Having fun is a familiar theme at Fallbrook Technologies. The Cedar Park, Texas-based company’s NuVinci continuously variable planetary transmission hub makes riding a bike, for example, a pure pleasure by seamlessly changing the bike’s drive ratio in contrast to the clunky shifting felt with derailleur gears.
Fun is also found in Fallbrook’s prototype shop, which began offering its low-volume machining services to external customers in June as part of the Fallbrook Technologies Engineering Services (FTES). “Doing something new brings new challenges and keeps people engaged in the work,” said Mark House, engineering manager of the prototype shop. “Challenges are fun for us.”
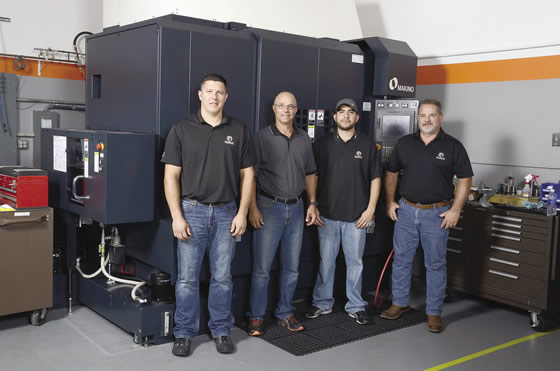
The prototype shop workers are (left to right): Jason Schafer, Keith Knippa, Kris Gonzales and Mark House. Image courtesy Fallbrook Technologies.
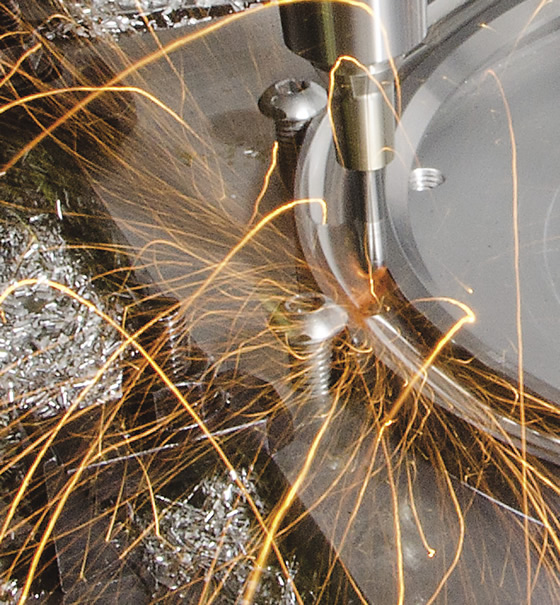
A prototype part is machined on Fallbrook’s Makino V56i Pro 5 vertical machining center. Image courtesy Makino.
He added that so far the shop hasn’t come across a challenge that it couldn’t overcome. Those difficult jobs include milling materials harder than 68 HRC, which some job shops turn down because they don’t have adequate hard-milling capability, or machining internal and external involute splines with radii as small as 0.010 " (0.254mm) in hardened steel.
House expects to see outside jobs progressively increase over the next few years. Historically, Fallbrook’s internal projects have required shop priorities to frequently change. Offering prototypes with quick turnaround times to new customers necessitates assurance that commercial work doesn’t interfere with the shop’s ability to complete prototypes for licensees. “There are concerns about that so we’ll break into it kind of slow,” House added.
Strictly PrototypesHouse emphasized that Fallbrook’s machine shop is different from a standard job shop because it makes prototypes for licensees’ applications and doesn’t perform any production work. “The parts are similar but almost every transmission that we design for our customers is unique, so it truly is prototyping,” he said.
In addition to machining parts, such as rings and stators, House noted the shop, which employs three machinists plus himself, is heavily involved in building test stands for testing new transmission designs. If an issue arises with one of those stands, such as a shaft that has too much runout, the replacement component is typically needed in less than a week. “Otherwise, we have engineers standing around waiting for something,” he said. “We have testing that needs to take place, so we have to move fairly quick.”
