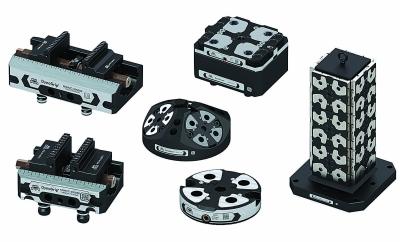
Mate Precision Technologies, a leading provider of innovative workholding solutions, has introduced a series of new enhancements for its 52/96 zero point workholding system. Featured at Mate's booth during IMTS 2024, the enhancements are said to help customers solve a wide range of metalworking challenges quickly and efficiently.
Among the innovations on display during IMTS 2024 were:
- Machinable Hard Jaws — Mate’s new machinable hard jaws allow users to create custom profiles from blank jaws. Customers can request Mate to customize the hard jaws with delivery usually in 10 days or less; or they can order blank profiles to customize in-house.
- DynoGrip ER Collet Chucks — These collet chucks provide an easy and reliable solution for holding round parts during milling operations. The industry-standard ER32 and ER40 collets accommodate diameters from 2 mm (0.08") to 32 mm (1.26").
- DynoGrip Direct Mount Vise — A wider body provides additional flexibility and allows for direct bolting to a machine bed, pallet or other fixture. It includes two 10 mm counterbores on center, 100 mm apart for direct mounting.
- DynoMount Lower Profile Pyramid — This three-sided pyramid is designed for more compact machining spaces.
The 52/96 zero-point workholding system includes vises, bases, and mounting systems that are manufactured in Minnesota. Engineered to maximize holding power for 3-, 4- and 5-axis machining centers, Mate workholding not only reduces setup times and process variability, it offers best-in-class accuracy and repeatability in a compact, quick change, modular design.
Mate’s workholding system includes:
- Mate DynoGrip self-centering vises feature maximum holding power in a compact system with minimal part movement and zero-point quality engagement with a rigid four-post pull stud pattern. The vises come in 13 sizes and 3 widths.
- Mate DynoLock quick change bases provide zero-point quality engagement with the same four-post stud pattern and best-in-class holding power, center accuracy and repeatability and is available in 11 size variations.
- Mate DynoMount system expands machine capacity and flexibility with tombstones, pyramids, risers, and dual right-angle mounts that feature the same zero-point quality engagement for four-point stud patterns.
The Mate 52/96 workholding system also includes QuickSpecs, Mate’s unique product identification system, allowing real-time access to critical user data, CAD models, and potential integration into business systems. Additionally, the product supports common robotic interfaces and palletizing systems to support factory automation. The Mate workholding system is backed by sophisticated technical support, unsurpassed product quality, responsive customer service, and Mate’s industry-leading 100-percent satisfaction guarantee.
Contact Details
Related Glossary Terms
- centers
centers
Cone-shaped pins that support a workpiece by one or two ends during machining. The centers fit into holes drilled in the workpiece ends. Centers that turn with the workpiece are called “live” centers; those that do not are called “dead” centers.
- collet
collet
Flexible-sided device that secures a tool or workpiece. Similar in function to a chuck, but can accommodate only a narrow size range. Typically provides greater gripping force and precision than a chuck. See chuck.
- computer-aided design ( CAD)
computer-aided design ( CAD)
Product-design functions performed with the help of computers and special software.
- fixture
fixture
Device, often made in-house, that holds a specific workpiece. See jig; modular fixturing.
- gang cutting ( milling)
gang cutting ( milling)
Machining with several cutters mounted on a single arbor, generally for simultaneous cutting.
- metalworking
metalworking
Any manufacturing process in which metal is processed or machined such that the workpiece is given a new shape. Broadly defined, the term includes processes such as design and layout, heat-treating, material handling and inspection.
- milling
milling
Machining operation in which metal or other material is removed by applying power to a rotating cutter. In vertical milling, the cutting tool is mounted vertically on the spindle. In horizontal milling, the cutting tool is mounted horizontally, either directly on the spindle or on an arbor. Horizontal milling is further broken down into conventional milling, where the cutter rotates opposite the direction of feed, or “up” into the workpiece; and climb milling, where the cutter rotates in the direction of feed, or “down” into the workpiece. Milling operations include plane or surface milling, endmilling, facemilling, angle milling, form milling and profiling.
- modular design ( modular construction)
modular design ( modular construction)
Manufacturing of a product in subassemblies that permits fast and simple replacement of defective assemblies and tailoring of the product for different purposes. See interchangeable parts.