Mold and die makers have long incorporated lasers into their arsenal of fabrication and repair tools; today, new advancements in laser technology have expanded the realm of possibilities.
While traditional machining methods are still used to remove material from the core cavity, lasers can create complex features in molds, fashion intricate mold coolant systems, repair worn molds and even provide routine mold maintenance. The benefits include fine surface finishes, high accuracy and cost and time savings for ablative and additive laser technologies.
Cavity Search
One of the broadest applications of lasers in mold and die making is in patterning the mold cavity, according to Greg Hyatt, senior vice president and chief technical officer at machine builder DMG Mori USA, Hoffman Estates, Ill. While traditional patterning methods, such as chemical erosion or mechanical machining, can achieve simple, repetitive patterns, lasers offer unmatched flexibility, he said.
“The accuracy and speed could be matched using conventional machines for simple repeating patterns, but there is a range of intricacy for which there’s no other technical solution. The laser is really the only way to produce more involved or irregular patterns,” Hyatt said.
In addition to ablating intricate patterns on the mold surface, laser beam sources, such as the redEnergy line of pulsed fiber lasers from Southampton U.K.-based SPI Lasers, can be used to perform deep engraving at depths up to 0.030 ".
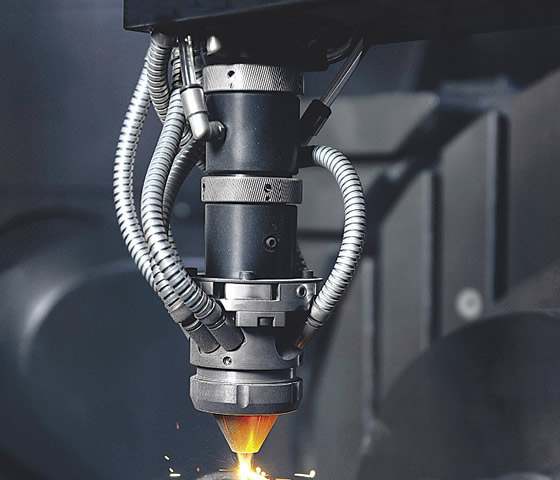
Courtesy of DMG Mori USA
With the Lasertec 65 additive manufacturing machine, DMG Mori incorporates laser deposition welding and 5-axis milling into a hybrid machine.
“Molds are typically made from hardened steels, which are difficult to machine by any means, and certainly lasers are no exception,” said Dr. Ken Dzurko, general manager of SPI Lasers LLC, Santa Clara, Calif. “What you need depends on whether you want to machine the entire mold to a fine surface finish using the laser, or if you are using the laser to imprint a rough pattern and then clean it up using wet chemistry.” The same laser would be utilized in either process, he continued, but the software to direct the laser for fine finishing would need to be considerably more powerful, which is where the cost differential comes into play.
A “brute-force” deep-engraving laser system costs from $30,000 to $60,000, Dzurko said, while a workstation with high-resolution capability can cost well over $100,000—with the bulk of the price difference being the operating software. “To render a 3D object with high spatial resolution and low residual surface roughness takes a lot of programming power.”
Like other lasers, SPI’s machines are controlled using three parameters: pulse duration, frequency and optical power. The lasers can produce pulses from 3 to 500 ns, which can vary in frequency from 1 kHz to 1 MHz, and the operator maintains analog control over the rate of power, Dzurko explained. “With those three knobs to turn, you essentially have an artist’s palette in terms of what you can achieve with that laser,” he said.
Hybrid Vigor
In addition to removing material to create patterns and textures, lasers can be used for additive processes that build mold features. DMG Mori, in conjunction with its subsidiary Sauer GmbH, Pfronten, Germany, has developed a machine that performs both processes: The Lasertec 65 combines laser deposition and 5-axis milling (see photo above).
In the laser deposition process, powdered metal is sprayed into the beam of a high-powered diode laser, with the powder spray focused by a surrounding stream of argon gas, according to Friedemann Lell, sales manager for Sauer. “The powder is directly melted in the laser and deposited to build up complete mold components.”
The machine uses pure metal powder (no additives or binding agents) with grain sizes from 30µm to 100µm, which reduces the cost compared to sintering applications requiring finer powders or additives. The laser deposition process is fairly well established for applying coatings on cutting and hole-punching tools, he explained, but has not previously been utilized to build mold components.