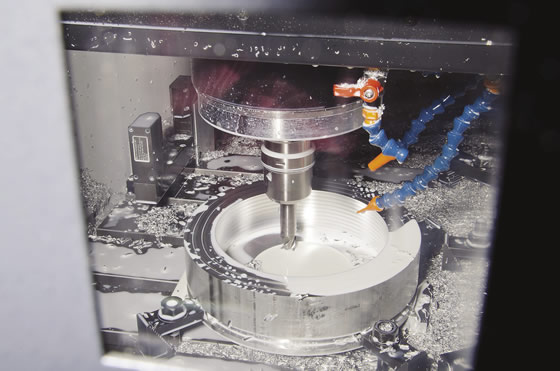
Fallbrook is able to impart surface finishes as fine as 0.1µm Ra on its Makino V56i. Image courtesy Makino.
That need for speed also comes into play when creating high-priority prototype parts, including ones for external customers. “I can take three parts and hand one to each of those guys,” House said, “and they work on it start to finish, and in a day or two we have completed parts.” He compared that to a conventional job shop that might take a week to quote a part and consume 12 weeks or more to deliver it after determining how to schedule the part into its system. “We don’t function that way.”
This is possible, according to House, because each shop worker can program, saw, operate a CNC mill and a CNC lathe, perform heat treatment, grind, deburr, weld and do other fabrication tasks, and interact with the engineering department to get their questions answered and the metrology lab to get their parts measured. “They have the ability to carry a part through the shop on their own from start to finish,” he said. “The versatility of shop employees is really what shines.”
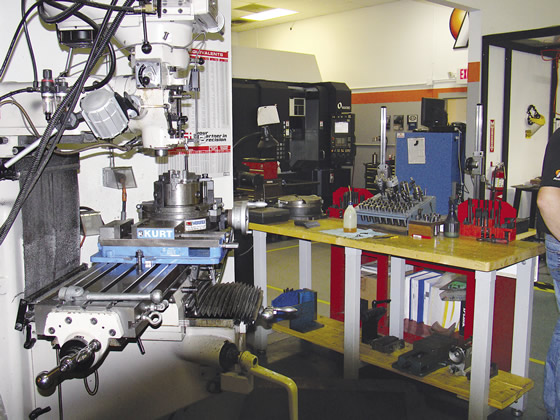
The prototype shop includes a mix of general-purpose and high-performance machines. Image courtesy A. Richter.
Adding to the fun, the machinists sometimes need to be creative in how they produce a part. House explained that for the first decade of Fallbrook’s 11-year history, the shop exclusively used “general-purpose equipment” to make prototypes before acquiring a high-performance Makino V56i Pro 5 vertical machining center (see sidebar on page 53). “They accept the fact that they’re going to have to build whatever is needed and build it with what they have, and they are comfortable doing that, for the most part,” he said with a smile, adding that the shop still uses those cost-effective, general-purpose machines for 95 percent of its work. “We’ve created a different culture, which came from our need for quickly producing quality parts.”
In addition to being able to effectively and creatively use a range of manufacturing equipment, House pointed out the need to be a good communicator to fit into the shop’s culture. “When sharing skill sets, every individual becomes stronger than he is by himself,” he said. “That’s how we grow the shop. It takes time; you’re talking years, potentially.”
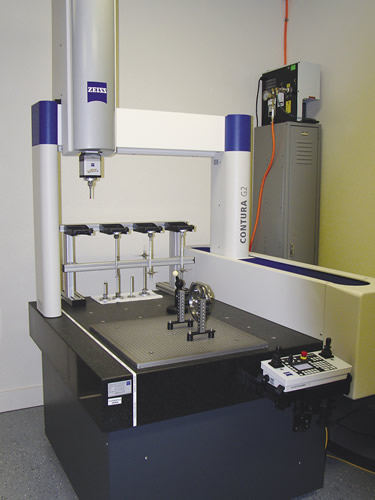
A part is positioned for measurement on a Zeiss Contura G2 coordinate measuring machine in Fallbrook’s metrology lab. Image courtesy A. Richter.
The skills and machining knowledge gained at Fallbrook’s prototype shop can act as a springboard for those with higher aspirations. House noted three key workers left the company on friendly terms: the first two to start their own machine shops and the third to become a shop manager. “We’ve helped get those people there because of our environment.”
However, House added that the shop’s retention rate is quite good because workers’ satisfaction levels are high. “When you have people satisfied and engaged, they’re capable of giving you their best every day, and our quality level stays extremely high,” House said. “Rob has helped us prove that with his metrology department, but before Rob was here we still had a high level of quality; we just weren’t very good with checking it because we had manual inspection equipment.”
