Job shops generally tackle numerous low-volume part runs and often feel that automated manufacturing systems are not suitable for their operations. Steelville (Mo.) Manufacturing Co. begs to differ.
The family-owned and -operated company handled about 10,500 part numbers last year, predominantly defense-related aerospace components, and used two flexible manufacturing systems to produce a vast majority of them, noted John Bell, vice president – engineering for SMC. “We’ve done as many as 13,800 part numbers in a year,” he said, adding that the shop produces an average of 30 pieces of each part number annually.
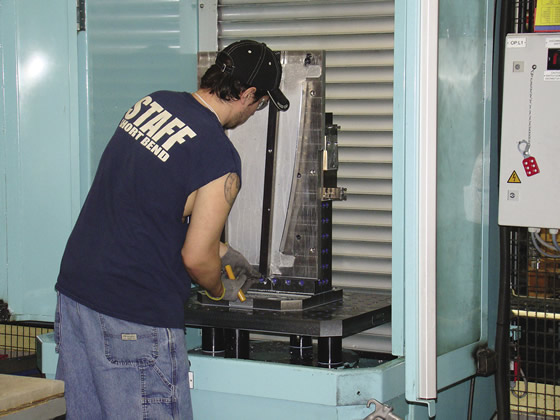
A worker loads parts into a tombstone for machining in the Fastems cell at SMC. All images courtesy A. Richter.
About 15 years ago, SMC installed a Makino A55E 4-axis, 400mm (15.75 ") horizontal machining center as a stand-alone machine and added two Makino A51 HMCs about 8 years ago. The shop then combined the three machines to create an MMC (Makino Machining Complex) automated pallet-delivery work cell. “We can put two more machines on it if we get enough business to fill it up,” Bell said.
Realizing the shop was going down the right automation path while understanding it needed to perform simultaneous 5-axis machining, in 2009 SMC added a Fastems pallet-delivery work cell that marries two Okuma Millac 800HV 5-axis, 800mm vertical machining centers and two Okuma MA600HB 4-axis, 630mm (24.8 ") VMCs. The Fastems/Okuma FMS also includes two tombstone-changing stations and two material-handling stations, one between two machines and the other at the end of the cell.
When installed, the FMS was Fastems’ longest in North America at 167 ' (50.9m), according to the company, and still remains one of the longest. When installing the MMC, Bell said SMC planned on adding a second cell at a later date as well, so the company added about 17,000 sq. ft. (5,182 sq. m) to its facility to accommodate both. The addition brought the building to 50,000 sq. ft. (15,240 sq. m).
As with the Makino cell, the second cell has space for up to two more machines. Bell noted adding machines to the Fastems cell is basically a plug-and-play procedure that doesn’t involve adding to payroll. “We can simply add two machines,” he said. “It’s nice to know that I don’t have to bring in more employees [to operate them]. It’s just a matter of capital expenditure.”
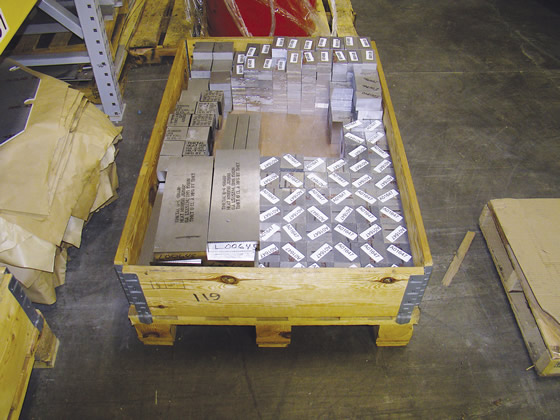
A typical crate for the Fastems FMS is loaded with a variety of workpieces for placing into tombstones.
Although both cells function in a similar manner while processing information a bit differently, the MMC communicates only with Makino machines while the Fastems FMS works with CNC machines from various builders. On the Fastems system at SMC, the shop can add any modern machine tool, according to Michael Bell, director of operations for Fastems LLC, West Chester, Ohio, who’s not related to John. “We have integrated 72 different machine tool manufacturers’ equipment into our systems to date,” he said. “Pallet size is irrelevant as is machine tool type (VMC or HMC).”
