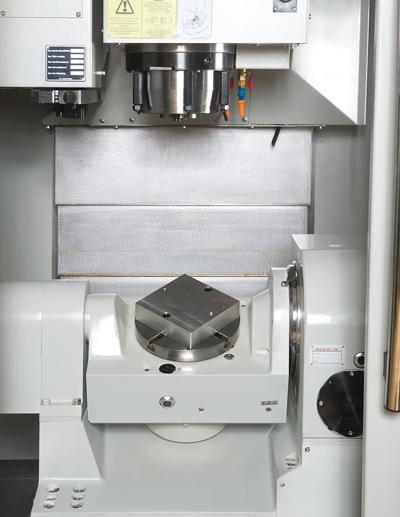
Hardinge Inc. announces the release of two Bridgeport 5-Face (4+1) Vertical Machining Centers: the GX 250 5F and GXR 320 5F. These 4+1 axis vertical machining centers are high quality machine tools designed to achieve maximum capacity and performance in the job shop, OEM, aerospace, medical, electronic, defense, automotive and power generation industries, as well as many other manufacturing sectors.
Two machine sizes are available and come standard with a sophisticated, yet user-friendly, FANUC 0i-D control for 4+1 machining. 4+1 refers to the use of four simultaneous axes plus one axis that is used for positioning only. 4+1 or 5-face machining is a step up from 3-axis machining where just 1 or 2 sides of the part are machined per setup. 4+1 machining allows the part to be machined on 5 faces in one single set up. The part remains in one fixture instead of being moved from one fixture or vise to another, drastically reducing setup time while improving accuracy.
The GX 250 5F (4+1) with travels of 11.8" x 15.6" x 16.9" (X,Y,Z) provides fast rapid traverse of 1181 inches per minute on X, Y and Z axes and features a powerful 20hp, 15,000-rpm direct-drive spindle motor with 70.4 ft-lbs of torque and a 30-tool swing-arm automatic tool changer. The larger GXR 320 5F (4+1) with travels of 20" x 24" x 20" (X,Y,Z) provides very fast rapid traverse of 1693 inches per minute on X and Y axes and 1417 inches per minute on the Z axis. The machine features a powerful 25hp, 12,000-rpm direct-drive spindle with 86.3 ft-lbs of torque and a 48-tool swing-arm automatic toolchanger.
Bridgeport 5-Face (4+1) Machining Centers feature an integrated 5-axis robust rotary table supported by large bearings to allow heavy horizontal and vertical cutting loads with smooth and accurate rotation at all times. Bridgeport incorporates heavy-duty linear guideways and oversized double-nut ballscrews that are pre-tensioned to provide superior accuracy and repeatability. The linear way modules consist of slide members (guide trucks) and linear rails to provide a large load rating, stable accuracy, high rigidity and low friction. The wide spacing between all axes rails provides optimum stiffness for the overall machine structure. Oversized 45mm (1.77") ballscrews are featured in the GXR 320 5F, while 32mm (1.26") ballscrews are incorporated in the GX 250 5F. All of these robust features are designed into a small cost-effective footprint.
Bridgeport 5-Face (4+1) Machining Centers have a work envelope to machine small to medium parts. Machines with larger work envelopes use a larger rotary table, increasing the size of the machine, increasing the overall cost. Bridgeport offers a smaller footprint machine for 5-face machining that is ideal for the medical and dental market and that complements the automotive, aerospace and other industries as well.
Both machines come packed with standard features including a BIG-PLUS spindle, oil chiller, chip conveyor, coolant flush system, preparation for through spindle coolant (with rotary union), coolant wash down gun, tri-color stack light and many standard control features.
"These new Bridgeport 5-Face (4+1) Machining Centers offer a high degree of sophistication and functionality in a small footprint at an attractive price," states Andy McNamara, Director of Sales and Marketing, North America. "Like all Bridgeport machining centers, these machines reflect Hardinge's commitment to quality and performance without compromise."
Contact Details
Related Glossary Terms
- automatic toolchanger
automatic toolchanger
Mechanism typically included in a machining center that, on the appropriate command, removes one cutting tool from the spindle nose and replaces it with another. The changer restores the used tool to the magazine and selects and withdraws the next desired tool from the storage magazine. The changer is controlled by a set of prerecorded/predetermined instructions associated with the part(s) to be produced.
- centers
centers
Cone-shaped pins that support a workpiece by one or two ends during machining. The centers fit into holes drilled in the workpiece ends. Centers that turn with the workpiece are called “live” centers; those that do not are called “dead” centers.
- coolant
coolant
Fluid that reduces temperature buildup at the tool/workpiece interface during machining. Normally takes the form of a liquid such as soluble or chemical mixtures (semisynthetic, synthetic) but can be pressurized air or other gas. Because of water’s ability to absorb great quantities of heat, it is widely used as a coolant and vehicle for various cutting compounds, with the water-to-compound ratio varying with the machining task. See cutting fluid; semisynthetic cutting fluid; soluble-oil cutting fluid; synthetic cutting fluid.
- fixture
fixture
Device, often made in-house, that holds a specific workpiece. See jig; modular fixturing.
- inches per minute ( ipm)
inches per minute ( ipm)
Value that refers to how far the workpiece or cutter advances linearly in 1 minute, defined as: ipm = ipt 5 number of effective teeth 5 rpm. Also known as the table feed or machine feed.
- rapid traverse
rapid traverse
Movement on a CNC mill or lathe that is from point to point at full speed but, usually, without linear interpolation.
- stiffness
stiffness
1. Ability of a material or part to resist elastic deflection. 2. The rate of stress with respect to strain; the greater the stress required to produce a given strain, the stiffer the material is said to be. See dynamic stiffness; static stiffness.
- toolchanger
toolchanger
Carriage or drum attached to a machining center that holds tools until needed; when a tool is needed, the toolchanger inserts the tool into the machine spindle. See automatic toolchanger.
- work envelope
work envelope
Cube, sphere, cylinder or other physical space within which the cutting tool is capable of reaching.