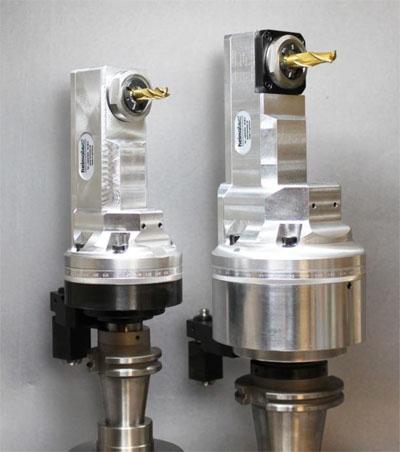
Heimatec announces immediate availability of its popular U-tec flexible adapter system on all right-angle heads in the company's line. Models are now available for most popular lines of machine tools in the North American market, according to company President Preben Hansen. The company plans to include its U-tec adapter system on all angle heads, going forward, according to Hansen. He notes this development will especially provide the system's rigidity and quick-change capabilities to users doing deep hole drilling with extended tools.
U-tec is the company's patented flexible tool adapter system that allows a standard ER output live tool to accept various adapters for different applications. This allows users the ability to have quick changeover of tools on almost any lathe or mill, using a single live tool, without having to commit to a quick-change system on the initial purchase. A facemill adapter, for example, can be quickly positioned into the standard holder, without the need for a completely new base being installed. This significantly reduces inventory costs as well as changeover time, for the busy shop.
The U-tec system, according to Preben Hansen, represents a real improvement in lathe and mill/turn tooling design. "U-tec allows great user flexibility, while a polygonal drive system ensures extremely high power transmission stability and faster set-up with absolutely no loss in performance or accuracy, because the live tool base remains in position and only the adapter and collet get swapped out."
He went on to explain the unique collet nuts on the U-tec system have internal threading for rigid mounting and that this new tool adapter system enables the actual cutting tool to be brought into closer proximity to the bearing, thus further improving performance in use. This benefit results from the short and compact tool length design. Internal coolant up to 2000 psi (140 bar) is provided as standard.
Every adapter in the U-tec system, complete with any necessary clamping nuts and adapters for arbor, Weldon, CAT 40 and CAT 50, is now available in shell mill, face mill, ER extension, side lock, shrink fit, hydraulic and blank styles. U-tec angle heads are compatible with most automatic tool changers, feature 360º manual positioning and include torque arms and a stop block. Torque rated up to 150 Nm (110 ft-lb).
Contact Details
Related Glossary Terms
- arbor
arbor
Shaft used for rotary support in machining applications. In grinding, the spindle for mounting the wheel; in milling and other cutting operations, the shaft for mounting the cutter.
- collet
collet
Flexible-sided device that secures a tool or workpiece. Similar in function to a chuck, but can accommodate only a narrow size range. Typically provides greater gripping force and precision than a chuck. See chuck.
- coolant
coolant
Fluid that reduces temperature buildup at the tool/workpiece interface during machining. Normally takes the form of a liquid such as soluble or chemical mixtures (semisynthetic, synthetic) but can be pressurized air or other gas. Because of water’s ability to absorb great quantities of heat, it is widely used as a coolant and vehicle for various cutting compounds, with the water-to-compound ratio varying with the machining task. See cutting fluid; semisynthetic cutting fluid; soluble-oil cutting fluid; synthetic cutting fluid.
- facemill
facemill
Milling cutter for cutting flat surfaces.
- lathe
lathe
Turning machine capable of sawing, milling, grinding, gear-cutting, drilling, reaming, boring, threading, facing, chamfering, grooving, knurling, spinning, parting, necking, taper-cutting, and cam- and eccentric-cutting, as well as step- and straight-turning. Comes in a variety of forms, ranging from manual to semiautomatic to fully automatic, with major types being engine lathes, turning and contouring lathes, turret lathes and numerical-control lathes. The engine lathe consists of a headstock and spindle, tailstock, bed, carriage (complete with apron) and cross slides. Features include gear- (speed) and feed-selector levers, toolpost, compound rest, lead screw and reversing lead screw, threading dial and rapid-traverse lever. Special lathe types include through-the-spindle, camshaft and crankshaft, brake drum and rotor, spinning and gun-barrel machines. Toolroom and bench lathes are used for precision work; the former for tool-and-die work and similar tasks, the latter for small workpieces (instruments, watches), normally without a power feed. Models are typically designated according to their “swing,” or the largest-diameter workpiece that can be rotated; bed length, or the distance between centers; and horsepower generated. See turning machine.
- milling machine ( mill)
milling machine ( mill)
Runs endmills and arbor-mounted milling cutters. Features include a head with a spindle that drives the cutters; a column, knee and table that provide motion in the three Cartesian axes; and a base that supports the components and houses the cutting-fluid pump and reservoir. The work is mounted on the table and fed into the rotating cutter or endmill to accomplish the milling steps; vertical milling machines also feed endmills into the work by means of a spindle-mounted quill. Models range from small manual machines to big bed-type and duplex mills. All take one of three basic forms: vertical, horizontal or convertible horizontal/vertical. Vertical machines may be knee-type (the table is mounted on a knee that can be elevated) or bed-type (the table is securely supported and only moves horizontally). In general, horizontal machines are bigger and more powerful, while vertical machines are lighter but more versatile and easier to set up and operate.
- threading
threading
Process of both external (e.g., thread milling) and internal (e.g., tapping, thread milling) cutting, turning and rolling of threads into particular material. Standardized specifications are available to determine the desired results of the threading process. Numerous thread-series designations are written for specific applications. Threading often is performed on a lathe. Specifications such as thread height are critical in determining the strength of the threads. The material used is taken into consideration in determining the expected results of any particular application for that threaded piece. In external threading, a calculated depth is required as well as a particular angle to the cut. To perform internal threading, the exact diameter to bore the hole is critical before threading. The threads are distinguished from one another by the amount of tolerance and/or allowance that is specified. See turning.