Hard-chrome plating (HCP) provides parts, such as ones for the aerospace industry, with a wear- and corrosion-resistant surface but requires the use of hexavalent chromium salts. Those salts are genotoxic carcinogens and pose health and environmental hazards, and, therefore, are restricted in the U.S. by the Occupational Safety and Health Administration and in the European Union by REACH (Registration, Evaluation, Authorization and Restriction of Chemicals).
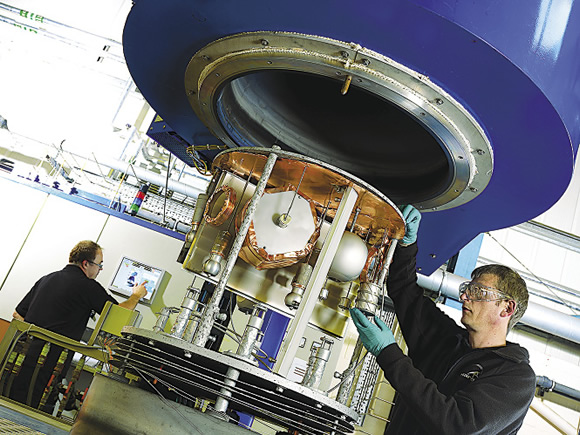
Parts to be coated with Hardide-A are loaded into a CVD coating reactor.
“Hexavalent chromium has been a concern for many years, but the alternatives have always been limited,” said Dan Wilson, business development manager for Hardide Coatings Inc., which offers the Hardide-A coating as an environmentally and worker-friendly alternative to HCP.
Workers applying hexavalent chromium-containing products are exposed the most, particularly when chrome plating because the processing bath produces bubbles, which generate a difficult-to-capture fog, according to Dr. Yuri Zhuk, technical director for U.K.-based Hardide Coatings Ltd.
Hardide-A, on the other hand, is a tungsten carbide-based CVD coating that is applied in a coating reactor, which doesn’t expose workers to environmental hazards. Zhuk added that although spray coatings, such as high-velocity oxy-fuel, are considered the best available alternative to HCP, those are line-of-sight processes that can only be applied to external surfaces because a spray gun can’t fit, for example, into a small bore.
“In the past, hard chrome was often seen as the best option for hardening interior surfaces because spray coatings are difficult or impossible to apply in tight spaces,” Wilson said.
The company stated that the CVD coating’s hardness of 800 to 1,200 HV and standard thickness from 50µm to 100µm (0.002 " to 0.004 ") match the hardness and thickness of HCP, simplifying the transition without the need for part dimensional changes and drawing redesigns. In addition, Zhuk said Hardide-A offers better corrosion resistance because it passed a salt-spray test for 2,000 hours, whereas HCP failed after 280 hours. The Hardide-A coated surface is also free of microcracks, which are always present in HCP. “These microcracks form channels for corrosive media to attack the substrate,” he said.
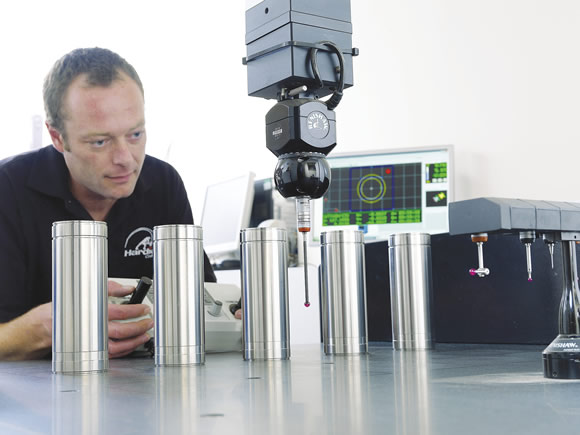
A technician measures parts coated with Hardide-A.
The CVD-coated parts have surface finishes as fine as 0.3µm Ra, but can be ground, honed or lapped, if necessary, Zhuk noted.
The company is working on test programs with customers, including helicopter manufacturer AgustaWestland, Airbus and other aerospace OEMs. According to Hardide Coatings, it has successfully completed the first of two test phases to approve Hardide-A as a replacement for HCP on an AgustaWestland helicopter rotor blade component. The first phase involved testing basic properties, such as corrosion resistance and fatigue life, and the second phase will test actual coated components.
To control quality, the company applies Hardide-A at its coating facilities in Bicester, Oxfordshire, U.K.
For more information about Hardide Coatings Inc., Houston, visit www.har dide.com or call (713) 677-3504. CTE
Related Glossary Terms
- Vickers hardness number ( HV)
Vickers hardness number ( HV)
Number related to the applied load and surface area of the permanent impression made by a square-based pyramidal diamond indenter having included face angles of 136º. The Vickers hardness number is a ratio of the applied load in kgf, multiplied by 1.8544, and divided by the length of diagonal squared.
- chemical vapor deposition ( CVD)
chemical vapor deposition ( CVD)
High-temperature (1,000° C or higher), atmosphere-controlled process in which a chemical reaction is induced for the purpose of depositing a coating 2µm to 12µm thick on a tool’s surface. See coated tools; PVD, physical vapor deposition.
- corrosion resistance
corrosion resistance
Ability of an alloy or material to withstand rust and corrosion. These are properties fostered by nickel and chromium in alloys such as stainless steel.
- fatigue
fatigue
Phenomenon leading to fracture under repeated or fluctuating stresses having a maximum value less than the tensile strength of the material. Fatigue fractures are progressive, beginning as minute cracks that grow under the action of the fluctuating stress.
- fatigue life
fatigue life
Number of cycles of stress that can be sustained prior to failure under a stated test condition.
- hardening
hardening
Process of increasing the surface hardness of a part. It is accomplished by heating a piece of steel to a temperature within or above its critical range and then cooling (or quenching) it rapidly. In any heat-treatment operation, the rate of heating is important. Heat flows from the exterior to the interior of steel at a definite rate. If the steel is heated too quickly, the outside becomes hotter than the inside and the desired uniform structure cannot be obtained. If a piece is irregular in shape, a slow heating rate is essential to prevent warping and cracking. The heavier the section, the longer the heating time must be to achieve uniform results. Even after the correct temperature has been reached, the piece should be held at the temperature for a sufficient period of time to permit its thickest section to attain a uniform temperature. See workhardening.
- hardness
hardness
Hardness is a measure of the resistance of a material to surface indentation or abrasion. There is no absolute scale for hardness. In order to express hardness quantitatively, each type of test has its own scale, which defines hardness. Indentation hardness obtained through static methods is measured by Brinell, Rockwell, Vickers and Knoop tests. Hardness without indentation is measured by a dynamic method, known as the Scleroscope test.