The all-in-one workstation allows mold components to be completed quickly by cutting down on changeover, he said. When the process requires laser deposition, the machine spindle automatically picks up the spray nozzle in an HSK toolholder; when milling needs to be performed, the same machine spindle picks up the milling tool. In this way, the downtime resulting from switching between machines is eliminated. Turning and grinding options can also be added, further increasing the versatility of the multitask machine.
“If there are complex internal coolant channels that would be difficult or impossible to drill, we can manufacture those by deposition,” Hyatt said, “and if those channels require machining before they’re closed, we can do that easily because the turning or milling or grinding is happening in the same machine as the deposition.”
According to the company, the Lasertec 65 has several advantages over powder-bed laser sintering, in which a powder bed in the form of the part is laid down and a laser then sinters that bed into a solid metal part or feature.
The machine’s main advantage is workpiece size. While the area of a typical powder bed is from 200mm to 300mm (8 " to 12 ")—roughly the size of a microwave oven—the 28.9 "×25.6 "×22 " (734.06mm × 650.24 mm × 558.8mm) envelope of the additive laser allows for much larger molds and mold inserts to be manufactured.
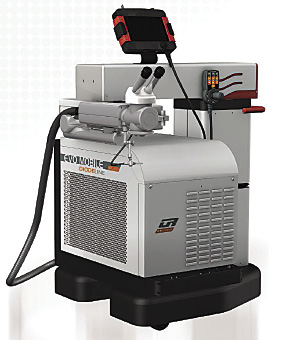
Courtesy of O.R. Lasertechnology
O.R. Lasertechnology’s EVO mobile laser welding station allows for precise repair of mold components.
The other primary advantage is production speed. “Powder beds are designed to achieve a high level of initial accuracy to minimize post-production machining,” Hyatt explained. “But because of the nature of our machine, we don’t have that concern. We focus on productivity and achieve final part accuracy by milling after deposition. As a result, our deposition rates are 10 to 40 times faster than a powder bed, capable of depositing material at a rate of 0.9kg per hour per kilowatt of laser power.” The laser power is adjustable, he explained, allowing for fine control over the deposition process.
While the machine isn’t commercially available—a working prototype was shown at DMG’s open house in Pfronten in February—the company has already received many inquiries, according to Lell. “We have introduced a lot of new technology, but have never had this kind of response, and from different types of customers—from prototypers to additive manufacturing job shops to the aerospace industry to mold and die makers,” he said. “We don’t know how to handle all the inquiries and we don’t even have a machine to sell at this point.” The Lasertec 65 will be introduced to the North American market at IMTS 2014 in September.
A similar machine, the Lumex Avance-25, is distributed by MC Machinery Systems Inc., Wood Dale, Ill. The hybrid laser sintering and milling machine, from Matsuura Machinery Corp., Fukui City, Japan, allows for one-machine, one-process manufacturing of complex molds and parts.
Precision and Power
While 3D laser deposition is a newer addition to the moldmaking toolbox, ablation is still the standard application for lasers when it comes to finishing cavities. Many types of lasers can be used to impart textures, but Raydiance Inc., Petaluma, Calif., offers what it says are complete machining solutions involving ultrashort-pulse lasers.
“Usually when folks turn to [femtosecond lasers], they’ve tried other tools, maybe even other lasers, but can’t reach the dimensional precision they need,” said Michael Mielke, chief scientist for Raydiance. “We deal with part-to-part consistency on the order of 1µm.”
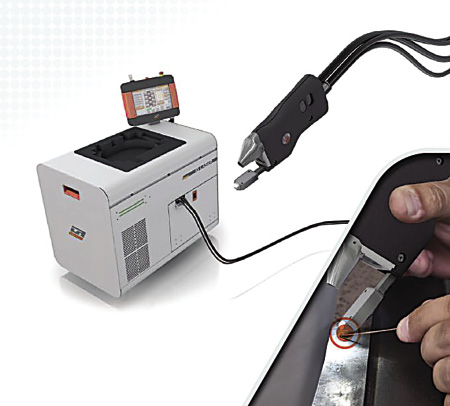
Courtesy of O.R. Lasertechnology
The iQ hand-held welder allows the user to make repairs on mold inserts without removing them from the fixture.
