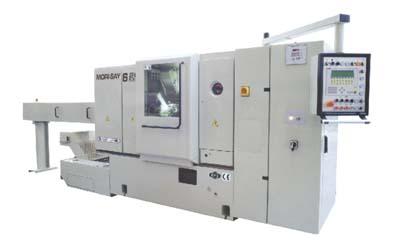
ZPS America LLC's cam-driven 6-spindle automatic lathe has a 20mm bar capacity. The rigid, European-built machine is for continuous or series production of precision turned parts. Solid base casting ensures maximum rigidity and stability, according to the company. The machine includes six frontal slides with up to 110 working strokes, and six cross slides plus four compound slides with clamping, and bar stop in the sixth station. An independent cam controls each slide. Stroke is adjustable on the rocker arm of the corresponding drive. Machines in the range are provided with different spindle speed ranges, depending on material type and size. Four safety clutches prevent the slides from overloading. Spindle drum locking is accomplished by a Hirth coupling for repeatability and precision. A bar stock guide is standard, and the machine can also include automatic bar loaders and bar magazines for long, unattended operation. Spindles are driven by Simodrive Siemens variable-speed motors and the machines are controlled through a Siemens S7. To accomplish nearly any operation, the machines can be provided with a wide range of optional equipment, including NC drive of the pickup spindle, bar stock feeding and clamping in the fourth station, attachments for high-speed drilling, reaming, tapping and broaching, and multispindle drilling heads on the frontal slides.
Contact Details
Related Glossary Terms
- broaching
broaching
Operation in which a cutter progressively enlarges a slot or hole or shapes a workpiece exterior. Low teeth start the cut, intermediate teeth remove the majority of the material and high teeth finish the task. Broaching can be a one-step operation, as opposed to milling and slotting, which require repeated passes. Typically, however, broaching also involves multiple passes.
- computer-aided manufacturing ( CAM)
computer-aided manufacturing ( CAM)
Use of computers to control machining and manufacturing processes.
- lathe
lathe
Turning machine capable of sawing, milling, grinding, gear-cutting, drilling, reaming, boring, threading, facing, chamfering, grooving, knurling, spinning, parting, necking, taper-cutting, and cam- and eccentric-cutting, as well as step- and straight-turning. Comes in a variety of forms, ranging from manual to semiautomatic to fully automatic, with major types being engine lathes, turning and contouring lathes, turret lathes and numerical-control lathes. The engine lathe consists of a headstock and spindle, tailstock, bed, carriage (complete with apron) and cross slides. Features include gear- (speed) and feed-selector levers, toolpost, compound rest, lead screw and reversing lead screw, threading dial and rapid-traverse lever. Special lathe types include through-the-spindle, camshaft and crankshaft, brake drum and rotor, spinning and gun-barrel machines. Toolroom and bench lathes are used for precision work; the former for tool-and-die work and similar tasks, the latter for small workpieces (instruments, watches), normally without a power feed. Models are typically designated according to their “swing,” or the largest-diameter workpiece that can be rotated; bed length, or the distance between centers; and horsepower generated. See turning machine.
- numerical control ( NC)
numerical control ( NC)
Any controlled equipment that allows an operator to program its movement by entering a series of coded numbers and symbols. See CNC, computer numerical control; DNC, direct numerical control.
- tapping
tapping
Machining operation in which a tap, with teeth on its periphery, cuts internal threads in a predrilled hole having a smaller diameter than the tap diameter. Threads are formed by a combined rotary and axial-relative motion between tap and workpiece. See tap.