Debating the need for CAM systems on Swiss-style machines.
As CNC machine tools become increasingly complex, so does the job of programming them. CNC Swiss-style machines are no exception. With more tools than the Snap-On truck and tighter quarters than a World War II submarine, many shops view them as coding nightmares.
Yet the bane of these machines—their complexity—is often a boon. With stations aplenty, it’s likely that some of the needed tools already reside in one of the machine’s many turrets or slides, reducing setup time. Because the parts made on a Swiss-style machine are relatively small, stock removal is minimal—program a single pass and you’re done. And Swiss-style machine builders have incorporated cool features, such as synchronization codes and automatic axis mirroring into their machine controls, simplifying manual programming.
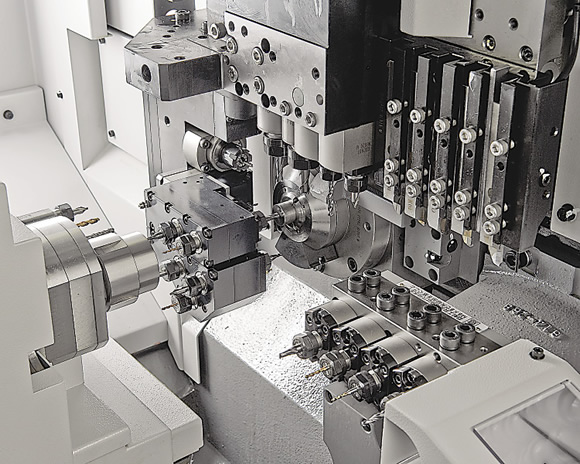
Courtesy of Marubeni Citizen-Cincom
With seven cutting axes and up to 32 tools, the L20E Swiss-style machine from Marubeni Citizen-Cincom might be a challenge to program manually.
An experienced Swiss setup person can often program at the machine and have the first part in inspection faster than programming it in a CAM system, according to Brian Such, an Elk Grove Village, Ill.-based customer support group manager for machine builder Marubeni Citizen-Cincom Inc., Allendale, N.J. “In many shops, the parts are pretty straightforward, so programming means turn, drill and cut off,” he said. “It’s not that difficult.”
Despite his hands-on perspective, Such warned that traditional programming tasks are changing. As shops become more diverse in terms of machine capability, manual programming methods may be going the way of paper tape.
“The whole world wants to go CAM, and our customers are increasingly looking for people who can go cross-platform,” Such said. This means some underpaid soul has to program Swiss-style machines one day, wire EDMs the next and 5-axis machining centers after that. Programmers often multitask more than the machine tools they program.
Send in the CAMs
Someone who’s participated in the evolution of Swiss programming is Don Davies, director of sales and application engineering for DP Technology Corp. He admitted that a seasoned setup person might be able to whip out a manual program quickly, but stated that CAM systems offer benefits beyond just code generation. Multitask machines in general require synchronization, and Swiss-style machines are the mothers of multitasking. And simulating machine movements before the first chips fly can cut setup time and avoid costly crashes.
Davies said, “Even on parts that are simple to program, simulating the machine setup—seeing axis movements, how the tools are plugged in and if there are any potential violations—can be very valuable.”
DP Technology Corp., Camarillo, Calif., has been developing ESPRIT CAM software for Swiss-style machines since the mid-1990s. Twenty years ago, shops were still seeing orders for a gazillion parts, and setup time wasn’t a huge concern. But the market has changed.
“Today, you see orders of 50 parts and they’re (often) far more complex than 20 years ago,” Davies said. “That combination means you need a CAM system to stay competitive.” DP Technology serves this market with its ESPRIT CAM product, with features such as B-axis support, G-code optimization, pinch milling and several flavors of axis synchronization.
Good functionality is important, but one of the most important attributes of any CAM system is its post-processor. “We’re talking about the engine,” Davies said. “It sits within the CAM software, building the code and performing the synchronization and process planning. Regardless of the operations you’re going to perform on the Swiss machine, the post has to handle them. The goal is to push a button and see G code, with no edits required. It’s not simple.”
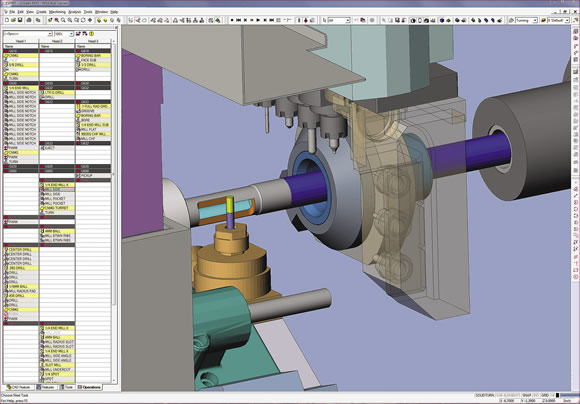
Courtesy of DP Technology
DP Technology’s ESPRIT CAM software shows three-channel simultaneous simulation of a rifle bolt carrier being machined on a Citizen M32 Swiss-style machine.
