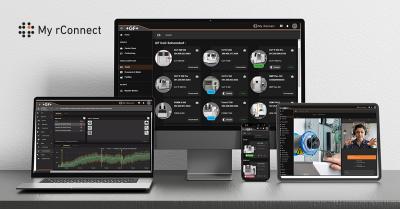
To ensure all customers and their machines benefit from digital assistance, GF Machining Solutions (GFMS) has launched its new My rConnect platform engineered for the company’s EDM, milling and laser texturing machines. The all-encompassing platform allows shops to connect any model of GFMS machine for fast, responsive and easily accessible service and support while also providing expanded digital capabilities.
Prior to My rConnect, shops were required to have a connection between a machine and the rConnect software. Additionally, a separate dedicated PC – other than the machine’s – was needed to run the software and to access the Internet to connect with GFMS technicians.
Now, My rConnect is completely cloud-based, so as long as a computer is connected to the same network as their current GFMS machine, that machine is connected to My rConnect. However, GFMS machines that don’t have network access and are connected to the Internet can also use My rConnect.
With My rConnect, machines are connected without having them connected, per se. As such, shops gain the ability to contact GFMS for service calls for machines that previously weren’t connected by the older PC version of rConnect software. With this capability, they can update a machine’s profile with any service information, record repair issues, obtain updated machine documentation and much more.
A key benefit of bypassing the need for a direct connection is security. My rConnect is password protected and includes an extended level of protection where the system verifies user identity via text message or email code.
The GFMS My rConnect provides a virtual link between a machine and the company’s service and support team, often eliminating the need for a technician to travel to a customer’s shop. When problems occur with those machines that are networkable, shops create an event for that issue, and a service engineer will log in and ask for permission to access and view the machine via the live Remote Assist function to diagnose problems at the machine level.
For nonnetworkable GFMS machines, the process is basically the same. However, once a GFMS service engineer connects using Remote Assist, the operator and GFMS service engineer can use the My rConnect audio/video/chat/ and whiteboard to communicate and resolve the problem.
From these types of service calls, GFMS can record data for how a particular service problem was resolved. If that same problem occurs but with a different customer, this data base of information allows the service engineer to quickly fix and/or diagnose the problem.
Within My rConnect, users can create groups, such as for the machines in various production facility locations. Once done, they can request any related documentation, such as manuals, for a particular machine. Instead of service having to send it, customers with My rConnect-connected machines can simply download needed documentation.
With a machine network connected to My rConnect, shops gain more digital capability. This includes access to current and future developed applications (apps) that enhance the capabilities of customer machines, and the platform makes new or updated apps easy to acquire. GFMS can push the new apps or application update directly to a customer’s machines, notifying them when they log into a particular machine.
One such app is a new version of the company’s Job Recorder now for Wire EDMs and a version for its milling machines. The app lets shops record all the jobs they’ve done to generate efficiency reports based on how much time during the course of a day a machine worked on certain jobs.
Another extremely useful app is the Machine Dashboard. It shows real time machine status – whether it’s running, paused or off. For machines running, it shows the job being done and how long the machine has been working on it in addition to all the previous jobs that have been processed on that particular machine and how long each of those have taken.
Central communications platforms such as My rConnect provide fast and comprehensive IIoT connectivity, and according to Chris Jones, President of GF Machining Solutions North America and Mexico, systems such as My rConnect have special appeal in industries such as aerospace, defense and medical part production in particular, that are under constant pressure to record information and validate machining processes.
“Direct Internet connectivity,” he said, “represents the future of end user-machine builder relationships, and the goal of platforms such as My rConnect is to ensure that a shop’s machine is running, cutting parts and generating profit for the maximum amount of time available.”
Contact Details
Related Glossary Terms
- electrical-discharge machining ( EDM)
electrical-discharge machining ( EDM)
Process that vaporizes conductive materials by controlled application of pulsed electrical current that flows between a workpiece and electrode (tool) in a dielectric fluid. Permits machining shapes to tight accuracies without the internal stresses conventional machining often generates. Useful in diemaking.
- gang cutting ( milling)
gang cutting ( milling)
Machining with several cutters mounted on a single arbor, generally for simultaneous cutting.
- milling
milling
Machining operation in which metal or other material is removed by applying power to a rotating cutter. In vertical milling, the cutting tool is mounted vertically on the spindle. In horizontal milling, the cutting tool is mounted horizontally, either directly on the spindle or on an arbor. Horizontal milling is further broken down into conventional milling, where the cutter rotates opposite the direction of feed, or “up” into the workpiece; and climb milling, where the cutter rotates in the direction of feed, or “down” into the workpiece. Milling operations include plane or surface milling, endmilling, facemilling, angle milling, form milling and profiling.