotates opposite the direction of feed, or “up” into the workpiece; and climb milling, where the cutter rotates in the direction of feed, or “down” into the workpiece. Milling operations include plane or surface milling, endmilling, facemilling, angle milling, form milling and profiling.
- stiffness
stiffness
1. Ability of a material or part to resist elastic deflection. 2. The rate of stress with respect to strain; the greater the stress required to produce a given strain, the stiffer the material is said to be. See dynamic stiffness; static stiffness.