Drilling carbon- and glass-fiber composites, as well as graphite carbon, thermosetting plastics, green ceramics and green carbide, generates dust that poses a health hazard to workers. Vacuuming it through a hood assembly placed over the drill is a possible solution, but it is difficult to correctly position the hood and avoid interfering with the tool while effectively removing the particles, according to Randy Prafke, operations manager at Lach Diamond Inc.
The situation becomes more problematic as the drill diameter increases. “Those bigger drills produce so much dust that a standard vacuum system can’t handle it,” he said, adding that the dust pours across the workpiece. “When you get into this kind of material, you don’t want that dust flying around all over the place.”
To effectively suction and remove the dust particles, the toolmaker’s German parent company, Jakob Lach GmbH & Co. KG, developed a PCD-tipped drill with an internal extraction system through the center of the tool body. Because part manufacturers generally dry-machine these types of workpiece materials, coolant doesn’t need to be delivered through the drill, Prafke noted. “It’s basically the reverse of supplying coolant.”
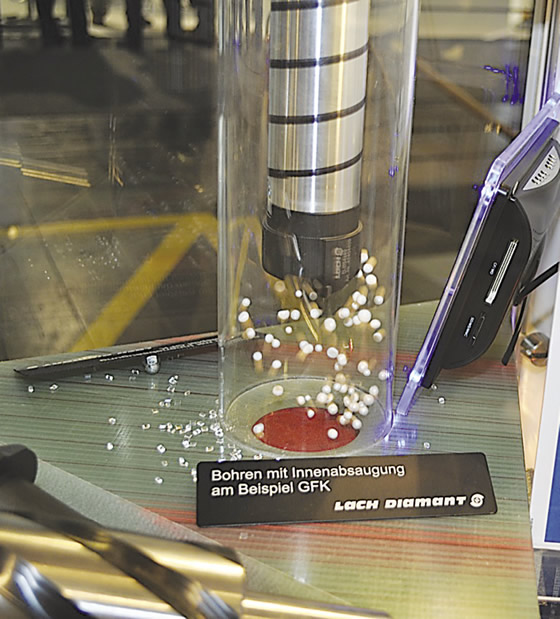
Lach Diamond’s PCD-tipped drill with an internal extraction system through the center of the tool body is demonstrated at EMO.
He explained that Lach engineers specials based on an end user’s application requirements, which can vary significantly depending on the workpiece material and part configuration and requirements. Even different carbon-fiber composites can require unique tool designs based on the direction the material is drilled and its structural characteristics, such as the fiber-weave pattern. “About 99 percent of what we do are special applications,” Prafke said.
The abrasiveness of the composites often dictates the use of PCD drills instead of carbide ones, he added. “Go to a PCD drill and you go from 50 finished holes to 4,500 finished holes.”
Users of the internal-extraction PCD drills require custom-designed machine tools to apply the tools, and an existing machine can be modified to run the drills, Prafke noted.
For additional information about Lach Diamond Inc., Grand Rapids, Mich., call (616) 698-0101 or visit www.lach-diamant.de. CTE
Related Glossary Terms
- ceramics
ceramics
Cutting tool materials based on aluminum oxide and silicon nitride. Ceramic tools can withstand higher cutting speeds than cemented carbide tools when machining hardened steels, cast irons and high-temperature alloys.
- composites
composites
Materials composed of different elements, with one element normally embedded in another, held together by a compatible binder.
- coolant
coolant
Fluid that reduces temperature buildup at the tool/workpiece interface during machining. Normally takes the form of a liquid such as soluble or chemical mixtures (semisynthetic, synthetic) but can be pressurized air or other gas. Because of water’s ability to absorb great quantities of heat, it is widely used as a coolant and vehicle for various cutting compounds, with the water-to-compound ratio varying with the machining task. See cutting fluid; semisynthetic cutting fluid; soluble-oil cutting fluid; synthetic cutting fluid.
- polycrystalline diamond ( PCD)
polycrystalline diamond ( PCD)
Cutting tool material consisting of natural or synthetic diamond crystals bonded together under high pressure at elevated temperatures. PCD is available as a tip brazed to a carbide insert carrier. Used for machining nonferrous alloys and nonmetallic materials at high cutting speeds.