An interview with Michael Nahum, Micro Encoder Inc.
Michael Nahum, Ph.D., is president of Micro Encoder Inc., Kirkland, Wash., a wholly owned R&D subsidiary of Mitutoyo Corp., Kawasaki, Japan. MEI develops new technologies and software for products, such as small hand-held measurement instruments like calipers and micrometers, and capital equipment like machine vision systems and coordinate measuring machines. The company employs a combined 85 people at its 30,000-sq.-ft. (2,787-sq.-m) facility in Kirkland and 4,000-sq.-ft. (372-sq.-m) facility near Los Angeles. These facilities include state-of-the-art temperature- and vibration-controlled laboratories, electromagnetic and optical test and measurement equipment, more than 15 machine vision systems and five CMMs. Nahum spoke about the company’s areas of focus, how part miniaturization influences inspection, new metrology devices and techniques that can help part manufacturers meet their needs, and what still needs to be accomplished in order for metrology to improve.
Cutting Tool Engineering: What are the metrology areas that MEI focuses on?
Michael Nahum: We are always looking for new technologies for small hand tools to make them more useful by improving measurement capabilities. Another big focus is research for machine vision systems, where we develop algorithms, software and hardware that provide customers higher throughput, more ease of use, 3D measurement capability and better accuracy. We also develop part program-generation software for CMMs. Finally, we develop technologies for noncontact sensors, such as chromatic confocal systems, and white light interferometers.
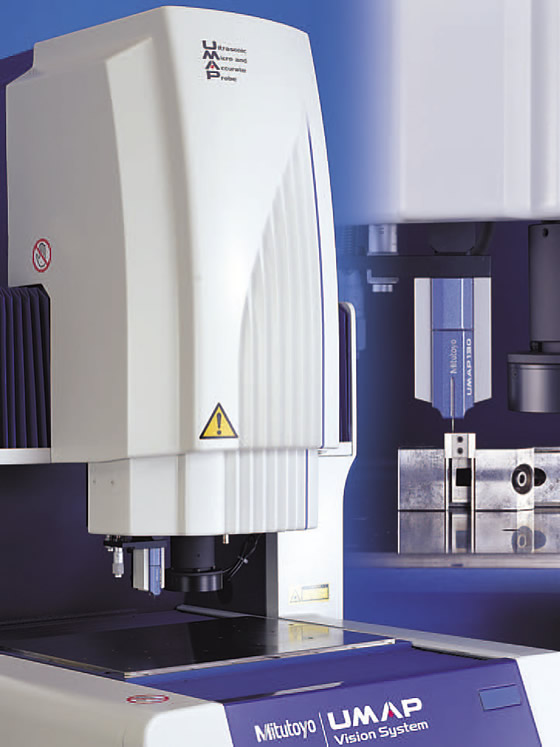
Styli as small as 15µm on the UMAP vision system from Mitutoyo enable microscopic-form touch measurement. Image courtesy Mitutoyo.
CTE: Why is metrology becoming more necessary?
Nahum: Precision parts inevitably have to be fabricated to some required tolerance level, and tolerances are growing tighter, especially as parts shrink in size. Better metrology equipment will enable a part to have a slightly looser fabrication tolerance requirement, for example 0.0005 " instead of 0.0003 ", because less of the cumulative tolerance is consumed by the metrology equipment. This saves our customers money and makes their job easier.
CTE: What’s required to incorporate new metrology technologies into existing measurement methods?
Nahum: First, there must be a key purpose for introducing a new technology, such as better performance or another significant advantage for the customer. Second, customers depend on the results from our products. Therefore, measurement results from the new technology must closely correspond to existing measurement methods. We do not want to make a change that can disrupt a working process. We expend a huge effort checking new technologies to make sure they perform as well as or better than existing technologies under various conditions, including temperature and humidity levels. Third, we want to minimize reengineering to accommodate new technology, which places additional requirements on size, weight and power consumption. All in all, it is a challenging job to develop new technologies for existing methods.
