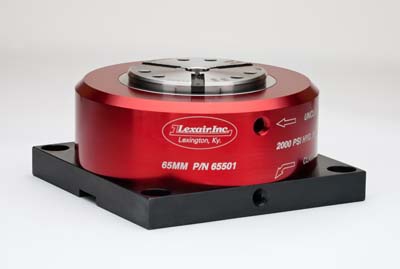
Lexair Inc. introduces a new low-profile stationary collet closer that uses quick-change vulcanized collet heads. These collet closers were designed around the Hardinge Flex-C collet heads, and will also accept other brands of vulcanized collets on the market currently being used in lathe applications. Lexair Flex-Grip Collet Closers can be used horizontally or vertically on mill tables, tombstones or rotary trunnions. Lexair Flex-Grip Collet Closers have a through-hole, double-action, fixed-length design allowing long parts to be accommodated through the body. They are hydraulically actuated with pressure-to-open, pressure-to-close (no springs) while holding the collet and part in a fixed position. Maximum input pressure is 2,000 psi.
The collet closers are available in 42 and 65mm sizes and have a low profile of 2.75" and 3.17" respectively. The short height permits more Z-axis clearance to accommodate a wider range of part sizes. Lexair Flex-Grip collet closers can be used individually or ganged together on a fixture plate for multiple part machining. 4th-axis machining can be achieved when installed on a rotary plate trunnion. Vulcanized collet heads have a much wider compression range than conventional spring collets allowing for variation in stock.
A total of +/- .020" diameter range is possible while still maintaining parallel grip on the part. Parallel grip helps to minimize stock push back, at the same time requiring less draw bar force to equal the same clamping force of conventional spring collets. Collet changeover is a matter of seconds using the collet compression tool. Additional benefits include automatic centering of the part and quick set up.
Lexair is an authorized distributor for Hardinge FlexC vulcanized collets heads for use in these collet closers. Collet heads are available in 42mm and 65mm sizes in round smooth, round serrated, hex serrated, square smooth and emergency styles. The collet heads are sealed to minimize chips and sludge from entering the spindle. Collets are available in inch capacities from ¼" up to 2-9/16" and metric capacities from 6mm up to 65mm.
Contact Details
Related Glossary Terms
- centering
centering
1. Process of locating the center of a workpiece to be mounted on centers. 2. Process of mounting the workpiece concentric to the machine spindle. See centers.
- clearance
clearance
Space provided behind a tool’s land or relief to prevent rubbing and subsequent premature deterioration of the tool. See land; relief.
- collet
collet
Flexible-sided device that secures a tool or workpiece. Similar in function to a chuck, but can accommodate only a narrow size range. Typically provides greater gripping force and precision than a chuck. See chuck.
- fixture
fixture
Device, often made in-house, that holds a specific workpiece. See jig; modular fixturing.
- lathe
lathe
Turning machine capable of sawing, milling, grinding, gear-cutting, drilling, reaming, boring, threading, facing, chamfering, grooving, knurling, spinning, parting, necking, taper-cutting, and cam- and eccentric-cutting, as well as step- and straight-turning. Comes in a variety of forms, ranging from manual to semiautomatic to fully automatic, with major types being engine lathes, turning and contouring lathes, turret lathes and numerical-control lathes. The engine lathe consists of a headstock and spindle, tailstock, bed, carriage (complete with apron) and cross slides. Features include gear- (speed) and feed-selector levers, toolpost, compound rest, lead screw and reversing lead screw, threading dial and rapid-traverse lever. Special lathe types include through-the-spindle, camshaft and crankshaft, brake drum and rotor, spinning and gun-barrel machines. Toolroom and bench lathes are used for precision work; the former for tool-and-die work and similar tasks, the latter for small workpieces (instruments, watches), normally without a power feed. Models are typically designated according to their “swing,” or the largest-diameter workpiece that can be rotated; bed length, or the distance between centers; and horsepower generated. See turning machine.
- milling machine ( mill)
milling machine ( mill)
Runs endmills and arbor-mounted milling cutters. Features include a head with a spindle that drives the cutters; a column, knee and table that provide motion in the three Cartesian axes; and a base that supports the components and houses the cutting-fluid pump and reservoir. The work is mounted on the table and fed into the rotating cutter or endmill to accomplish the milling steps; vertical milling machines also feed endmills into the work by means of a spindle-mounted quill. Models range from small manual machines to big bed-type and duplex mills. All take one of three basic forms: vertical, horizontal or convertible horizontal/vertical. Vertical machines may be knee-type (the table is mounted on a knee that can be elevated) or bed-type (the table is securely supported and only moves horizontally). In general, horizontal machines are bigger and more powerful, while vertical machines are lighter but more versatile and easier to set up and operate.
- parallel
parallel
Strip or block of precision-ground stock used to elevate a workpiece, while keeping it parallel to the worktable, to prevent cutter/table contact.
- through-hole
through-hole
Hole or cavity cut in a solid shape that connects with other holes or extends all the way through the workpiece.