The poor heat conductivity of stainless steel, titanium, cobalt-chrome and nickel-base alloys makes them difficult to machine and causes a cutting tool to become extremely hot when machining them. To prevent that heat from prematurely damaging a tool’s cutting edges when machining these challenging materials, coolant must be applied, according to Mikron Tool SA Agno.
As a result, the Swiss toolmaker developed the CrazyMill Cool solid-carbide endmill with internal cooling channels that are large in relation to the cutting diameter, noted Markus Schnyder, Mikron founder and president. The design provides a high-volume coolant flow rather than a high-pressure stream to remove heat from the cutting zone while clearing chips to prevent recutting them and damaging the tool. The recommended coolant pressure is from 400 to 500 psi (29 to 35 bar).
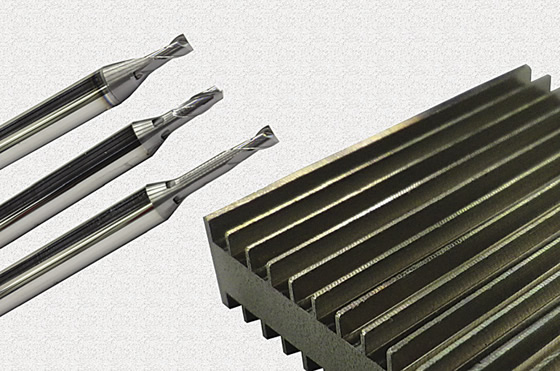
Three versions of CrazyMill Cool through-coolant milling cutters are available for different maximum milling depths from 1.5 to 5 diameters deep.
“We have seen that using more than 1,000 psi makes no sense, because there is no change in the results,” he said, noting the coolant keeps the tool/workpiece interface below 1,112° to 1,292° F (600° to 700° C)—the “green range.”
The tools have three to five channels, depending on the cutter diameter. The diameter range is from 0.3mm to 6mm (0.012 " to 0.236 "). “We think we could start at 0.1mm,” Schnyder said, “but we are not there yet.”
Because the cooling channels are optimally sized to achieve maximum flow, standard coolant filtration of 10µm to 15µm (0.0004 " to 0.0006 ") is suitable, according to Alberto Gotti, who’s in charge of R&D at Mikron.
In addition to the coolant channels, Schnyder emphasized that designers optimized the entire tool—substrate, geometry and coating—to tackle materials with poor heat conductivity. The carbide grains are smaller than 0.5µm (0.00002 ") and are distributed and anchored in a cobalt binder to provide the required combination of hardness and toughness, he noted.
Prior to coating, a pretreatment process polishes the substrate and radiuses the cutting edges. “The radiusing is very soft and gentle for the smaller sizes and more intense for the larger diameters,” Schnyder said. The tools are also available with a 45° protection face, instead of a corner radius, to stabilize the cutting edges.
Gotti indicated that the aluminum-chromium-nitride base coating is modified by other coating elements to provide a low affinity with nickel, chrome and the other alloying elements in challenging workpieces, such as stainless. “It’s like using Teflon on your cooking pan,” he said. “We reduce the risk that material will stick to the cutting edges.”
The coating is polished, which, in combination with the cooling effect, reduces the risk of built-up edge, Gotti added.
When a machine tool spindle with through-coolant capability can rotate at speeds that enable microscale endmills to cut effectively, the CrazyMill Cool is 10 to 20 times more efficient than conventional cutters, according to Schnyder. And with the enhanced chip evacuation, such as when machining deep slots, the toolmaker reports that the tool imparts surface finishes two to three times finer—“the cherry on the cake.”
For more information about Mikron Corp. Monroe, based in Monroe, Conn., call (203) 261-3100 or visit www.mikron.com/tool-us.
Related Glossary Terms
- alloys
alloys
Substances having metallic properties and being composed of two or more chemical elements of which at least one is a metal.
- built-up edge ( BUE)
built-up edge ( BUE)
1. Permanently damaging a metal by heating to cause either incipient melting or intergranular oxidation. 2. In grinding, getting the workpiece hot enough to cause discoloration or to change the microstructure by tempering or hardening.
- coolant
coolant
Fluid that reduces temperature buildup at the tool/workpiece interface during machining. Normally takes the form of a liquid such as soluble or chemical mixtures (semisynthetic, synthetic) but can be pressurized air or other gas. Because of water’s ability to absorb great quantities of heat, it is widely used as a coolant and vehicle for various cutting compounds, with the water-to-compound ratio varying with the machining task. See cutting fluid; semisynthetic cutting fluid; soluble-oil cutting fluid; synthetic cutting fluid.
- endmill
endmill
Milling cutter held by its shank that cuts on its periphery and, if so configured, on its free end. Takes a variety of shapes (single- and double-end, roughing, ballnose and cup-end) and sizes (stub, medium, long and extra-long). Also comes with differing numbers of flutes.
- gang cutting ( milling)
gang cutting ( milling)
Machining with several cutters mounted on a single arbor, generally for simultaneous cutting.
- hardness
hardness
Hardness is a measure of the resistance of a material to surface indentation or abrasion. There is no absolute scale for hardness. In order to express hardness quantitatively, each type of test has its own scale, which defines hardness. Indentation hardness obtained through static methods is measured by Brinell, Rockwell, Vickers and Knoop tests. Hardness without indentation is measured by a dynamic method, known as the Scleroscope test.
- milling
milling
Machining operation in which metal or other material is removed by applying power to a rotating cutter. In vertical milling, the cutting tool is mounted vertically on the spindle. In horizontal milling, the cutting tool is mounted horizontally, either directly on the spindle or on an arbor. Horizontal milling is further broken down into conventional milling, where the cutter rotates opposite the direction of feed, or “up” into the workpiece; and climb milling, where the cutter rotates in the direction of feed, or “down” into the workpiece. Milling operations include plane or surface milling, endmilling, facemilling, angle milling, form milling and profiling.