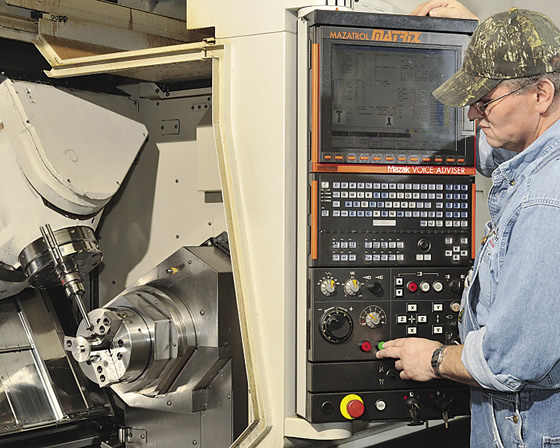
All images courtesy Ingersoll Cutting Tools
An operator at Allied Specialty Precision cutting a gear from 17-4 PH bar stock using an indexable tool.
By tradition, gear makers tend to be skeptical of new ideas. Most still generate gear teeth with single-point, HSS shapers, rack cutters or hobs, believing that indexable-insert tools cost too much, can’t meet American Gear Manufacturers Association standards or are “not proven” enough.
More progressive gear makers tell a different story. By applying indexable-insert tools, many have gained substantial competitive and cost advantages. They are routinely tripling material-removal rates and tool life with no tradeoff in accuracy or surface finish. They have also gotten off the tool regrinding carousel, a bottleneck that often delays deliveries. Regrinding tools typically requires trafficking five expensive cutters through 5-week regrinding cycles just to keep a single process operating.
In many cases, these progressive thinkers have also dispensed with special-purpose hobbing machines and machine-to-machine part transfers. Some are even completing the entire gear—teeth, keyways and hubs—with “one-and-done” machining processes on general-purpose CNC machining centers.
Opening New Doors
The potential to improve gear machining stems largely from advances in indexable-insert carbide tools that enable them to repeatably hold much closer tolerances than previously possible. Indexable mills, including form tools, significantly perform better than and outlast HSS ones. They also routinely hold 0.0005 " (0.0127mm) repeatability to datum, axially and radially. That’s more than good enough for the vast majority of gear machining applications. Moreover, many indexable tools or inserts can be replaced in the spindle, so chipmaking can resume in minutes with no touching off.
One case demonstrates many of these advantages. On an 8 AGMA 66.5 " shaft gear, a mining equipment manufacturer reduced tooth-generation cycle time from 34 hours to 8.5 hours by switching from HSS shaping to indexable-insert hobbing. The new process uses a 1.25DP Ingersoll single-start indexable hob on a Liebherr LC 2500 hobbing machine. The change also eliminated a separate rough sawing operation and mid-cut stoppages to replace tools. Cutting edges last for two complete parts and deliver an 80-rms surface finish to the roots of the shaft gear.
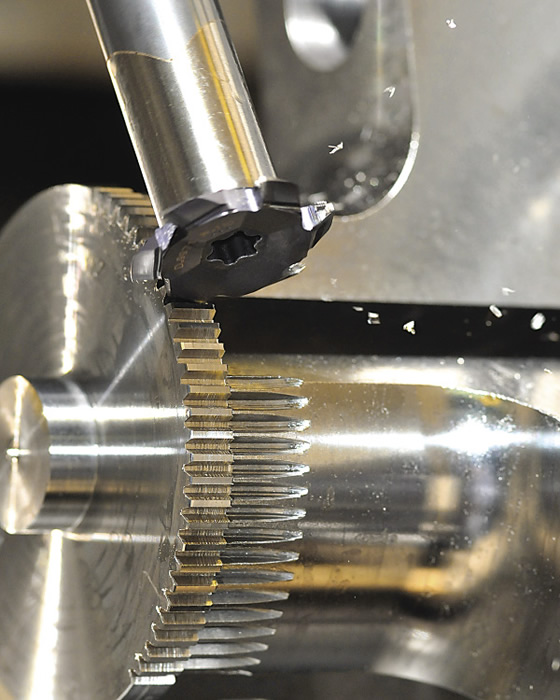
A modified standard Chip-Surfer slotting tool from Ingersoll forms teeth in two passes at Allied Specialty Precision, reducing cycle time by 20 minutes.
The process is essentially climb milling. Parameters for roughing are 110 mm/min. (4.33 ipm) surface speed, 0.90mm (0.035 ") axial feed per table revolution and a 42.45mm (1.67 ") DOC. For finishing, the respective parameters are 140 mm/min. (5.51 ipm), 0.300mm (0.012 ") and 5mm (0.197 "). The application reflects the trend toward using advanced indexable hobs for higher AGMA-class work.