Measurement MattersHouse is talking about Robert Butler, Fallbrook’s engineering manager for metrology. The heart of his temperature-controlled metrology lab is a Zeiss Contura G2 coordinate measuring machine with 3D scanning. “That is our workhorse,” Butler said, “or our equivalent of a Makino machine for the metrology world.”
The lab specializes in first-article inspections and, in addition to the CMM, has a Mahr Formtester MMQ 400 semiautomatic measuring station, a Mahr XCR-20 contour and surface-roughness measurement system and an OGP SmartScope 500 vision measuring system. Similar to the prototype shop, Fallbrook offers metrology services to other companies besides its technology licensees, such as a small startup that is seeking to prove out its concepts and prototypes, Butler noted.
“What we are not designed to do is check 100 of every 10,000 parts coming off a production line,” Butler said, adding that the lab has two technicians besides himself. “We’re not set up for production any more than the prototype shop is, but what we’re set up to do is have extremely fast turnaround times for a wide range of applications.”
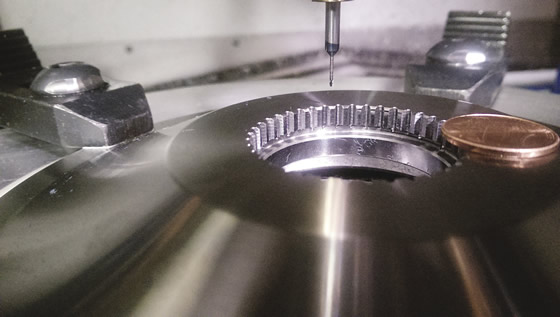
An involute spline is roughed with a 0.031”-dia. endmill. Image courtesy Fallbrook Technologies.
Butler emphasized that the metrology group takes surface-finish measurement seriously, because a fine surface finish positively impacts the durability of the company’s transmission hubs. The prototype shop struggled a bit in the past with its general-purpose machine tools, according to House, and, again, needed to be creative with machining parameters and cutting tool selection to overcome some of the hurdles to imparting fine surface finishes.
The Makino V56i VMC, however, enables the shop to achieve mirror finishes of 0.1µm Ra, House added. To convince company management of the benefit of investing in the V56i, the metrology department used the Zeiss CMM to show that a part machined on the VMC for 1 hour imparted a significantly finer surface finish than one that took 3 hours to produce on a general-purpose machine and also required 72 hours of tumble deburring.
Tool TimeWhen viewed under magnification, House said the surface finish produced on the 20,000-rpm VMC has a pattern similar to a checkerboard rather than the swirls seen when conventionally plunging standard ballnose endmills on a general-purpose machine. This is in part because the standard tools have grinding marks on the cutting edges that are transferred to the part, he explained, while the high-performance machine can apply high-end cutting tools that are honed to eliminate those marks. “If I take an expensive tool that has the geometry for high-speed machining and run it on a general-purpose piece of equipment that doesn’t have good runout and rigidity, I just burn it up and so I’m wasting money.”
When machining hard materials, House estimated that the VMC has reduced tool costs about 40 to 60 percent while reducing cycle times at least 35 percent. “We get about a 65 percent cycle-time reduction on certain work.”
In addition, the shop performs the flush fine milling concept on the high-performance VMC to impart fine finishes with the checkerboard pattern, House noted. That involves applying tools with sharp cutting edges at a high spindle speed while taking shallow cuts and a small step-over, effectively shearing a chip and sending the heat generated during the cut into the chip rather than the workpiece or tool.
“When we purchased the Makino machine, we were given some formulas that enable us to look at the surface-finish requirements and from those back-calculate and get all of our speeds and feeds,” House said.
Future high-performance machine tools might even use the continuously variable planetary technology. House said machine tool builders have inquired about replacing a variable-speed head with the CVP technology to enable smoother performance by eliminating the vibration and harmonics geared spindles can cause. “If you’re running gears, its clunk here’s a range and clunk here’s another range,” he said. “Continuously variable technology doesn’t have that so we can make adjustments, and avoiding harmonics might require just a small adjustment. It may be more efficient. It definitely would require less maintenance.”
The future may also find Fallbrook’s shop doing more than making prototypes. “Let’s say we were going to make a product in a quantity of 6,000 a year,” House said. “There is the potential that we would do that in-house. We would help set it up but probably not manage it. We can help build the entire production system, and it all stems from the fact that we know how to make one in the first place.”
