According to hockey legend Wayne Gretzky, a great player skates to where the puck will be rather than where it is.
Similarly, world-class manufacturers expand their production space for anticipated demand rather than attempting to catch up with current needs. This effort to always be ahead of the times was on display at Horn Technology Days, which took place June 17-19 and was hosted by Hartmetall-Werkzeugfabrik Paul Horn GmbH at its headquarters in Tübingen, Germany.
The cutting tool and carbide manufacturer reported that it is doubling its capacity by adding 12,000 sq. m (39,370 sq. ft.) of production space, which Horn plans to occupy by the end of the year. The company currently manufactures more than 20,000 different types of standard tools and has supplied 120,000-plus specials to date. Horn says it processes about 96,000 production orders annually and produces around 9 million inserts in batches that average 90 pieces.
The toolmaker isn’t only adding production space. Horn stated that it hired 100 new employees last year and plans to create more jobs annually in anticipation of the new building’s completion and the extra capacity it will provide. The figure is even more compelling given that one person operates up to seven auto-loading grinding machines. The company employs more than 850 people in Tübingen and nearby Gomaringen, up to 60 of whom are apprentices. Outside of Germany, 400 employees work at various branches, such as Horn USA Inc. in Franklin, Tenn., which is also undergoing upgrades.
Horn’s machinist apprenticeship program lasts 3 years and receives about 80 applications a year for approximately 15 openings. The men and women who make the cut must have a solid knowledge of physics, chemistry and mathematics, be responsible and able to work independently and as a team, communicate effectively, have a basic understanding of English and be physically fit. The practical training for the apprenticeship program includes measuring, marking, manual and mechanical machining, forming, assembly and disassembly, CNC technology and commissioning equipment and systems.
As part of its systematic growth, Horn invested nearly $34 million a couple years ago to build a plant for its Horn Hartstoffe GmbH subsidiary in Tübingen. At the facility, with 5,000 sq. m (16,404 sq. ft.) of production area, the company produces carbide inserts and blanks via metal injection molding and hydrostatic and axial pressing.
According to the company, the injection molding process required about 3 years to develop, and the plant has a toolroom for producing its own molds. Injection molding reduces the amount of grinding needed to produce an insert by about 30 percent and can produce geometries that are not cost-efficient or possible to grind, such as complex chipbreaker geometries and inserts with cutting edges on the top and bottom. For the molding process, Horn must modify the carbide powder with additives that act as a binder, which are then removed in a vacuum using reduction gases during the presintering stage.
With the event’s slogan of “Innovative Machining Technologies” on display, it became apparent that Horn isn’t just selling cutting tools—it is selling technology while skating toward the place tool development is headed. CTE
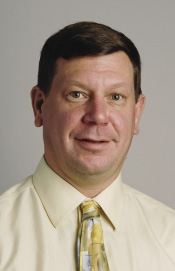
Alan Richter, Editor, [email protected]
Related Glossary Terms
- chipbreaker
chipbreaker
Groove or other tool geometry that breaks chips into small fragments as they come off the workpiece. Designed to prevent chips from becoming so long that they are difficult to control, catch in turning parts and cause safety problems.
- computer numerical control ( CNC)
computer numerical control ( CNC)
Microprocessor-based controller dedicated to a machine tool that permits the creation or modification of parts. Programmed numerical control activates the machine’s servos and spindle drives and controls the various machining operations. See DNC, direct numerical control; NC, numerical control.
- grinding
grinding
Machining operation in which material is removed from the workpiece by a powered abrasive wheel, stone, belt, paste, sheet, compound, slurry, etc. Takes various forms: surface grinding (creates flat and/or squared surfaces); cylindrical grinding (for external cylindrical and tapered shapes, fillets, undercuts, etc.); centerless grinding; chamfering; thread and form grinding; tool and cutter grinding; offhand grinding; lapping and polishing (grinding with extremely fine grits to create ultrasmooth surfaces); honing; and disc grinding.
- lapping compound( powder)
lapping compound( powder)
Light, abrasive material used for finishing a surface.