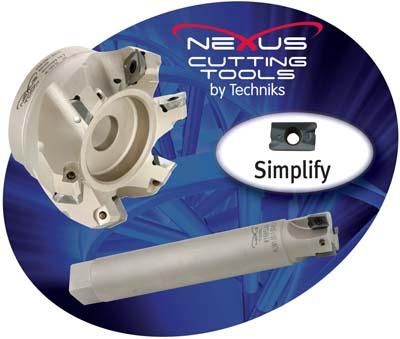
Techniks Inc.'s lineup of Nexus Cutting Tools includes face mills that feature an innovative shrink-fit connection to the arbor (ShrinkMILL), indexable end mills that also can be shrink-fit into a holder (PowerLOC), and high-performance inserts for milling, turning, and boring. These new inserts feature a patented PVD application process and advanced edge geometries by Lamina Technologies that permits insert coatings up to 5X thicker than current technology for greater feeds and speeds, improved surface finish and greatly extended insert life.
According to John Stagge President of Techniks: "Patented advances we have made in ShrinkFIT toolholder design eliminate the poor arbor tolerance of face mills, and toolholder imbalance associated with end mill holders. The PowerLOC end mill and ShrinkMILL face mills, both make a perfected ShrinkFIT connection with the toolholder, providing the same high-performance and extended tool life that regular ShrinkFIT brought to carbide cutting tools 20 years ago. Combined with our new high-performance inserts, the cost-savings and performance benefits Nexus Cutting Tools provides is unequaled in the industry."
ShrinkMILL technology removes the tolerance between the face mill and the arbor, and features a patented ShrinkFIT tool change, bringing the rigidity, holding power, and near-perfect runout of ShrinkFIT to face milling applications. ShrinkMILL face mills provide 30 percent better T.I.R., increased insert life, improved surface finish, (eliminate or reduce finish passes) and faster metal removal rates.
PowerLOC indexable end mills feature a shank that is manufactured to ShrinkFIT tolerances, and also has a square-end that positively engages with the toolholder body to prevent spinning the tool. Use PowerLOC end mills with a ShrinkLOC holder for maximum rigidity, accuracy, and holding power. The advantages that a ShrinkFIT connection provides (faster speeds and feeds, longer insert life, better surface finish) yield cost savings that other end mill holders cannot match.
PowerLOC end mills can also be used with a Techniks collet chuck (equipped with a PowerLOC adapter) for substantial performance gains and insert life compared to end mill holders. PowerLOC technology turns Techniks collet chucks into highly accurate milling chucks, with much greater accuracy and balance then end mill holders can provide.
Contact Details
Related Glossary Terms
- arbor
arbor
Shaft used for rotary support in machining applications. In grinding, the spindle for mounting the wheel; in milling and other cutting operations, the shaft for mounting the cutter.
- boring
boring
Enlarging a hole that already has been drilled or cored. Generally, it is an operation of truing the previously drilled hole with a single-point, lathe-type tool. Boring is essentially internal turning, in that usually a single-point cutting tool forms the internal shape. Some tools are available with two cutting edges to balance cutting forces.
- chuck
chuck
Workholding device that affixes to a mill, lathe or drill-press spindle. It holds a tool or workpiece by one end, allowing it to be rotated. May also be fitted to the machine table to hold a workpiece. Two or more adjustable jaws actually hold the tool or part. May be actuated manually, pneumatically, hydraulically or electrically. See collet.
- collet
collet
Flexible-sided device that secures a tool or workpiece. Similar in function to a chuck, but can accommodate only a narrow size range. Typically provides greater gripping force and precision than a chuck. See chuck.
- gang cutting ( milling)
gang cutting ( milling)
Machining with several cutters mounted on a single arbor, generally for simultaneous cutting.
- milling
milling
Machining operation in which metal or other material is removed by applying power to a rotating cutter. In vertical milling, the cutting tool is mounted vertically on the spindle. In horizontal milling, the cutting tool is mounted horizontally, either directly on the spindle or on an arbor. Horizontal milling is further broken down into conventional milling, where the cutter rotates opposite the direction of feed, or “up” into the workpiece; and climb milling, where the cutter rotates in the direction of feed, or “down” into the workpiece. Milling operations include plane or surface milling, endmilling, facemilling, angle milling, form milling and profiling.
- milling machine ( mill)
milling machine ( mill)
Runs endmills and arbor-mounted milling cutters. Features include a head with a spindle that drives the cutters; a column, knee and table that provide motion in the three Cartesian axes; and a base that supports the components and houses the cutting-fluid pump and reservoir. The work is mounted on the table and fed into the rotating cutter or endmill to accomplish the milling steps; vertical milling machines also feed endmills into the work by means of a spindle-mounted quill. Models range from small manual machines to big bed-type and duplex mills. All take one of three basic forms: vertical, horizontal or convertible horizontal/vertical. Vertical machines may be knee-type (the table is mounted on a knee that can be elevated) or bed-type (the table is securely supported and only moves horizontally). In general, horizontal machines are bigger and more powerful, while vertical machines are lighter but more versatile and easier to set up and operate.
- physical vapor deposition ( PVD)
physical vapor deposition ( PVD)
Tool-coating process performed at low temperature (500° C), compared to chemical vapor deposition (1,000° C). Employs electric field to generate necessary heat for depositing coating on a tool’s surface. See CVD, chemical vapor deposition.
- shank
shank
Main body of a tool; the portion of a drill or similar end-held tool that fits into a collet, chuck or similar mounting device.
- tolerance
tolerance
Minimum and maximum amount a workpiece dimension is allowed to vary from a set standard and still be acceptable.
- toolholder
toolholder
Secures a cutting tool during a machining operation. Basic types include block, cartridge, chuck, collet, fixed, modular, quick-change and rotating.
- turning
turning
Workpiece is held in a chuck, mounted on a face plate or secured between centers and rotated while a cutting tool, normally a single-point tool, is fed into it along its periphery or across its end or face. Takes the form of straight turning (cutting along the periphery of the workpiece); taper turning (creating a taper); step turning (turning different-size diameters on the same work); chamfering (beveling an edge or shoulder); facing (cutting on an end); turning threads (usually external but can be internal); roughing (high-volume metal removal); and finishing (final light cuts). Performed on lathes, turning centers, chucking machines, automatic screw machines and similar machines.