For more information about Fallbrook Technologies Inc., visit www.fallbrooktech.com. CTE
Rigid machine enables smooth ride
Fallbrook Technologies Inc.’s NuVinci N360 continuously variable planetary (CVP) transmission hub replaces the cogs of gears and derailleurs that have been standard issue on multispeed bicycles for decades. Unlike conventional transmissions, the company’s hub enables riders to continuously, smoothly and silently change the bike’s drive ratio, because it has an “infinite” number of ratios within its 360 percent range.
With the nature of the traction-drive principle used in the CVP hub, surface finishes for its parts are critical and profile accuracy is required for proper operation. (That principle relates to two adjacent part surfaces forced close together to compress the traction fluid between them and transfer force from one part to the other.) Further complicating matters, because the transmission essentially also serves as a large bearing, it requires hardened materials—typically 52100 alloy steel hardened to 62 HRC—making tool life a significant concern as well. Fallbrook knew it had reached the limits of what creative processing could get from its commodity vertical machining centers and sought a hard-milling solution.
The company looked at outsourcing the prototyping work to a moldmaking shop, but the volume of parts needed were so small that the shop wouldn’t provide the quick turnaround Fallbrook required.
Fallbrook contacted several machine suppliers, requesting sample part runs for one of its more difficult parts, giving them aggressive cycle-time targets to push throughput as far as possible while improving part quality. Using its V56i VMC, Makino Inc., Mason, Ohio, was the first company to meet the requirements and deliver a sample part.
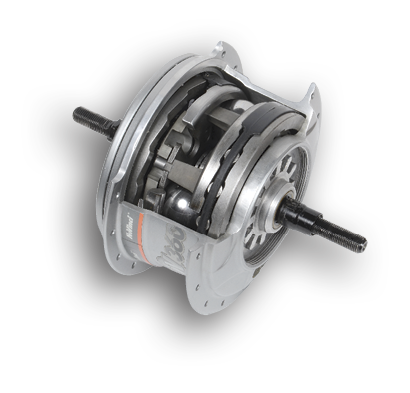
A cutaway of Fallbrook’s NuVinci continuously variable planetary transmission hub. Image courtesy Fallbrook Technologies.
As a part of his research, Fallbrook’s Mark House visited Makino and was taken to see a moldmaking customer that operates a V56i for hard milling. During the shop tour, House noticed something odd. “I realized that they didn’t have any metrology equipment in the shop,” he said. When he asked about it, he was informed that the shop was so confident in the VMC’s ability to hold a 0.0002 " (5µm) tolerance that it didn’t need verification. When there is a dispute, which doesn’t happen often, the shop’s policy is to go to a qualified third party to perform the measurement testing and resolve the issue.
After Fallbrook’s research was completed and the results from the test-part runs were in, it was time to calculate the return on investment. Fallbrook determined the V56i would provide a full repayment in 2 to 3 years. With leadership convinced, Fallbrook purchased a Makino V56i from Single Source Technologies, a supplier of machining, tooling and engineering services.
Partnering with SST and Makino, House and his team immediately began to test the machine’s capabilities by filling customer orders. Similar to the change in thinking it took for Fallbrook to look to moldmaking technology for its prototyping needs, it now realized a new perspective on the entire machining process. “We no longer have that wall—that equipment limitation, which previously stopped us dead in our tracks,” House explained. “Now we have fun. For example, rather than turning on one part, we chose to helical interpolate a traction surface on a large ring and held 2µm circularity.”
In addition, Fallbrook was able to increase speeds and feed rates by 35 to 65 percent on typical applications, and operators believe those numbers can eventually grow much larger with additional process optimization.
“Bringing innovations to market is what matters most to all of us at Fallbrook,” House said. “We’re not just here to make a profit. We want to make a positive impact on the world around us, producing lasting experiences that people can’t experience anywhere else.”
—Based on information provided by Makino Inc.
‘Turning gears into spheres’
Bill Klehm is CEO of Fallbrook Technologies and he shared his thoughts about the gear industry, manufacturing and intellectual property with Cutting Tool Engineering.
CTE: What is your vision for the company?