Bell added that lathes and mills can even be positioned in a progressive line, if needed. In addition to scheduling jobs, the cells use a track-based, pick-and-place robot to gather workpiece materials and tombstones from multiple-level racks and return them.
Bell emphasized that any mix of parts can justify an FMS, but a shop must have work it can schedule for the system to function properly. This sometimes requires a shift in a company’s mindset. “So many machinists have never really had to do scheduling,” he said. That differs from the typical scenario in which a machinist receives a job from his foreman, completes it, then receives another job.
Hard and Soft Cells
SMC machines a host of workpiece materials, including titanium, Inconel, stainless steel, aluminum, phenolic, plastics and some composite materials. In the Fastems system, Bell said two machines—a 4-axis machine for roughing and a 5-axis one for finishing—are more or less dedicated to cut relatively soft metals and two are dedicated to the more challenging ones.
The arrangement functions fairly well, but Bell conceded it is not ideal, because it limits SMC’s ability to run any part on any machine. “If the whole cell ran one or the other, we could greatly increase our efficiencies,” he said.
Nonetheless, Bell noted the two 5-axis machines in the cell achieve at least 80 percent spindle utilization and frequently hit 90 percent, while the 4-axis machines have a spindle utilization from 40 to 60 percent. Achieving higher spindle utilization is easier to achieve when the need to write part programs, which is done offline, is not as demanding.
“Last year, we did a little over 2,000 first articles,” Bell said. “We will likely do about 1,500 to 1,800 first articles this year, but we still are getting 100 to 150 new parts each month.”
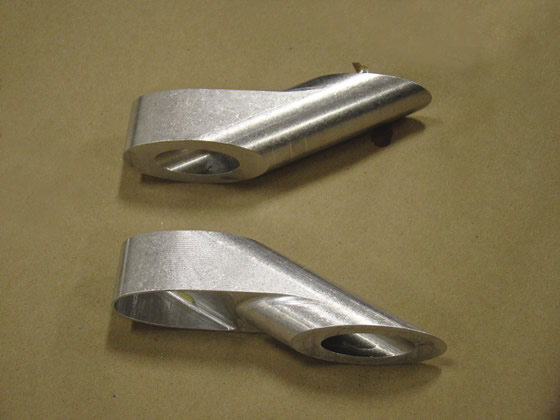
An example of the type of parts SMC produces for the aerospace industry that require 5-axis machining.
The shop runs three shifts 5 days a week, with the day shift being the most manned. It uses that shift to produce first articles and other critical components. During the first shift, two people run each cell, whereas only one person runs each cell during the second shift and one person runs both cells during the midnight shift.
Prior to adding the Fastems system, SMC employed slightly fewer than 50 people, Bell said. Some of those workers were concerned that more automation would jeopardize their jobs. “Their automatic response was that ‘you’re not going to need us,’ but we’ve done nothing but hire more people since putting it in,” he said, adding that SMC employs 138 workers. Those additional hires are not necessarily tending machine tools; the automation created positions in shipping and receiving, inspection, quality and programming.
“The cells have actually decreased our need for skilled machinists,” Bell said. However, he added that the cells make the production process more difficult because SMC needs programmers with significantly higher skill levels to keep everything moving, especially with the volume it has. “We’ve had as many as seven programmers operating at one time, and we could always use two or three more.” The shop didn’t have 5-axis programming capability when it installed the Fastems system.
Tracking Down Talent
Finding the required talent to grow can be a challenge for any manufacturer, and particularly for one located in a town with some 1,600 residents and 90 miles from the nearest city. “Being out here in the middle of the country, we don’t have a deep bench of talent to draw from,” Bell said.
Therefore, SMC provides in-house training and taps into online resources, such as the National Tooling & Machining Association’s NTMA-U program and Tooling University LLC’s Tooling U-SME curricula. Bell noted the company is also looking at the possibility of creating an apprenticeship program to replenish skills as its workforce ages.