To that end, DP Technology offers post-processors for all major brands of Swiss-style machines in all their various configurations. Yet Davies said machine builders are busy dreaming up even better mousetraps. “I’m hearing noises that they’re planning to release even more complex machines.”
This doesn’t necessarily mean more axes or more tools, but more capability. One example of this is simultaneous 5-axis machining. Where 3-axis milling on a Swiss-style machine was unusual just a few years ago, builders have introduced 5-axis milling capability. “Who knows what the future’s going to be?” Davies asked.
David Green, manufacturing engineer at FMI Hansa Medical Products LLC, Madison, Ala., has been using ESPRIT since 2007. The shop manufactures a variety of bone screws, dental implants and cardiovascular components in titanium and cobalt-chrome alloys. With 10 Swiss-style machines to manage, the largest of which is a 7-axis, 32mm machine, Green is busy.
“Before ESPRIT, we would key in all the programs by hand,” Green said. “This isn’t as complicated as you might think, because you can program one axis at a time and use the built-in synch codes to marry the different axes. But still, it would take us an hour or two to enter each program and debug it.”
FMI Hansa’s work has evolved since 2007. Not only are there more machines to program, but the parts have become more challenging. That’s because the shop’s CAM system has created new business opportunities by allowing it to take full advantage of the Swiss machines’ multiaxis capabilities. Where manual programming methods once limited them to 2-D features, they are now able to generate complex geometries with 3-D sculpting and 4-axis simultaneous cutting.
“Obviously, we couldn’t make those kinds of parts before,” Green said. “And with the programming now done offline, machine output has increased. We don’t have to stand in front of the machine for hours at a time, keying in code. Now, the setup technician pulls the program in via Ethernet and it’s basically ready to run. Looking back, I’d say we were really limiting ourselves with manual programming.”
Chicken or the Egg?
Someone who agrees wholeheartedly with that opinion is Gary Hargreaves, vice president of business development for CNC Software Inc., Tolland, Conn., the developer of Mastercam. A relative newcomer to the Swiss market, CNC Software entered the fray in 2010 by acquiring the assets of Jurasoft SA, a Switzerland-based company known for its Swiss-specific CAM system, SylvieXpert.
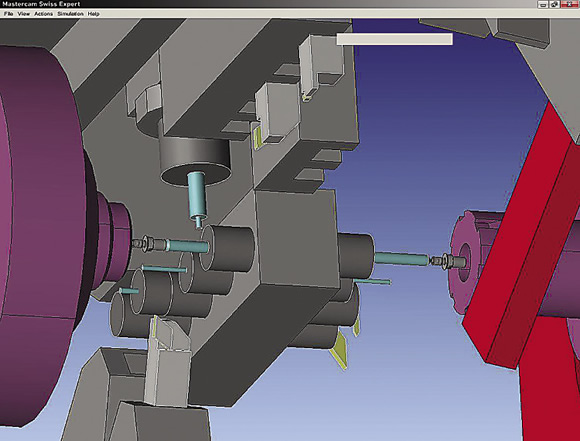
Courtesy of CNC Software
A representation of multiaxis machining with Mastercam Swiss Expert’s built-in simulation capability.
“I managed the acquisition and staffing of the development office in Switzerland,” Hargreaves said. “It’s been my responsibility from the beginning, and I am still in charge of the product and the project.”
That project is going well, according to Hargreaves, and sales have steadily increased. Now marketed under the brand name Swiss Expert, the software is for multiple-axis operations. “One thing CAM shoppers should look for is the number of channels [axes] the software can support,” he said. “As machine builders continue to add complexity, it’s critical that your CAM system can keep up.”
Because Swiss-style machines are busier than the proverbial rooster in a hen house, ease of synchronization is also an important feature. Swiss Expert uses a “sync manager” to pull together the different channels so an operator can build the sequence of manufacturing events. “There isn’t any level of automatic synchronization,” Hargreaves said. “You develop your toolpaths in a linear fashion, in the order that you would expect them to happen on the machine. When this is completed, you go into the sync manager and tell the software you want this to start before that, move this over there, wait so many seconds before handing off to the subspindle and so on. It’s a pretty easy process.”
Although CNC Software considered developing its own Swiss CAM system, Hargreaves said the company was concerned about unseen knowledge gaps in its programming team and the possibility of expensive rewrites. CNC Software realized that Swiss programming isn’t just a matter of laying a milling module on top of a turning module. “We saw one competitor have to start over after several years of development,” he said.