The dramatic reduction in cycle time stems from two key differences between the hobbing and shaping tools. First, hobbing, a rotating-tool process with multiple cutting edges, keeps a cutting edge engaged in the cut much longer than a reciprocal-motion shaping process. Second, the indexable single-start hob allows higher speeds and feeds, leading to increased mrr and shorter cycle times.
One and Done
Another company, Allied Specialty Precision Inc., is milling gear teeth rather than hobbing or gashing them. As a result, the Mishawaka, Ind.-based company cuts gear teeth in half the previous time and completes all other operations in the same setup. “Now it’s a pure one- and-done operation, even including the gear teeth,” said Todd Stoddard, manufacturing engineer at Allied.
Cutting the teeth was always the longest part of these jobs, so, as order volume rose, Stoddard decided to streamline that operation. Andy Thornburg, field engineer for Ingersoll Cutting Tool Co., Rockford, Ill., suggested approaching the gear tooth forms as slots. Accordingly, the gear teeth are now milled with a form-matched Ingersoll replaceable-tip Chip-Surfer T-slotting tool rather than a HSS gear gasher. Cutting speed increased by a factor of 10 and tool life tripled.
The process change also reduced tooling cost per part from $20 to $2.56. Each Chip-Surfer replaceable tip costs about $125—approximately the same cost as one regrind of a $500 gear gasher. Fewer spares are needed as well, because the turnaround time for new tips is a few days, compared to up to 5 weeks for regrinding the gasher.
As the Worm Turns
Form milling also improves process economics for making the worms used in gear drives. Besides speeding up chipmaking compared to traditional hobbing, form-matched slotting mills running on 4-axis CNC machines also eliminate the need for limited-use hobbing machines and expensive hobbing tools.
Shops using this method report, on average, a 300 percent improvement in cycle time and tool life on a variety of worms compared to using form-matched worm hobs.
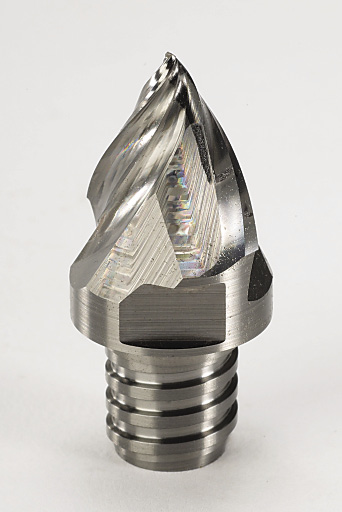
Ingersoll’s modified standard Chip-Surfer carbide slotting tool.
“At some time in a worm machining process, the part is put on a mill anyway, at least to cut a keyway,” said Ingersoll Tool Engineer Jeremy Bradley, who developed the worm-slotting method. “It’s a matter of adding an operation to a milling process instead of transferring the part among machines and stocking six to eight spare tools to support the operation.”
In one tooth-forming application, form milling with a modified standard Chip-Surfer completed a worm in a single pass, reducing cycle time from 14 to 4 minutes. Mounted on an alloy steel shank, the replaceable-tip cutting tool produced 60 to 80 pieces compared to 200 pieces between resharpenings for an HSS hob, but cost about one third as much as regrinding the $400 HSS hob, the average cost of which was $50. Traditional worm fabrication involves three separate operations, requiring two transfers among machines. First the bar stock is turned on one machine to generate the hub and worm ODs. Then the parts are moved to a mill to create nontooth-related features, such as flats and keyways. Finally, hobbing is performed on a dedicated machine.
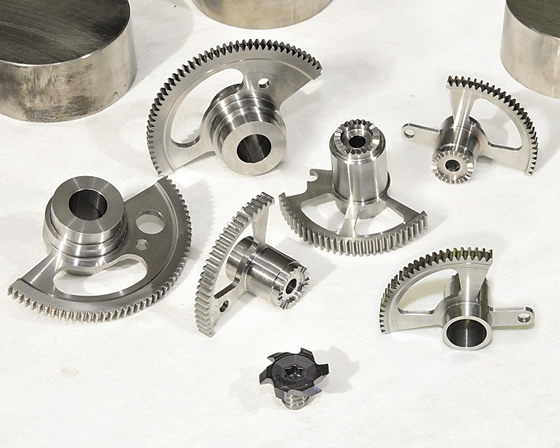
A selection of typical worms for worm-gear drives.
In the new process, the form-matched slotter, running in a 4-axis program, generates the form as a milling operation, so the whole part can be completed on a single machine.