Bill Klehm: Turning gears into spheres. Gears have not fundamentally changed in 2,500 years. My belief 11 years ago, now going on 12, is the gearing industry might be the last fundamental industry that hasn’t been reinvented through technology. Obviously, gears have been improved, but there has been trillions of dollars deployed for improving gear sets and this continuously variable planetary technology is the first fundamental replacement for gears. We started with a dual path. One path was to create a commercial product. The bicycle drivetrain is the most efficient drivetrain ever created by man, where one unit of energy to peddle equals one unit of energy on the ground—you feel every loss between your legs. We are the fastest-growing drivetrain in Europe, with almost 40 percent of the luxury electric-bike segment. We positioned ourselves in the luxury segment at the beginning. In parallel with that, we have licenses in automotive and off-highway. Our licensing partners, including Dana Ltd. and Allison Transmission, have invested heavily in their development of applications for our technology over the last few years and now it is starting to flourish.
CTE: What role does machining play in that vision?
Klehm: Obviously, machining products is a big part of what we do, and over the last 100 years machined products haven’t been deemed “sexy.” Technology is all around electronics. We’re proving that mechanical technology can be attractive and sexy as well. With the advent of advanced computing and predictive modeling, as well as high-tech machining, we are enabling the replacement of gears.
CTE: How do you protect your intellectual property?
Bill Klehm, CEO of Fallbrook Technologies
Klehm: I have a general rule: trust and verify. It doesn’t worry me that somebody is going to copy Fallbrook. I’m concerned about it but not worried about it. The competitive advantage provided by our intellectual property coverage is so dominant that it is highly likely that anybody who wants to copy our products or our partners’ products would be put into a position where he would simply have to license or be found to infringe on our property rights. What we really do give people with our licensing model is the ability to practice the technology exclusively. Monopolies as a concept are not a bad thing when they serve the public good. Monopolies are where people make money. Everybody thinks open competition is where people make money. That’s not true. People make the most money when they have a monopoly. That’s ultimately where we are going: To create a monopoly, but offer our clients the opportunity to participate in that monopoly.
CTE: What are your plans for continuing to grow the business?
Klehm: The gearing industry is a $650 billion market, so it is a target-rich environment. If you’re going to address a target-rich environment you have to have a strong intellectual property-based business, and we have 700 patents or applications and over 14,000 patent claims. We have a government-sponsored, internationally sanctioned monopoly on the replacement for gears. We’re going to just keep doing what we’re doing: license, build the bicycle business and continue to teach. There are 225,000 mechanical engineers in North America, roughly a million mechanical engineers in the world, and one of our jobs in the next 12 to 18 months is to make sure every single one of those mechanical engineers knows that a variable planetary drive actually exists and what the benefit of it is. If you are in the rotating connection business, connecting power source to power use through some sort of rotating machinery, you want to consider the benefits that a variable planetary drive can give you.
—A. Richter
Related Glossary Terms
- centers
centers
Cone-shaped pins that support a workpiece by one or two ends during machining. The centers fit into holes drilled in the workpiece ends. Centers that turn with the workpiece are called “live” centers; those that do not are called “dead” centers.
- computer numerical control ( CNC)
computer numerical control ( CNC)
Microprocessor-based controller dedicated to a machine tool that permits the creation or modification of parts. Programmed numerical control activates the machine’s servos and spindle drives and controls the various machining operations. See DNC, direct numerical control; NC, numerical control.
- endmill
endmill
Milling cutter held by its shank that cuts on its periphery and, if so configured, on its free end. Takes a variety of shapes (single- and double-end, roughing, ballnose and cup-end) and sizes (stub, medium, long and extra-long). Also comes with differing numbers of flutes.
- feed
feed
Rate of change of position of the tool as a whole, relative to the workpiece while cutting.
- gang cutting ( milling)
gang cutting ( milling)
Machining with several cutters mounted on a single arbor, generally for simultaneous cutting.
- grinding
grinding
Machining operation in which material is removed from the workpiece by a powered abrasive wheel, stone, belt, paste, sheet, compound, slurry, etc. Takes various forms: surface grinding (creates flat and/or squared surfaces); cylindrical grinding (for external cylindrical and tapered shapes, fillets, undercuts, etc.); centerless grinding; chamfering; thread and form grinding; tool and cutter grinding; offhand grinding; lapping and polishing (grinding with extremely fine grits to create ultrasmooth surfaces); honing; and disc grinding.
