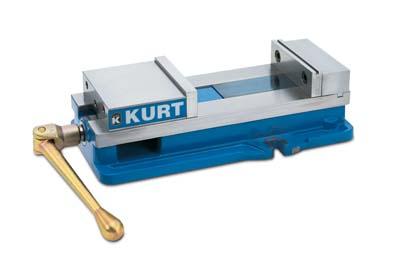
Kurt Manufacturing Co. announces re-introduction of its flagship D688 vise model with more features. Having proven itself in the marketplace as the new machining vise standard, the D688 replaces the D675 model.
"The D688 with many upgraded features replaces the D675 model, which has served machinists well during its era," reports Steve Kane, global sales and marketing manager for Kurt Industrial Products. "The D688 is designed for the high performance requirements of the latest machining centers. It meets the needs of today's highly skilled and demanding machinists. It does this by providing more clamping force, and larger part holding capacity with many other upgraded features. The D688 is also being offered at an 8 percent price reduction."
The D688 has the same footprint as the D675 (distance of keyway to stationary jaw is identical) so the two vises can be aligned on a vise table without problems. This allows machinists to phase in the new vise technology without making their existing vises obsolete.
The D688 features an 8.8 inch jaw opening and repeatability to within 0.001 inch. It produces up to 7,968 lbs. clamping force with just 80 ft. lbs. input torque. This is a 25 percent increase in jaw capacity and a 36 percent greater clamping torque than the D675 and similar competitor vises.
Designed with high precision roller bearings and alloy steel screw mechanism (competitor models use less efficient ball bearings), D688 vises distribute clamping force evenly and precisely across the full jaw surface. The Anglock design in the moveable jaw (patented by Kurt) further reduces jaw lift. Providing overall vise rigidity while absorbing machining vibration, Kurt D688 vises have porosity-free, 80,000-PSI ductile iron bodies. Additional features include removable, hardened jaw plates, ergonomically designed vise handle, and GrooveLock workstops that store easily in the vise body.
The D688 vise is designed for use on the latest machine tools including machining centers and knee-type mills. The D688 is ideal for all types of machining operations including precision boring, tapping, drilling and finishing with high accuracy on most part configurations.
Contact Details
Related Glossary Terms
- boring
boring
Enlarging a hole that already has been drilled or cored. Generally, it is an operation of truing the previously drilled hole with a single-point, lathe-type tool. Boring is essentially internal turning, in that usually a single-point cutting tool forms the internal shape. Some tools are available with two cutting edges to balance cutting forces.
- centers
centers
Cone-shaped pins that support a workpiece by one or two ends during machining. The centers fit into holes drilled in the workpiece ends. Centers that turn with the workpiece are called “live” centers; those that do not are called “dead” centers.
- tapping
tapping
Machining operation in which a tap, with teeth on its periphery, cuts internal threads in a predrilled hole having a smaller diameter than the tap diameter. Threads are formed by a combined rotary and axial-relative motion between tap and workpiece. See tap.