“My brothers and I are all in our early to mid-50s,” he said. “We were all young when we started, and we still have 25 of our first employees with us, but they’re just a little younger than we are. So 15 years from now we are going to need a lot of new workers.”
In addition to continual training, Steelville Manufacturing also promotes continuous improvement in connection with its lean initiative. As part of that effort, the company seeks to overcome issues created by outsourcing parts for processing, such as painting, heat treating, anodizing and conversion coating. “Besides programming, outside processing has been our biggest bottleneck,” Bell said.
He noted customers want 8- to 12-week lead times for their parts, but outside processing alone can consume 6 to 12 weeks. For example, parts may require an initial outsourced process before returning to SMC for assembly and then are shipped again after assembly for an additional process, such as top coating. “That takes 12 weeks,” Bell said. “We’re just at the mercy of our suppliers.”
In addition, SMC can’t control the quality of its suppliers, such as when they mask the wrong side of a part or chemically etch too much material for holes with tolerances as tight as 0.0005 " (0.0127mm). “They should remove no more than 0.0001 " or 0.0002 " in the process,” Bell said, “but it always seems like when our parts go into the tank, the workers take a smoke break and, when they come back, our holes are 0.0006 " or 0.0007 " bigger.”
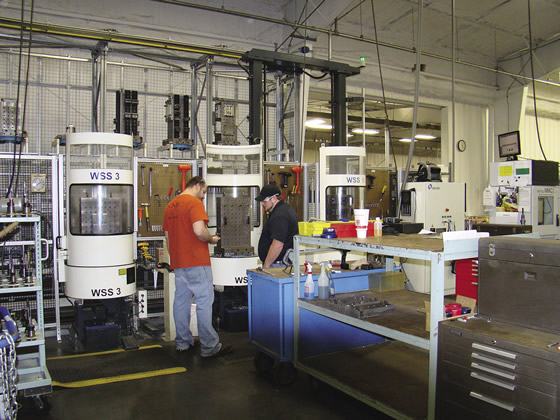
SMC’s MMC automated pallet-delivery work cell has three work stations.
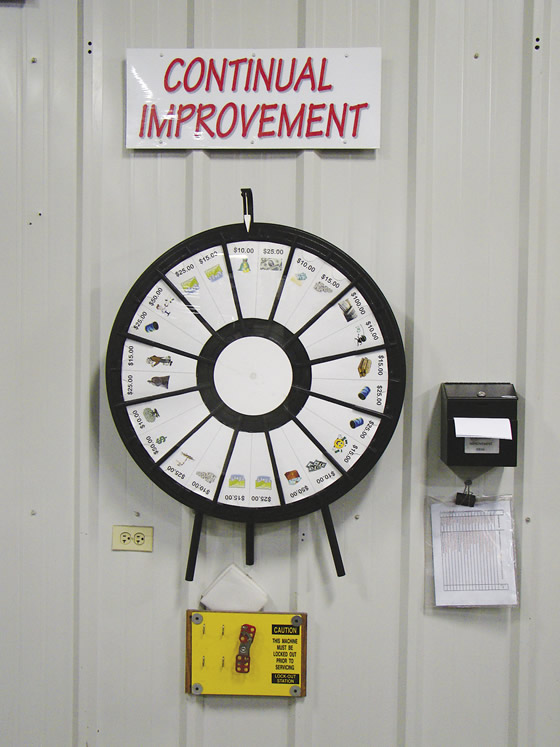
Each month, workers at SMC submit ideas for continual improvement and the worker with the best idea, as determined by company managers, gets to spin the continual-improvement wheel and win a cash prize.
Bell added that SMC might be able to salvage parts with secondary, corrective operations or an outside processor might redo a batch of parts—or not. “One time they scrapped $8,000 worth of parts; I don’t even think they said they were sorry.”
To bring the work in-house and avoid lead-time and part-quality problems, SMC built a new 16,000-sq.-ft. (4,877-sq.-m) facility to house equipment for painting, heat treating and chemical processing. The facility is expected to begin operating in the fall. Not only will doing those processes internally solve the quality problems, it will also ensure that SMC can meet its delivery times if a supplier is unable to accommodate SMC because the supplier no longer has the capacity, Bell added. “We’re trying to get ahead of that curve.”
