A shortage of skilled employees is a common problem for virtually all part manufacturers. Finding CNC programmers, machinists, toolmakers and engineers with the skills to be effective can seem impossible. This can make developing and improving machining operations exceptionally difficult.
I was fortunate to have had the opportunity to learn machining and toolmaking in my family’s machine shop under the guidance of a master tool and die maker. I had time to learn and practice my skills, then apply them as a manufacturing engineer when coupled with my higher education.
Unfortunately, few manufacturing engineers have any significant shop time, and the shop time they do have was probably spent learning bad habits and unsafe techniques in an outdated engineering department lab. Some of these young engineers will eventually find themselves thrust into jobs where success requires them to develop and manage machining processes.
Compounding the problem, the machinists and toolmakers who have the ability to teach young engineers are disappearing and being replaced with machine operators who lack the skills to solve complex machining problems or to develop new processes.
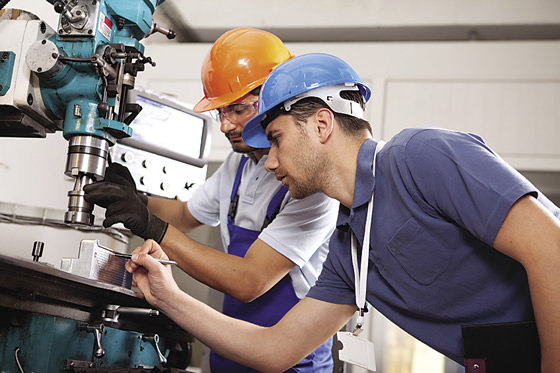
Industry’s response to these conditions has been to turn to machine tool builders and distributors. These companies can provide the skills needed to develop new machining processes and help train engineers and operators.
“Turnkey solution” is the term typically applied to these services, which means different things to different people. Some projects consist of many machines and take many months to prepare, while others consist of one machine making a simple part. Engineers typically associate turnkey services with a new machine purchase, but machine tool distributors often set up and program a part on an existing machine.
Hiring a machine tool builder or distributor to provide a turnkey solution or process design can have significant benefits. Obviously, with a turnkey solution, the vendor provides all the expertise needed to design and build the process. This means a manufacturer can focus its resources on other projects, preventing the dilution of limited resources. Small manufacturers frequently have excellent support and production personnel but lack the advanced skills needed to develop a complex machining operation from scratch. Turnkey solutions can mitigate these situations by providing a complete package.
In addition, turnkey solutions allow one-stop shopping for manufacturers. An effective turnkey solution provides all the fixtures, tools, programming, development and cutting tools needed to complete a project. This reduces the costs associated with supporting the purchase of multiple components.
A turnkey solution also transfers a large portion of risk to the machine tool supplier. New projects can be challenging and the opportunities for failure can be numerous. The vendor, however, is responsible if cutting tools and fixtures do not perform as expected. If the project is specified correctly, the vendor must provide a complete solution that fulfills all of its customer’s quality and cycle-time requirements.
When designing a machining process with numerous fixtures and cutting tools, it is easy to have items that do not interface correctly with each other. When one vendor sources all of the components, it is responsible for ensuring all the components interface correctly.
One rarely recognized benefit of turnkey services is the broad knowledge base possessed by machine tool builders and distributors as a result of their involvement in many different industries and experience with countless machining operations. They are also tapped into the latest technologies and machining techniques.
It is easy for a manufacturer to unknowingly become trapped in a machining process because it is familiar; creativity can be stifled. Turnkey providers bring innovation because they are unencumbered by a customer’s culture or the we-have-always-done-it-this-way mentality.
Of course, there are some drawbacks to turnkey services, and cost is usually the first issue. However, don’t confuse cost with price. The true cost of a failed project can easily be more than the price of a sound solution. As such, value is probably the best term to use when discussing turnkey projects.
Good turnkey solution providers should offer things that would not otherwise be available to a manufacturer. Many times these are intangible items, such as a talented application engineer or expert fixture designer. They might have made the same or similar parts in the past and have a unique, cost-saving method. This brings value to a project.
Some might argue that purchasing a turnkey solution removes the opportunity for an engineer to gain experience. However, a young engineer can learn a lot from a knowledgeable machine tool application engineer.
Turnkey solutions can efficiently and effectively fill the skills gap and leverage the knowledge of a local machine tool distributor. The expense can often easily be justified if the solution adds value and the vendor brings innovation and creativity. CTE
About the Author: Christopher Tate is engineering manager, combustion shop, for Mitsubishi Hitachi Power Systems Americas, Savannah (Ga.) Machinery Works, a global builder of gas and steam turbines. He has 20 years of experience in the metalworking industry and holds a Master of Science and Bachelor of Science from Mississippi State University. Email: [email protected].
Related Glossary Terms
- computer numerical control ( CNC)
computer numerical control ( CNC)
Microprocessor-based controller dedicated to a machine tool that permits the creation or modification of parts. Programmed numerical control activates the machine’s servos and spindle drives and controls the various machining operations. See DNC, direct numerical control; NC, numerical control.
- fixture
fixture
Device, often made in-house, that holds a specific workpiece. See jig; modular fixturing.
- metalworking
metalworking
Any manufacturing process in which metal is processed or machined such that the workpiece is given a new shape. Broadly defined, the term includes processes such as design and layout, heat-treating, material handling and inspection.