Other applications for replaceable-tip indexable tools include slotting and cavity milling and as replacements for comparable solid-carbide or HSS tools. Compared with a HSS tool, a replaceable-tip tool cuts faster and lasts longer. Compared with solid-carbide endmills, a replaceable-tip tool requires up to 90 percent less carbide. When mounted on an alloy-steel shank, it also eliminates the risk of tool failures due to vibration or excessive lateral forces. CTE
Contact Details
Related Glossary Terms
- centers
centers
Cone-shaped pins that support a workpiece by one or two ends during machining. The centers fit into holes drilled in the workpiece ends. Centers that turn with the workpiece are called “live” centers; those that do not are called “dead” centers.
- climb milling ( down milling)
climb milling ( down milling)
Rotation of a milling tool in the same direction as the feed at the point of contact. Chips are cut to maximum thickness at the initial engagement of the cutter’s teeth with the workpiece and decrease in thickness at the end of engagement. See conventional milling.
- computer numerical control ( CNC)
computer numerical control ( CNC)
Microprocessor-based controller dedicated to a machine tool that permits the creation or modification of parts. Programmed numerical control activates the machine’s servos and spindle drives and controls the various machining operations. See DNC, direct numerical control; NC, numerical control.
- cutting speed
cutting speed
Tangential velocity on the surface of the tool or workpiece at the cutting interface. The formula for cutting speed (sfm) is tool diameter 5 0.26 5 spindle speed (rpm). The formula for feed per tooth (fpt) is table feed (ipm)/number of flutes/spindle speed (rpm). The formula for spindle speed (rpm) is cutting speed (sfm) 5 3.82/tool diameter. The formula for table feed (ipm) is feed per tooth (ftp) 5 number of tool flutes 5 spindle speed (rpm).
- feed
feed
Rate of change of position of the tool as a whole, relative to the workpiece while cutting.
- gang cutting ( milling)
gang cutting ( milling)
Machining with several cutters mounted on a single arbor, generally for simultaneous cutting.
- high-speed steels ( HSS)
high-speed steels ( HSS)
Available in two major types: tungsten high-speed steels (designated by letter T having tungsten as the principal alloying element) and molybdenum high-speed steels (designated by letter M having molybdenum as the principal alloying element). The type T high-speed steels containing cobalt have higher wear resistance and greater red (hot) hardness, withstanding cutting temperature up to 1,100º F (590º C). The type T steels are used to fabricate metalcutting tools (milling cutters, drills, reamers and taps), woodworking tools, various types of punches and dies, ball and roller bearings. The type M steels are used for cutting tools and various types of dies.
- milling
milling
Machining operation in which metal or other material is removed by applying power to a rotating cutter. In vertical milling, the cutting tool is mounted vertically on the spindle. In horizontal milling, the cutting tool is mounted horizontally, either directly on the spindle or on an arbor. Horizontal milling is further broken down into conventional milling, where the cutter rotates opposite the direction of feed, or “up” into the workpiece; and climb milling, where the cutter rotates in the direction of feed, or “down” into the workpiece. Milling operations include plane or surface milling, endmilling, facemilling, angle milling, form milling and profiling.
- milling machine ( mill)
milling machine ( mill)
Runs endmills and arbor-mounted milling cutters. Features include a head with a spindle that drives the cutters; a column, knee and table that provide motion in the three Cartesian axes; and a base that supports the components and houses the cutting-fluid pump and reservoir. The work is mounted on the table and fed into the rotating cutter or endmill to accomplish the milling steps; vertical milling machines also feed endmills into the work by means of a spindle-mounted quill. Models range from small manual machines to big bed-type and duplex mills. All take one of three basic forms: vertical, horizontal or convertible horizontal/vertical. Vertical machines may be knee-type (the table is mounted on a knee that can be elevated) or bed-type (the table is securely supported and only moves horizontally). In general, horizontal machines are bigger and more powerful, while vertical machines are lighter but more versatile and easier to set up and operate.
- sawing
sawing
Machining operation in which a powered machine, usually equipped with a blade having milled or ground teeth, is used to part material (cutoff) or give it a new shape (contour bandsawing, band machining). Four basic types of sawing operations are: hacksawing (power or manual operation in which the blade moves back and forth through the work, cutting on one of the strokes); cold or circular sawing (a rotating, circular, toothed blade parts the material much as a workshop table saw or radial-arm saw cuts wood); bandsawing (a flexible, toothed blade rides on wheels under tension and is guided through the work); and abrasive sawing (abrasive points attached to a fiber or metal backing part stock, could be considered a grinding operation).
- shank
shank
Main body of a tool; the portion of a drill or similar end-held tool that fits into a collet, chuck or similar mounting device.
- shaping
shaping
Using a shaper primarily to produce flat surfaces in horizontal, vertical or angular planes. It can also include the machining of curved surfaces, helixes, serrations and special work involving odd and irregular shapes. Often used for prototype or short-run manufacturing to eliminate the need for expensive special tooling or processes.
- slotting
slotting
Machining, normally milling, that creates slots, grooves and similar recesses in workpieces, including T-slots and dovetails.