After installing the equipment and obtaining the required Nadcap certifications, such as for heat treating and chemically processing, Bell said the shop plans to start heat treating parts in 6 months and perform chemical processing by the end of 2016. (Nadcap is an aerospace-industry-managed conformity assessment.)
With about 25 acres of land to expand on out of the 400 acres the company owns, SMC has room to grow. Bell indicated that the company is considering adding another building, possibly to house a flexible manufacturing work cell dedicated to machining hard metals and one dedicated to machining soft metals.
The growth would certainly generate more jobs at SMC while making its customers happier by meeting their lead time requirements. “I can show them that these systems make my machines more productive,” Bell said.
For more information about Steelville Manufacturing Co., call (573) 775-2977 or visit www.steelvillemfg.com. CTE
About the Author: Alan Richter is editor of CTE. Contact him at (847) 714-0175 or [email protected].
All in the family
Steelville Manufacturing Co. was established in 1959 and the Bell family began acquiring shares in the 1960s. The father, Paul, a lawyer by trade, traded his legal work with one of the company’s original investors for shares over time. He acquired SMC outright in 1979 and distributed shares to his sons, Dennis, Bob and John, as they got older.
The three boys got acclimated to working in the shop by doing chores, such as sweeping floors and cleaning bathrooms, before advancing to deburring parts and running jobs that were already set up. “It was all manual equipment back then,” said John Bell, vice president - engineering.
Not being a machinist, the father hired a shop manager before gaining full ownership. The shop struggled to make a profit during that time, John noted. After the eldest son, Dennis, SMC president, began managing the company in 1979, profitability improved. Since then, John added, SMC has seen positive growth except for 3 years when it posted small losses. In the last 25 years, SMC hasn’t had a drop in sales, John noted, adding that SMC experienced double-digit sales growth during the Great Recession.
John added that SMC maintains its growth without a sales force or even a salesman, relying instead on word-of-mouth and the company’s reputation.
In 1993, SMC became a preferred supplier to McDonnell Douglas Corp. and maintained that relationship after Boeing Co. purchased its long-time rival in 1996. John added SMC plans to remain privately held rather than cashing in its chips by selling to an equity fund, which Boeing prefers because the aerospace OEM finds that part costs tend to rise and quality diminishes after an equity fund assumes ownership of a parts manufacturer. This occurs because the equity fund typically pays a premium to acquire a company and removes the highest-paid employees—the ones who play critical roles in enhancing productivity and ensuring high-quality parts.
Although SMC has almost exclusively served the defense side of the aerospace industry, John pointed out that the shop is slowly but steadily doing more commercial aerospace work, which requires part volumes up to 2,500 or more instead of 30. The dollar value for one commercial customer with 65 part numbers, for example, can replace one military program with 3,000 part numbers.
—A. Richter
Related Glossary Terms
- centers
centers
Cone-shaped pins that support a workpiece by one or two ends during machining. The centers fit into holes drilled in the workpiece ends. Centers that turn with the workpiece are called “live” centers; those that do not are called “dead” centers.
- computer numerical control ( CNC)
computer numerical control ( CNC)
Microprocessor-based controller dedicated to a machine tool that permits the creation or modification of parts. Programmed numerical control activates the machine’s servos and spindle drives and controls the various machining operations. See DNC, direct numerical control; NC, numerical control.
- flexible manufacturing system ( FMS)
flexible manufacturing system ( FMS)
Automated manufacturing system designed to machine a variety of similar parts. System is designed to minimize production changeover time. Computers link machine tools with the workhandling system and peripherals. Also associated with machine tools grouped in cells for efficient production. See cell manufacturing.
- land
land
Part of the tool body that remains after the flutes are cut.
- machining center
machining center
CNC machine tool capable of drilling, reaming, tapping, milling and boring. Normally comes with an automatic toolchanger. See automatic toolchanger.
- pick-and-place robot
pick-and-place robot
Simple robot or piece of hard automation that is capable of the simple actions of picking an object from a fixed point and placing the object at another fixed point.