CTE: How does part miniaturization influence inspection?
Nahum: Smaller features are often denser, which generally means tighter tolerances. When we develop new products, we want higher spatial and axial resolution, as well as a convenient working range. In addition, many small parts have difficult-to-inspect characteristics. For example, if a shiny part has lots of edges, you might get multiple reflections with an optical system, or it might have very steep edges, so it’s tough to measure. It can be difficult to know if you’re even measuring the feature of interest. If you want to measure the surface roughness of an integrated-circuit bonding pad, are you actually measuring the bonding pad or a neighboring feature? Contact metrology can become a much bigger problem. Your typical CMM probe doesn’t work, because you need a much lower force and smaller contact area. Depending on the material, tiny features can’t endure much force, so noncontact and low-force measurements become important. Aside from probe manufacturing issues, motion control increasingly becomes a challenge. When features are located microns apart, you must be able to move and detect position at a smaller scale if you need to rely on positioning for measurement. Volume sensing technology, such as white light interferometry and points from focus systems, help solve this problem, at least within a field of view.
CTE: What devices or techniques are you finding that manufacturers need?
Nahum: 2D microscale is not so new—microscopes and high-magnification vision inspection have been meeting these needs for years, although their performance continues to improve. For instance, high-accuracy optical systems from Mitutoyo allow interchangeable lenses to achieve very high magnifications. We are finding, however, that customers need 3D measurement capability more and more. In some of our systems, we use conventional vision in combination with some type of noncontact 3D sensor, such as a chromatic confocal sensor, a point sensor with a small spot size that you scan over the part. We use the vision mainly for alignment to know where we are starting to acquire the scan and where we are ending the scan, to register and align the noncontact sensor. In addition, we have contact probes for accurate 3-D measurements of microparts. The Mitutoyo UMAP probe has a stylus diameter as small as 15µm (0.0006 "). Effectively, it’s a nanoCMM.
CTE: What efforts has the metrology industry taken for micro-scale applications?
Nahum: These include improved traceability chains, improved CMM accuracy via calibration models, volume-compensation methods and the use of technology roadmaps to give metrology companies a heads-up on future needs. New gaging technology has also seen tremendous growth, especially in the noncontact arena. We see many profiler systems that can perform detailed 3D analysis of shapes and features. The ability to put these all in one system remains a challenge, mainly because these multisensor systems are relatively expensive.
CTE: What still needs to be accomplished for metrology to improve?
Nahum: Throughput, accuracy, resolution, ease of use all must continue to improve. Difficult parts are still a challenge for optical systems, such as parts with shiny surfaces, steep angles and high aspect ratios. In addition, tighter feedback loops require metrology to move more inline, in-machine. That requires miniaturization of the metrology equipment itself, as well as increased robustness and a lower cost. The difficulty of making contact with features without breaking probes or damaging parts will increase and result in more noncontact sensing technologies. Regarding ease of use, many sensors require customers to set up different operating parameters, so they have to bring the sensor to just the right distance from the workpiece and get it in the right range. We’re trying to remove the human effect from the equation as much as possible. CTE

Michael Nahum, president of Micro Encoder Inc.
Related Glossary Terms
- 3-D
3-D
Way of displaying real-world objects in a natural way by showing depth, height and width. This system uses the X, Y and Z axes.
- calibration
calibration
Checking measuring instruments and devices against a master set to ensure that, over time, they have remained dimensionally stable and nominally accurate.
- metrology
metrology
Science of measurement; the principles on which precision machining, quality control and inspection are based. See precision machining, measurement.
- tolerance
tolerance
Minimum and maximum amount a workpiece dimension is allowed to vary from a set standard and still be acceptable.
- vision system
vision system
System in which information is extracted from visual sensors to allow machines to react to changes in the manufacturing process.