Another factor was industry need. When CNC Software first began its market analysis, there wasn’t much call for Swiss programming systems. “Most of our customers were running plain-Jane lathes and mills, and we had that well covered with Mastercam,” Hargreaves said. “Since then, however, everything has changed.”
Within the past 5 years, more “traditional” machine shops have added Swiss-style machines to their equipment lists. “It used to be all Swiss or no Swiss,” Hagreaves said. “But companies today are realizing the advantage of sliding headstock machines for small, difficult parts.”
This machine tool inbreeding is a classic case of the chicken or the egg—easy-to-use CAM systems make Swiss-style machines more appealing, while the rise in demand for low-volume, complex parts basically mandates a CAM system.
Seeing is Believing
Both ESPRIT and Swiss Expert utilize simulation as their primary method of program prove-out. These systems represent machine movement before the G code is ever generated, using what’s known as CL (cutter location) data, or internal software output. The CAM operator never sees the actual toolpaths until the machine executes the code. CAM vendors say this is more than adequate in most cases. Yet CNC Software’s Hargreaves argued that many of its customers don’t even bother with toolpath simulation, citing “not enough time” as the reason.
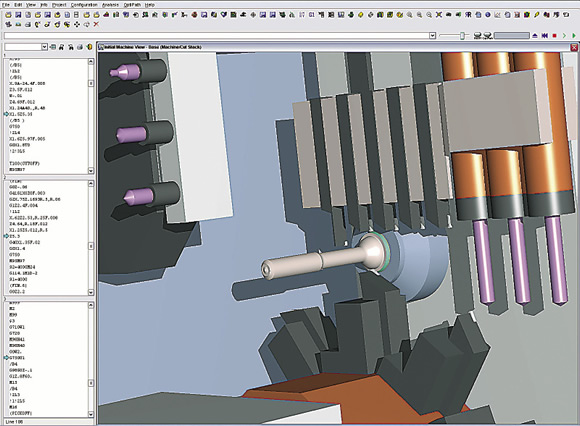
Courtesy of CGTech
Simulation software, such as CGTech’s Vericut (shown here), provides an accurate representation of what will happen on the production floor before committing an expensive Swiss-style machine tool to an unverified toolpath.
Simulation software company CGTech Inc., Irvine, Calif., disagrees with this approach. “You need an accurate representation of what’s going to happen on the production floor before you push cycle start and commit an expensive machine tool to an unverified toolpath,” said Bill Hasenjaeger, product marketing manager for CGTech.
That insurance doesn’t come cheaply. At roughly $20,000 per seat, CGTech’s Vericut can cost more than many shops can afford. Hasenjaeger noted many of the company’s customers are large aerospace and automotive manufacturers that want to avoid scrapping expensive titanium workpieces or mold cavities, relying on the software to show unexpected gouging or interference.
On the flip side, Swiss shops, with their small parts, think nothing of losing a few setup pieces. Why bother with machine simulation? Hasenjaeger fights this mindset with a question of his own: What about protecting the machine? “Everything today is moving faster, and Swiss machines, with their tight work areas and multiple tools engaged simultaneously, make it very hard to catch a crash before it happens,” he said. “Lose a spindle or wreck a turret and you’re looking at a lot more than the 20 grand you could have spent to prevent it.”
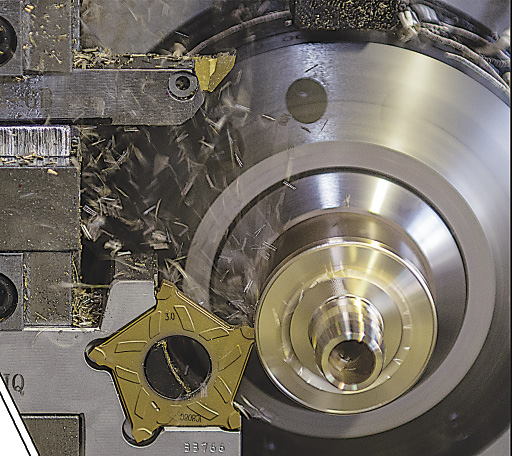
Courtesy of CNC Software
A cutoff operation on a Swiss-style machine.
Obviously, many CAM developers feel the same way. Hasenjaeger provided a list of CAM software companies that have developed interfaces to Vericut, including Mastercam, EdgeCAM, ESPRIT, SurfWare and Delcam. Every one of these programs has built-in simulation, so why buy an additional bolt-on product? The answer, according to Hasenjaeger, is accuracy. “We have thousands of simulation customers around the world. These companies are looking for the next level of NC-code visualization and can justify the additional expense for the reasons just mentioned.”