Raydiance recommends femtosecond lasers—which produce the shortest pulse of any laser—for moldmaking work. According to Mielke, the accuracy of fs lasers has led to shops using them to replace other machining options—such as drills, mills, EDMs and conventional CO2 and Nd:YAG lasers—for finishing work, as well as other applications typically reserved for traditional machining.
“If you’re drilling a hole or milling a surface feature in a mold or die, you often have very precise tolerances and surface quality requirements,” Mielke said. “Femtosecond lasers can routinely do submicron-level surface finishes and can maintain flatness on the order of 1µm or less. In comparison [to other types of tooling], sure, a femtosecond laser is going to be more expensive initially, but shops can see a full ROI within months, not years.” Mielke added that moldmakers report reduced material waste and less post-processing when using fs lasers.
Repair Shop
Lasers can also clean and repair molds. Mold cleaning has typically been performed via conventional machining and chemical baths, and repair has been done via manual welding. Part of SPI’s “artist’s palette” of fine control over pulse duration, frequency and power allows the operator to selectively ablate, and thus clean, residue from the molding process.
“Pulse durations of about 200 to 500 ns are very effective for rapid ablation of hard materials,” SPI’s Dzurko explained, “but if you were to squeeze that pulse duration down to around 10 ns, what you would find is that you have a smaller amount of energy in the pulse that can be applied at a much higher frequency and tuned to effectively nibble away at the softer material while not affecting the harder material underneath.”
And when the mold itself eventually wears, Dieburg, Germany-based O.R. Lasertechnologie GmbH offers an advanced repair solution. (O.R.’s U.S. operation, O.R. Lasertechnology, is located in Elk Grove Village, Ill.)
Laser welding—the practice of using a preprogrammed laser system to melt deposition wire directly into the weld—all but eliminates operator error and provides superior weld quality resulting from a simpler operation than conventional welding, according to the company. “With lasers, you can weld very specific areas, put down exactly the amount of material exactly where you want it, making the post-work cleanup very quick and efficient, compared to conventional welding,” said Sales Manager Michael Barsanti. “The deposition wire could be anywhere from 0.004 " to 0.040 " [in diameter], so if there are tiny areas that flash on your molded parts or wear marks that require a very small weld to bring the part back to spec, laser welding is the answer. There’s no oxidization, no porosity, no arc or stick or melt pool to control. The operator just needs to understand the geometry of the workpiece and hold the wire steady, and the machine will give you a uniform weld every time.”

Courtesy of Raydiance
Raydiance lasers utilize pulses in the femtosecond range to ablate material and create finely detailed textures in the mold cavity.
Laser welding is not new, but O.R. says its line of diode lasers has refined the process. The Nd:YAG lasers typically used for laser welding introduced in the 1980s were water-cooled and utilized multiple moving parts, as well as lamps and other consumables that had to be monitored and replaced. O.R.’s Diode-brand diode lasers, by contrast, are air-cooled, have no moving parts and use single-phase power, eliminating the need for a bulky transformer. In addition, the laser welding process can be automated.
Operating O.R.’s Diode lasers does not require extensive training or craftsmanship, according to Barsanti. “The machine is positioned on an X-Y arm and is run by a joystick, and, once positioned by the operator, the entire process is mechanized. That means a novice laser welder can come in after just a few days of training and do a professional repair job on a mold, something that was never possible before.”
O.R. said its iQ hand-held tool takes advantage of laser welding being extremely precise and using only a small amount of material. The tool allows a user to repair an injection mold without removing the inserts, potentially saving days of work, according to Barsanti.
Bright Future
Advances in laser technology have engendered new manufacturing techniques, according to Raydiance’s Mielke. He points to the automotive, aerospace, consumer electronics and medical device industries moving toward adopting new laser technology as it becomes available.
As power levels and pulse-control capabilities increase and the technology becomes more affordable, Dzurko predicts that it will put the technology within reach of a larger share of the market—and result in more high-quality products being made using molds.
Mielke believes increased awareness of the possibilities will also contribute to widespread adoption. “My favorite thing to see with our customers is the realization of ‘Oh my gosh, I can design something completely outside the scope of the limitations I had before,’ that expansion of what’s possible,” he said. “Everyone is always looking for a better way to make stuff.” CTE
Contributors
DMG Mori USA
(847) 593-5400
www.dmgmori-usa.com
O.R. Lasertechnology
(847) 593-5711
www.or-laser.com
Raydiance Inc.
