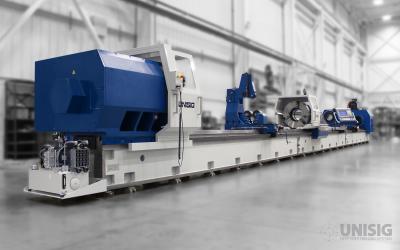
UNISIG has unveiled newly developed technologies that substantially improve performance while reducing cost in its larger B-series machines. These advances are introduced in the newly launched B850 model and will be integrated into larger models in the series. When designing the B850, UNISIG evaluated all aspects of the previous designs. The
bed and rack-and-pinion system were retained, while feed systems were modernized to improve rigidity and reduce backlash. A new high-performance, helical-geared transmission was incorporated in a three-range, automatically shifting headstock.
Incorporation of modern gearing and power train concepts simplified construction of the machine, reducing cost and boosting reliability and performance. The B850 also offers a standard programmable coolant system. Combined with userfriendly controls and the other new design features, the machine allows an operator to focus on the part being machined instead of managing a wide variety of manual functions.
Both the work and tool headstocks deliver 166 hp, providing the high power and torque needed to drill holes up to 7.1” (180 mm) in nickel alloys, 8.7” (221 mm) in carbon steel, and 12.6” (320 mm) with counterboring. The B850 model is available with maximum drill depths ranging from 78” to 65’ (1.98 m to 19.81 m), and the machine bed can
accommodate workpieces up to 10 tons (9,071 kg).
The B850 is part of UNISIG’s extensive B-series line, designed for on-center drilling of round workpieces in applications such as aerospace, defense, and oil and gas. In addition to standard BTA drilling methods, these machines are also capable of counterboring, trepanning, and skiving and roller burnishing processes, achieving the extremely strict tolerances required by manufacturers in these and other industries.
Contact Details
Related Glossary Terms
- alloys
alloys
Substances having metallic properties and being composed of two or more chemical elements of which at least one is a metal.
- backlash
backlash
Reaction in dynamic motion systems where potential energy that was created while the object was in motion is released when the object stops. Release of this potential energy or inertia causes the device to quickly snap backward relative to the last direction of motion. Backlash can cause a system’s final resting position to be different from what was intended and from where the control system intended to stop the device.
- burnishing
burnishing
Finishing method by means of compressing or cold-working the workpiece surface with carbide rollers called burnishing rolls or burnishers.
- coolant
coolant
Fluid that reduces temperature buildup at the tool/workpiece interface during machining. Normally takes the form of a liquid such as soluble or chemical mixtures (semisynthetic, synthetic) but can be pressurized air or other gas. Because of water’s ability to absorb great quantities of heat, it is widely used as a coolant and vehicle for various cutting compounds, with the water-to-compound ratio varying with the machining task. See cutting fluid; semisynthetic cutting fluid; soluble-oil cutting fluid; synthetic cutting fluid.
- counterboring
counterboring
Enlarging one end of a drilled hole. The enlarged hole, which is concentric with the original hole, is flat on the bottom. Counterboring is used primarily to set bolt heads and nuts below the workpiece surface.
- feed
feed
Rate of change of position of the tool as a whole, relative to the workpiece while cutting.
- trepanning
trepanning
Drilling deep holes that are too large to be drilled by high-pressure coolant drills or gundrills. Trepanning generates a solid core and normally requires a big, powerful machine. Shallow trepanning operations can be performed on modified engine or turret lathes or on boring machines. See boring; drilling; spade drilling.