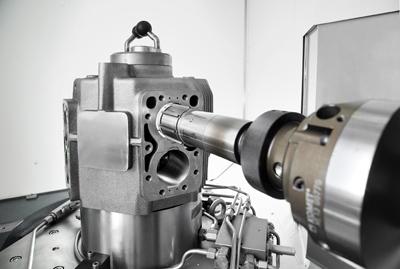
The complete machining of cylindrical bores from raw part to precise, controllable tolerances in just one setup on its H Series machining center dramatically reduces tooling and machine cost as well as machining times, according to Heller.
Deployed on a 4-axis machining center, Heller's NCU out-facing head prepared for honing can adjust the size, taper, surface and tolerance of a bore as it changes the size of the tool during the honing process. A Marposs in-process gage is incorporated into the head.
Heller collaborated with DIAHON to program honing cycles that permit helical slide honing. The H series are able to create a continuous cross-grind that can otherwise be produced only on advanced, expensive honing machines.
Unlike on honing machines, however, bores with a cylinder form tolerance of just 1 µm can be produced in one setup over a length of 300mm, for example, eliminating the typical 3-pass honing process and minimizing honing cycle time.
According to Bernd Sihling, Deputy CEO of DIAHON, "Combined with a machining center as a standard machine, honing is efficient and cost-effective up to a certain batch size. This is how, in one specific case, we were able to reduce the machine running times from 15 minutes for internal cylindrical grinding to 12 seconds by means of honing."
Productivity increases in this range can benefit manufacturers of pump housings, con-rods, cylinder blocks or hydraulic control housings. Cost savings result from the short machining times and the elimination of a special machine for honing. With honing on a machining center, the in-feed motion and the speed of the tool can be adjusted while machining occurs. A high degree of automation is possible, and production capacity can easily be adjusted as needed.
"Automotive Tier One manufacturers," observes Vince Trampus, Heller US Vice President – Sales, "can now avoid investing in dedicated honing systems for engine cylinder bores up to a certain volume production. Machining centers offer the total processing flexibility the industry is asking for, and adding the honing process to machining center capability makes the case even stronger."
Until now, ‘multitasking' has not included honing as a process. Once considered a costly, complex process, honing provided little reason to be included in a total part process, and it required expensive machines and tools. The precise machining of cylindrical bores with tight tolerances and complex geometric and topological features tended to be achieved by other processes, such as internal cylindrical grinding.
But according to Bernd Sihling, honing can be extremely process-capable and controllable: "Honing isn't such a complex process. There are three distinctly different types: honing by means of a permanently set tool with a defined diameter, honing by means of a tool with a flexible diameter, the hone of which can be expanded by coolant pressure, and path-controlled honing on machining centers, as accomplished by Heller with its controllable out-facing head."
Heller has added honing to the smart technology mix on the H series machining centers. The advantage is that this 4-axis machining center is highly dynamic and has a U-axis (out-facing head).
While economical, honing on a machining center must also satisfy technical requirements, including the highly precise replication of macroforms (cylinders). Series con-rod machining using coolant- expanded honing technology has also been performed on machining centers for some years now, but not at production volumes.
Honing of coated cylinder crankcases by means of out-facing heads combined with a non-wearing air measuring between nozzles and bore during honing is expected to become a preferred solution in engine construction for the future. High productivity is complemented by high precision (tolerance less than 6 µm) with specified surface finish, roughness, plateau structures, and cross-grind.
Contact Details
Related Glossary Terms
- centers
centers
Cone-shaped pins that support a workpiece by one or two ends during machining. The centers fit into holes drilled in the workpiece ends. Centers that turn with the workpiece are called “live” centers; those that do not are called “dead” centers.
- coolant
coolant
Fluid that reduces temperature buildup at the tool/workpiece interface during machining. Normally takes the form of a liquid such as soluble or chemical mixtures (semisynthetic, synthetic) but can be pressurized air or other gas. Because of water’s ability to absorb great quantities of heat, it is widely used as a coolant and vehicle for various cutting compounds, with the water-to-compound ratio varying with the machining task. See cutting fluid; semisynthetic cutting fluid; soluble-oil cutting fluid; synthetic cutting fluid.
- cylindrical grinding
cylindrical grinding
Grinding operation in which the workpiece is rotated around a fixed axis while the grinding wheel is fed into the outside surface in controlled relation to the axis of rotation. The workpiece is usually cylindrical, but it may be tapered or curvilinear in profile. See centerless grinding; grinding.
- grinding
grinding
Machining operation in which material is removed from the workpiece by a powered abrasive wheel, stone, belt, paste, sheet, compound, slurry, etc. Takes various forms: surface grinding (creates flat and/or squared surfaces); cylindrical grinding (for external cylindrical and tapered shapes, fillets, undercuts, etc.); centerless grinding; chamfering; thread and form grinding; tool and cutter grinding; offhand grinding; lapping and polishing (grinding with extremely fine grits to create ultrasmooth surfaces); honing; and disc grinding.
- machining center
machining center
CNC machine tool capable of drilling, reaming, tapping, milling and boring. Normally comes with an automatic toolchanger. See automatic toolchanger.
- tolerance
tolerance
Minimum and maximum amount a workpiece dimension is allowed to vary from a set standard and still be acceptable.