Applying high-pressure coolant when Swiss-style turning is effective at clearing chips to prevent them from welding to the workpiece or wrapping around the cutting tool. However, steering the coolant as close as possible to the cutting edge is tricky.
To remedy the situation while not pigeonholing the end user into one brand of cutting tool, Genevieve Swiss Industries Inc. offers the Multidec-Lube through-coolant tool clamp from Utilis AG, Müllheim, Switzerland. The patented system incorporates a coolant or oil delivery passage in the tool clamp to ensure a repeatable jet flow within a few millimeters of the tool/workpiece interface even after multiple tool changes, setups or teardowns, according to GenSwiss. It replaces the original gang slide tool clamps that come with a machine, allowing use of conventional, non-through-coolant, square-shank toolholders as if they were through-coolant holders because the coolant travels through the Multidec-Lube clamp.
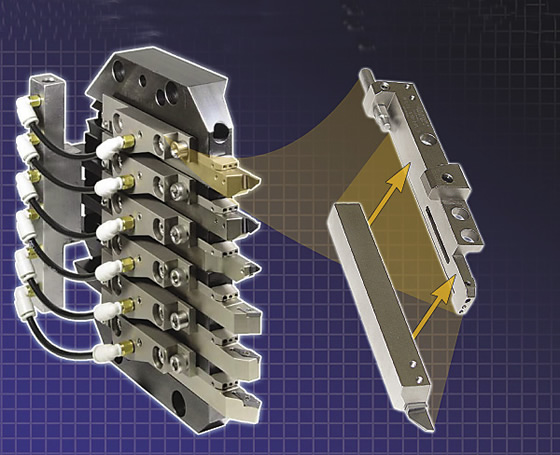
With GenSwiss’ Multidec-Lube tool clamp system, a square-shank, Swiss-style toolholder installs against the Multidec clamping wedge.
“Most Swiss turning centers have four to eight turning stations, and you can equip each one of those with one of these clamps and permanently run high-pressure lines,” said Scott Laprade, marketing manager for GenSwiss, noting the system didn’t leak when tested at 2,000 psi. “I don’t know anyone running anything higher.”
He added that an adjustable stop provides quick-change capability by enabling users to position a tool in the exact same location after an insert change.
Compared to manually bending and positioning coolant nozzles, the tool-clamp system drastically reduces setup time, according to Laprade. At the company’s machine shop, it took at least a couple hours to accurately position multiple nozzles on a manifold setup for a Swiss-style machine, he said. “With these it takes a few minutes.”
Although suitable for virtually all turning applications, on rare occasions, such as profiling a unique radius with a special tool, a fine-tuned manually adjustable nozzle might work better on one station, Laprade acknowledged. But the Multidec-Lube clamps would still be more effective than coolant nozzles for the remaining stations, he added.
Because of the large number of Citizen machines in use that employ ½ " square-shank stick tools for turning, such as the A20, L20, K16 and M16 models, GenSwiss began by offering tool clamp systems for them, and plans to introduce ones for other makes and models throughout the year.
For more information about Genevieve Swiss Industries Inc., Westfield, Mass., call (888) 244-1404 or visit www.genswiss.com.
Related Glossary Terms
- centers
centers
Cone-shaped pins that support a workpiece by one or two ends during machining. The centers fit into holes drilled in the workpiece ends. Centers that turn with the workpiece are called “live” centers; those that do not are called “dead” centers.
- coolant
coolant
Fluid that reduces temperature buildup at the tool/workpiece interface during machining. Normally takes the form of a liquid such as soluble or chemical mixtures (semisynthetic, synthetic) but can be pressurized air or other gas. Because of water’s ability to absorb great quantities of heat, it is widely used as a coolant and vehicle for various cutting compounds, with the water-to-compound ratio varying with the machining task. See cutting fluid; semisynthetic cutting fluid; soluble-oil cutting fluid; synthetic cutting fluid.
- profiling
profiling
Machining vertical edges of workpieces having irregular contours; normally performed with an endmill in a vertical spindle on a milling machine or with a profiler, following a pattern. See mill, milling machine.
- toolholder
toolholder
Secures a cutting tool during a machining operation. Basic types include block, cartridge, chuck, collet, fixed, modular, quick-change and rotating.
- turning
turning
Workpiece is held in a chuck, mounted on a face plate or secured between centers and rotated while a cutting tool, normally a single-point tool, is fed into it along its periphery or across its end or face. Takes the form of straight turning (cutting along the periphery of the workpiece); taper turning (creating a taper); step turning (turning different-size diameters on the same work); chamfering (beveling an edge or shoulder); facing (cutting on an end); turning threads (usually external but can be internal); roughing (high-volume metal removal); and finishing (final light cuts). Performed on lathes, turning centers, chucking machines, automatic screw machines and similar machines.