A PCBN cutting-edge tip brazed onto a carbide insert body provides an effective cutting tool for machining a host of materials, such as cast iron and hardened steel. However, making the indexable-insert tool requires either EDMing or laser machining precision-ground PCBN blanks to produce the tips, grinding carbide blanks to create pockets for the tips or buying preground, pre-pocketed blanks and brazing the tips into the pockets. This requires expensive brazing equipment, a furnace and skilled operators.
Thinking that there had to be a more efficient way, IDS Cutting Tools developed a patent-pending method for pressing PCBN tips to size in a mold and then thermally shrink fitting them in a P/M steel insert body, similar to the way a shrink-fit holder grasps a tool, noted Jackson Briggs, product manager for IDS, which has served the oil and gas industry with various diamond products for more than 25 years. The company then sells semifinished PCBN inserts to toolmakers and part manufacturers to finish via grinding. The inserts can then be PVD- or CVD-coated or left uncoated and protected from rusting by applying oil on the inserts.
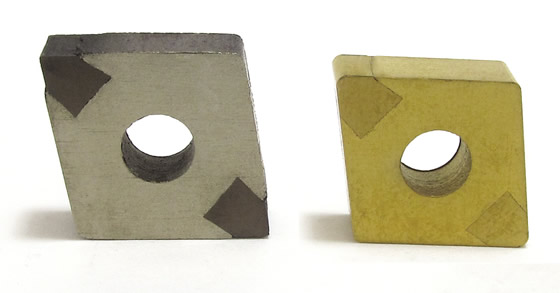
IDS Cutting Tools offers semifinished PCBN inserts in which PCBN tips are thermally shrunk fit into a P/M steel body that customers finish via grinding and coating for sale to end users or for in-house applications.
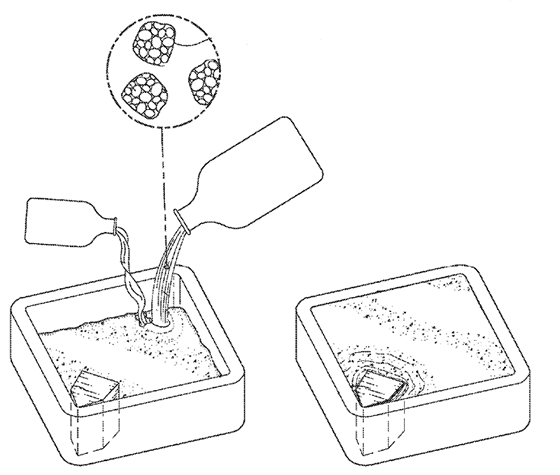
When making semifinished PCBN inserts, IDS Cutting Tools pours P/M steel into a mold containing at least one PCBN tip until the mold is filled.
“When looking at the price on a per-edge basis, we’re looking to save toolmakers about 50 percent of their manufacturing costs and eliminate the investment that brazing requires,” Briggs said. He added that a large auto parts manufacturer, for example, found IDS’ inserts performed as well as conventional brazed inserts while providing comparable tool life.
IDS grinds the tops and bottoms of tips to improve toughness and bend strength after they are pressed, explained Dr. Steve Webb, product development engineer for IDS. The sides of all tips, however, are left unground to improve the ability of the PCBN tip and the P/M steel to adhere to each other. “Efficiency is machining only what needs to be machined and putting hard material only where it needs to be,” he said.
“We bury tips in the steel powder, which is green compacted, then stick that in the furnace and fire it,” Webb added. “The steel binder burns out, the steel thermally contracts around all the tips and hardens and then we pull the hot pieces out.”
The low-carbon steel hardens to 70 HRB, while the PCBN is unaffected.
IDS offers three grades: LF with 50 percent CBN content and a grain size of 2µm, primarily for roughing and finishing hardened steel; HC with 85 percent CBN and 8µm grains, for roughing and semifinishing cast iron; and HF with 90 percent CBN and 2µm grains, for finishing cast iron.
IDS offers a standard range of tip and insert shapes and can produce anything from the ordinary to the exotic because the entire insert, or part, manufacturing process is based around molds, Briggs said. “As long as the part will sinter, we can produce it.” Theoretically, that includes making a ninja star with 16 cutting edges for both machining and combat purposes.
Although the company initially is targeting the PCBN insert market, IDS is developing prototypes of semifinished PCD inserts and the process is suitable for any tip material with adequate heat tolerance and bend and tensile strength, Webb pointed out. The material list also includes most ceramics, cermet and carbide. “The product for carbide is maybe 20 years ahead of its time, but this is where the cutting world is going,” he said.
For more information about IDS Cutting Tools, Houston, call (713) 681-5485 or visit www.idscuttingtools.com. CTE
Related Glossary Terms
- ceramics
ceramics
Cutting tool materials based on aluminum oxide and silicon nitride. Ceramic tools can withstand higher cutting speeds than cemented carbide tools when machining hardened steels, cast irons and high-temperature alloys.
- cubic boron nitride ( CBN)
cubic boron nitride ( CBN)
Crystal manufactured from boron nitride under high pressure and temperature. Used to cut hard-to-machine ferrous and nickel-base materials up to 70 HRC. Second hardest material after diamond. See superabrasive tools.
- grinding
grinding
Machining operation in which material is removed from the workpiece by a powered abrasive wheel, stone, belt, paste, sheet, compound, slurry, etc. Takes various forms: surface grinding (creates flat and/or squared surfaces); cylindrical grinding (for external cylindrical and tapered shapes, fillets, undercuts, etc.); centerless grinding; chamfering; thread and form grinding; tool and cutter grinding; offhand grinding; lapping and polishing (grinding with extremely fine grits to create ultrasmooth surfaces); honing; and disc grinding.
- lapping compound( powder)
lapping compound( powder)
Light, abrasive material used for finishing a surface.
- laser machining
laser machining
Intensified, pulsed beams of light generated by lasers—typically carbon dioxide or neodium-doped yttrium aluminum garnet (Nd:YAG)—that drill, weld, engrave, mark, slit and caseharden. Usually under CNC, often at both high cutting rates (100 linear in./sec.) and high power (5kW or more). Lasers also are used in conjunction with in-process quality-control monitoring systems allowing measuring accuracies of 0.00001".
- polycrystalline cubic boron nitride ( PCBN)
polycrystalline cubic boron nitride ( PCBN)
Cutting tool material consisting of polycrystalline cubic boron nitride with a metallic or ceramic binder. PCBN is available either as a tip brazed to a carbide insert carrier or as a solid insert. Primarily used for cutting hardened ferrous alloys.
- polycrystalline diamond ( PCD)
polycrystalline diamond ( PCD)
Cutting tool material consisting of natural or synthetic diamond crystals bonded together under high pressure at elevated temperatures. PCD is available as a tip brazed to a carbide insert carrier. Used for machining nonferrous alloys and nonmetallic materials at high cutting speeds.
- tensile strength
tensile strength
In tensile testing, the ratio of maximum load to original cross-sectional area. Also called ultimate strength. Compare with yield strength.
- tolerance
tolerance
Minimum and maximum amount a workpiece dimension is allowed to vary from a set standard and still be acceptable.