CGTech also works with machine builders, providing preconfigured 3-D models of most Swiss-style machines. One is Marubeni Citizen-Cincom, according to Such. He may not always see the need for CAM software, but said customers are definitely looking for better tools to envision toolpaths and improve part processing. “Especially when you get into milling or very complex workpieces, you want to see what’s going on.”
While the use of these software tools, including CAM systems, is on the rise, Such suggested waiting a few months to get a CAM system after buying a Swiss-style machine. “You must know how to process parts on a Swiss machine, and the only way to learn that is to program the hard way for a while,” he said. “Once you get that under your belt, the CAM system will make you faster and more efficient and help eliminate human mistakes.”
Swiss CAM systems cost more than 2-axis turning and 3-axis milling packages, but the expense is justified because of their additional functionality. In any event, you’re going to drop some serious cash on a new programming package, and even more if you opt for high-end simulation software. Is it worth it? The answer depends on a number of factors, including part complexity, sales volume and operator skill level. In today’s increasingly competitive environment, you owe it to yourself to take a look. CTE
Contributors
CGTech Inc.
(949) 753-1050
www.cgtech.com
CNC Software Inc.
(800) 228-2877
www.mastercam.com
DP Technology Corp.
(800) 627-8479
www.dptechnology.com
FMI Hansa Medical Products LLC
(256) 461-0900
www.fmihansa.com
Marubeni Citizen-Cincom Inc.
(201) 818-0100
www.marucit.com
Related Glossary Terms
- 2-D
2-D
Way of displaying real-world objects on a flat surface, showing only height and width. This system uses only the X and Y axes.
- 3-D
3-D
Way of displaying real-world objects in a natural way by showing depth, height and width. This system uses the X, Y and Z axes.
- alloys
alloys
Substances having metallic properties and being composed of two or more chemical elements of which at least one is a metal.
- centers
centers
Cone-shaped pins that support a workpiece by one or two ends during machining. The centers fit into holes drilled in the workpiece ends. Centers that turn with the workpiece are called “live” centers; those that do not are called “dead” centers.
- computer numerical control ( CNC)
computer numerical control ( CNC)
Microprocessor-based controller dedicated to a machine tool that permits the creation or modification of parts. Programmed numerical control activates the machine’s servos and spindle drives and controls the various machining operations. See DNC, direct numerical control; NC, numerical control.
- computer-aided manufacturing ( CAM)
computer-aided manufacturing ( CAM)
Use of computers to control machining and manufacturing processes.
- cutoff
cutoff
Step that prepares a slug, blank or other workpiece for machining or other processing by separating it from the original stock. Performed on lathes, chucking machines, automatic screw machines and other turning machines. Also performed on milling machines, machining centers with slitting saws and sawing machines with cold (circular) saws, hacksaws, bandsaws or abrasive cutoff saws. See saw, sawing machine; turning.
- gang cutting ( milling)
gang cutting ( milling)
Machining with several cutters mounted on a single arbor, generally for simultaneous cutting.
- milling
milling
Machining operation in which metal or other material is removed by applying power to a rotating cutter. In vertical milling, the cutting tool is mounted vertically on the spindle. In horizontal milling, the cutting tool is mounted horizontally, either directly on the spindle or on an arbor. Horizontal milling is further broken down into conventional milling, where the cutter rotates opposite the direction of feed, or “up” into the workpiece; and climb milling, where the cutter rotates in the direction of feed, or “down” into the workpiece. Milling operations include plane or surface milling, endmilling, facemilling, angle milling, form milling and profiling.
- sawing machine ( saw)
sawing machine ( saw)
Machine designed to use a serrated-tooth blade to cut metal or other material. Comes in a wide variety of styles but takes one of four basic forms: hacksaw (a simple, rugged machine that uses a reciprocating motion to part metal or other material); cold or circular saw (powers a circular blade that cuts structural materials); bandsaw (runs an endless band; the two basic types are cutoff and contour band machines, which cut intricate contours and shapes); and abrasive cutoff saw (similar in appearance to the cold saw, but uses an abrasive disc that rotates at high speeds rather than a blade with serrated teeth).
- toolpath( cutter path)
toolpath( cutter path)
2-D or 3-D path generated by program code or a CAM system and followed by tool when machining a part.
- turning
turning
Workpiece is held in a chuck, mounted on a face plate or secured between centers and rotated while a cutting tool, normally a single-point tool, is fed into it along its periphery or across its end or face. Takes the form of straight turning (cutting along the periphery of the workpiece); taper turning (creating a taper); step turning (turning different-size diameters on the same work); chamfering (beveling an edge or shoulder); facing (cutting on an end); turning threads (usually external but can be internal); roughing (high-volume metal removal); and finishing (final light cuts). Performed on lathes, turning centers, chucking machines, automatic screw machines and similar machines.