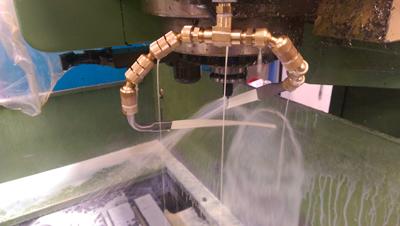
Chip evacuation on a machining center has been key to part quality, finish and integrity. For years, plastic line and metal tubing were the only way to flush the chips away as they were being cut. Then cold air, high-pressure coolant delivery and other methods followed.
Coherent jet coolant delivery has been around for over a decade. It has been used predominantly in grinding. But what would happen if it was applied to machining? Would the results be similar to the changes seen in grinding? Would the machined chips be flushed away faster with better lubrication to the cutting tool?
Recently a test was done using coherent jet coolant delivery on a vertical machining center. The machine uses a 300-psi pump. The material being machined is Inconel. On the original setup four plastic lines were being used and directed to the cut.
The test was looking to achieve several changes in the machining the part: increase tool life, better material integrity after machining and improve part finish. All three were accomplished.
First, the four plastic lines were removed from the coolant manifold and replaced with two coherent jet SwivelJet coolant lines from Productivity Solutions Inc. designed for the test. The new Swiveljet lines being used could be reconfigured easily and were capable of handling the coolant pressure.
The feeds, speeds and depth of cut were kept the same as when the plastic lines were used. Measurements were being taken while the test was being run. Power draw was reduced by over 35 percent. Chatter was lowered to less than a half. And the tool life was doubled.
Given the high nickel content of the part, it can be generalized that other high nickel alloys such as titanium would also benefit greatly from coherent jet coolant delivery. Tests will soon be run on stainless steels that can be difficult to machine such as 17-4 and 400 series medical grades of stainless steel.
Contact Details
Related Glossary Terms
- alloys
alloys
Substances having metallic properties and being composed of two or more chemical elements of which at least one is a metal.
- chatter
chatter
Condition of vibration involving the machine, workpiece and cutting tool. Once this condition arises, it is often self-sustaining until the problem is corrected. Chatter can be identified when lines or grooves appear at regular intervals in the workpiece. These lines or grooves are caused by the teeth of the cutter as they vibrate in and out of the workpiece and their spacing depends on the frequency of vibration.
- coolant
coolant
Fluid that reduces temperature buildup at the tool/workpiece interface during machining. Normally takes the form of a liquid such as soluble or chemical mixtures (semisynthetic, synthetic) but can be pressurized air or other gas. Because of water’s ability to absorb great quantities of heat, it is widely used as a coolant and vehicle for various cutting compounds, with the water-to-compound ratio varying with the machining task. See cutting fluid; semisynthetic cutting fluid; soluble-oil cutting fluid; synthetic cutting fluid.
- depth of cut
depth of cut
Distance between the bottom of the cut and the uncut surface of the workpiece, measured in a direction at right angles to the machined surface of the workpiece.
- grinding
grinding
Machining operation in which material is removed from the workpiece by a powered abrasive wheel, stone, belt, paste, sheet, compound, slurry, etc. Takes various forms: surface grinding (creates flat and/or squared surfaces); cylindrical grinding (for external cylindrical and tapered shapes, fillets, undercuts, etc.); centerless grinding; chamfering; thread and form grinding; tool and cutter grinding; offhand grinding; lapping and polishing (grinding with extremely fine grits to create ultrasmooth surfaces); honing; and disc grinding.
- machining center
machining center
CNC machine tool capable of drilling, reaming, tapping, milling and boring. Normally comes with an automatic toolchanger. See automatic toolchanger.
- stainless steels
stainless steels
Stainless steels possess high strength, heat resistance, excellent workability and erosion resistance. Four general classes have been developed to cover a range of mechanical and physical properties for particular applications. The four classes are: the austenitic types of the chromium-nickel-manganese 200 series and the chromium-nickel 300 series; the martensitic types of the chromium, hardenable 400 series; the chromium, nonhardenable 400-series ferritic types; and the precipitation-hardening type of chromium-nickel alloys with additional elements that are hardenable by solution treating and aging.