(707) 559-2100
www.raydiance.com
Sauer GmbH
+49 8363-890
tr.dmgmori.com/en,plant,sauer
SPI Lasers LLC
(408) 454-1170
www.spilasers.com
Related Glossary Terms
- coolant
coolant
Fluid that reduces temperature buildup at the tool/workpiece interface during machining. Normally takes the form of a liquid such as soluble or chemical mixtures (semisynthetic, synthetic) but can be pressurized air or other gas. Because of water’s ability to absorb great quantities of heat, it is widely used as a coolant and vehicle for various cutting compounds, with the water-to-compound ratio varying with the machining task. See cutting fluid; semisynthetic cutting fluid; soluble-oil cutting fluid; synthetic cutting fluid.
- fixture
fixture
Device, often made in-house, that holds a specific workpiece. See jig; modular fixturing.
- flash
flash
Thin web or film of metal on a casting that occurs at die partings and around air vents and movable cores. This excess metal is due to necessary working and operating clearances in a die. Flash also is the excess material squeezed out of the cavity as a compression mold closes or as pressure is applied to the cavity.
- gang cutting ( milling)
gang cutting ( milling)
Machining with several cutters mounted on a single arbor, generally for simultaneous cutting.
- grinding
grinding
Machining operation in which material is removed from the workpiece by a powered abrasive wheel, stone, belt, paste, sheet, compound, slurry, etc. Takes various forms: surface grinding (creates flat and/or squared surfaces); cylindrical grinding (for external cylindrical and tapered shapes, fillets, undercuts, etc.); centerless grinding; chamfering; thread and form grinding; tool and cutter grinding; offhand grinding; lapping and polishing (grinding with extremely fine grits to create ultrasmooth surfaces); honing; and disc grinding.
- lapping compound( powder)
lapping compound( powder)
Light, abrasive material used for finishing a surface.
- milling
milling
Machining operation in which metal or other material is removed by applying power to a rotating cutter. In vertical milling, the cutting tool is mounted vertically on the spindle. In horizontal milling, the cutting tool is mounted horizontally, either directly on the spindle or on an arbor. Horizontal milling is further broken down into conventional milling, where the cutter rotates opposite the direction of feed, or “up” into the workpiece; and climb milling, where the cutter rotates in the direction of feed, or “down” into the workpiece. Milling operations include plane or surface milling, endmilling, facemilling, angle milling, form milling and profiling.
- milling machine ( mill)
milling machine ( mill)
Runs endmills and arbor-mounted milling cutters. Features include a head with a spindle that drives the cutters; a column, knee and table that provide motion in the three Cartesian axes; and a base that supports the components and houses the cutting-fluid pump and reservoir. The work is mounted on the table and fed into the rotating cutter or endmill to accomplish the milling steps; vertical milling machines also feed endmills into the work by means of a spindle-mounted quill. Models range from small manual machines to big bed-type and duplex mills. All take one of three basic forms: vertical, horizontal or convertible horizontal/vertical. Vertical machines may be knee-type (the table is mounted on a knee that can be elevated) or bed-type (the table is securely supported and only moves horizontally). In general, horizontal machines are bigger and more powerful, while vertical machines are lighter but more versatile and easier to set up and operate.
- sintering
sintering
Bonding of adjacent surfaces in a mass of particles by molecular or atomic attraction on heating at high temperatures below the melting temperature of any constituent in the material. Sintering strengthens and increases the density of a powder mass and recrystallizes powder metals.
- turning
turning
Workpiece is held in a chuck, mounted on a face plate or secured between centers and rotated while a cutting tool, normally a single-point tool, is fed into it along its periphery or across its end or face. Takes the form of straight turning (cutting along the periphery of the workpiece); taper turning (creating a taper); step turning (turning different-size diameters on the same work); chamfering (beveling an edge or shoulder); facing (cutting on an end); turning threads (usually external but can be internal); roughing (high-volume metal removal); and finishing (final light cuts). Performed on lathes, turning centers, chucking machines, automatic screw machines and similar machines.