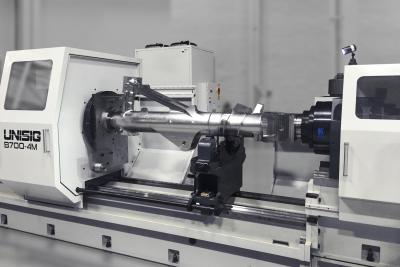
UNISIG engineered its new B700 Drop Bed machine to effectively generate the critical, high-precision features on large and irregularly shaped aerospace components, such as landing gear struts. Conversely, the flexibility of the machine allows it to also process medium-sized, more uniform-shaped workpieces with minimal changeover time from one to another.
The B700 offers an expansive working range with its servo programmable workpiece headstock capability, yet it sports a streamlined overall footprint that makes for spacesaving installations and enhanced ergonomics. This is unlike other comparable deep hole drilling machines that are often inflexible dedicated systems as well as oversized and cumbersome.
A 63" (1600 mm) swing over bed size along with the programmable moving headstock allow the B700 to process parts as long as 157" (4000 mm) or as short as 20" (500mm). In addition to high-precision deep hole drilling, the machine’s operational capabilities include other complex deep hole machining operations necessary in the production of other aerospace parts such as axles, beams, control rods and components for actuators. These include capabilities such as internal contouring via an optional servo bottle boring axis.
For performance and superior process control, the B700 packs a preloaded drive system together with high horsepower and precisely controlled in-process feedback system for real-time monitoring. With a 126-hp tool spindle and 90-hp work spindle, the machine productively solid bores up to 8" (200 mm) diameters and counterbores to 12" (300 mm) diameters. Another productivity-enhancing feature is a 250-gpm coolant flow for heat reduction, efficient chip evacuation and superior surface finish quality.
The B700 machine expands UNISIG’s extensive B-series line for on-center drilling of cylindrical workpieces in applications, such as aerospace, defense and oil & gas. In addition to standard BTA drilling methods, these machines are also capable of counterboring, trepanning and skiving and roller burnishing processes, achieving the extremely strict tolerances required by manufacturers in these and other industries.
Contact Details
Related Glossary Terms
- boring
boring
Enlarging a hole that already has been drilled or cored. Generally, it is an operation of truing the previously drilled hole with a single-point, lathe-type tool. Boring is essentially internal turning, in that usually a single-point cutting tool forms the internal shape. Some tools are available with two cutting edges to balance cutting forces.
- burnishing
burnishing
Finishing method by means of compressing or cold-working the workpiece surface with carbide rollers called burnishing rolls or burnishers.
- coolant
coolant
Fluid that reduces temperature buildup at the tool/workpiece interface during machining. Normally takes the form of a liquid such as soluble or chemical mixtures (semisynthetic, synthetic) but can be pressurized air or other gas. Because of water’s ability to absorb great quantities of heat, it is widely used as a coolant and vehicle for various cutting compounds, with the water-to-compound ratio varying with the machining task. See cutting fluid; semisynthetic cutting fluid; soluble-oil cutting fluid; synthetic cutting fluid.
- counterboring
counterboring
Enlarging one end of a drilled hole. The enlarged hole, which is concentric with the original hole, is flat on the bottom. Counterboring is used primarily to set bolt heads and nuts below the workpiece surface.
- process control
process control
Method of monitoring a process. Relates to electronic hardware and instrumentation used in automated process control. See in-process gaging, inspection; SPC, statistical process control.
- trepanning
trepanning
Drilling deep holes that are too large to be drilled by high-pressure coolant drills or gundrills. Trepanning generates a solid core and normally requires a big, powerful machine. Shallow trepanning operations can be performed on modified engine or turret lathes or on boring machines. See boring; drilling; spade drilling.