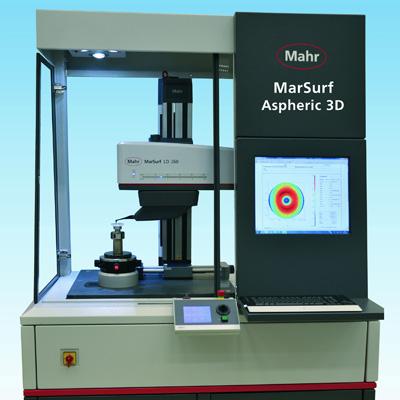
Mahr Federal Inc. has introduced a new high-precision 2D/3D measuring station for checking contour and surface topography of aspheric optical lenses and other components during multi-stage grinding and polishing operations. The MarSurf LD 130 and 260 Aspheric units feature high measuring speed, measuring range of up to 260mm, vertical resolution of 0.8 nm, and form deviations of less than 100 nm. As with all Mahr metrology systems, the MarSurf LD 130 and 260 Aspheric are backed by Mahr's extensive worldwide service and application support network.
"The market for high precision optics is growing very rapidly," said Pat Nugent, Vice President for Metrology Systems at Mahr Federal, headquarters of the Mahr group's US operations. "We see tremendous opportunities both to support existing applications and to apply Mahr's extensive metrology expertise in developing new systems to meet future needs. To this end, Mahr has dedicated an entire division to R&D, custom programming, and support at its manufacturing facility in Jena, Germany, a world renowned center for optics and the home of optics pioneers like Ernst Abbe."
The MarSurf LD 130 and 260 Aspheric facilitate the multiset grinding and polishing manufacturing process for high precision optics by providing fast accurate 2D and 3D measurements for the evaluation of contour and surface topography. The system can be used for spherical and aspherical lenses, as well as many types of cylinder lenses, lens mounts, housings, and other mechanical components. Measuring speed is up to 10mm/s for large lenses, and down to 0.02mm/s for micro lenses.
For 2D measurement the system generates a linear scan over the zenith of the lens. Collected data is compared to the nominal aspheric lens contour and presents results as PV or RMS values and slope error. For 3D measurements, the system generates several linear profiles across the center of the lens. The lens is then rotated and several circular profiles gathered. Combined, these measuring points create the surface profile, which can be compared to the nominal shape via a sagitta table or 3D-point cloud. The differential profile can be output as a color-coded height picture, and both 2D scans and 3D topography can be exported in machine-readable format for closed loop process control.
The MarSurf LD 130/260 Aspheric includes a new probe system with a biomimetic probe arm design that provides increased stiffness, damping, and lower moment of inertia. A chip integrated in the probe arm provides probe identification and parameters, and verification of correct mounting position, allowing probe arms to be changed without recalibration. Automatic probe positioning allows even discontinuous surfaces to be measured.
Contact Details
Related Glossary Terms
- grinding
grinding
Machining operation in which material is removed from the workpiece by a powered abrasive wheel, stone, belt, paste, sheet, compound, slurry, etc. Takes various forms: surface grinding (creates flat and/or squared surfaces); cylindrical grinding (for external cylindrical and tapered shapes, fillets, undercuts, etc.); centerless grinding; chamfering; thread and form grinding; tool and cutter grinding; offhand grinding; lapping and polishing (grinding with extremely fine grits to create ultrasmooth surfaces); honing; and disc grinding.
- metrology
metrology
Science of measurement; the principles on which precision machining, quality control and inspection are based. See precision machining, measurement.
- polishing
polishing
Abrasive process that improves surface finish and blends contours. Abrasive particles attached to a flexible backing abrade the workpiece.
- process control
process control
Method of monitoring a process. Relates to electronic hardware and instrumentation used in automated process control. See in-process gaging, inspection; SPC, statistical process control.
- stiffness
stiffness
1. Ability of a material or part to resist elastic deflection. 2. The rate of stress with respect to strain; the greater the stress required to produce a given strain, the stiffer the material is said to be. See dynamic stiffness; static stiffness.