- lathe
lathe
Turning machine capable of sawing, milling, grinding, gear-cutting, drilling, reaming, boring, threading, facing, chamfering, grooving, knurling, spinning, parting, necking, taper-cutting, and cam- and eccentric-cutting, as well as step- and straight-turning. Comes in a variety of forms, ranging from manual to semiautomatic to fully automatic, with major types being engine lathes, turning and contouring lathes, turret lathes and numerical-control lathes. The engine lathe consists of a headstock and spindle, tailstock, bed, carriage (complete with apron) and cross slides. Features include gear- (speed) and feed-selector levers, toolpost, compound rest, lead screw and reversing lead screw, threading dial and rapid-traverse lever. Special lathe types include through-the-spindle, camshaft and crankshaft, brake drum and rotor, spinning and gun-barrel machines. Toolroom and bench lathes are used for precision work; the former for tool-and-die work and similar tasks, the latter for small workpieces (instruments, watches), normally without a power feed. Models are typically designated according to their “swing,” or the largest-diameter workpiece that can be rotated; bed length, or the distance between centers; and horsepower generated. See turning machine.
- machining center
machining center
CNC machine tool capable of drilling, reaming, tapping, milling and boring. Normally comes with an automatic toolchanger. See automatic toolchanger.
- metrology
metrology
Science of measurement; the principles on which precision machining, quality control and inspection are based. See precision machining, measurement.
- milling
milling
Machining operation in which metal or other material is removed by applying power to a rotating cutter. In vertical milling, the cutting tool is mounted vertically on the spindle. In horizontal milling, the cutting tool is mounted horizontally, either directly on the spindle or on an arbor. Horizontal milling is further broken down into conventional milling, where the cutter rotates opposite the direction of feed, or “up” into the workpiece; and climb milling, where the cutter rotates in the direction of feed, or “down” into the workpiece. Milling operations include plane or surface milling, endmilling, facemilling, angle milling, form milling and profiling.
- milling machine ( mill)
milling machine ( mill)
Runs endmills and arbor-mounted milling cutters. Features include a head with a spindle that drives the cutters; a column, knee and table that provide motion in the three Cartesian axes; and a base that supports the components and houses the cutting-fluid pump and reservoir. The work is mounted on the table and fed into the rotating cutter or endmill to accomplish the milling steps; vertical milling machines also feed endmills into the work by means of a spindle-mounted quill. Models range from small manual machines to big bed-type and duplex mills. All take one of three basic forms: vertical, horizontal or convertible horizontal/vertical. Vertical machines may be knee-type (the table is mounted on a knee that can be elevated) or bed-type (the table is securely supported and only moves horizontally). In general, horizontal machines are bigger and more powerful, while vertical machines are lighter but more versatile and easier to set up and operate.
- parallel
parallel
Strip or block of precision-ground stock used to elevate a workpiece, while keeping it parallel to the worktable, to prevent cutter/table contact.
- sawing machine ( saw)
sawing machine ( saw)
Machine designed to use a serrated-tooth blade to cut metal or other material. Comes in a wide variety of styles but takes one of four basic forms: hacksaw (a simple, rugged machine that uses a reciprocating motion to part metal or other material); cold or circular saw (powers a circular blade that cuts structural materials); bandsaw (runs an endless band; the two basic types are cutoff and contour band machines, which cut intricate contours and shapes); and abrasive cutoff saw (similar in appearance to the cold saw, but uses an abrasive disc that rotates at high speeds rather than a blade with serrated teeth).
- step-over
step-over
Distance between the passes of the toolpath; the path spacing. The distance the tool will move horizontally when making the next pass. Too great of a step-over will cause difficulty machining because there will be too much pressure on the tool as it is trying to cut with too much of its surface area.
- tolerance
tolerance
Minimum and maximum amount a workpiece dimension is allowed to vary from a set standard and still be acceptable.
- turning
turning
Workpiece is held in a chuck, mounted on a face plate or secured between centers and rotated while a cutting tool, normally a single-point tool, is fed into it along its periphery or across its end or face. Takes the form of straight turning (cutting along the periphery of the workpiece); taper turning (creating a taper); step turning (turning different-size diameters on the same work); chamfering (beveling an edge or shoulder); facing (cutting on an end); turning threads (usually external but can be internal); roughing (high-volume metal removal); and finishing (final light cuts). Performed on lathes, turning centers, chucking machines, automatic screw machines and similar machines.