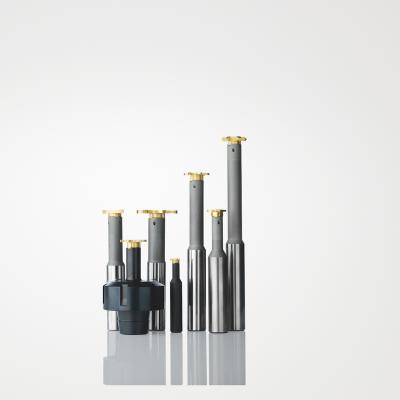
Seco has further expanded its selection of disc milling inserts and cutter bodies to meet customer demands for reliable, high performing cutters. With that, the company has introduced the 335.14 small-diameter exchangeable head system, 335.16 cutter for T-slot operations and cassette versions of its 335.25 cutter that incorporate round inserts.
Using small-diameter exchangeable carbide heads, the 335.14 offers a versatile, precise cutting profile that easily tackles any type of material, according to the company. These cutters are ideal for groove milling, circlip grooves, full radius profiles, threading profiles and chamfering. Reliable exchangeable head systems control machining costs, and the 335.14 product line comes in a variety of cylindrical and integrated collet chuck shanks in diameters from 0.38" (9.7 mm) to 1.37" (34.7 mm) that cut widths from 0.03" (0.74 mm) to 0.207" (5.26 mm.)
Seco’s stable 335.16 cutters incorporate four-edged inserts to economically perform demanding T-slot operations. Modern insert geometries reduce machining forces and noise for optimal tool life. Centralized cooling channels effectively remove chips and provide excellent surface finishes and finished part quality. Cutters come in diameters from 0.97" (25 mm) to 1.844" (50 mm) based on standardized T-slot dimensions. The expansive selection of insert geometries and grades cut many materials in widths ranging from 0.39" (11 mm) to 0.82" (21 mm.)
The expanded line of 335.25 disc mill cutters includes new cassettes for 0.63" (16-mm) and 0.79" (20 mm) round insert diameters. These cutters perform well in various full side, face or half side and face operations for applications involving corner radii. The exchangeable cassettes ensure long, reliable cutter performance, while the large choice of insert geometries and grades provide freer cutting operations and increase cost-efficiency in any type of material. Cutter diameters for these new sizes range from 4.00" (100 mm) to 12.00" (315 mm.)
Contact Details
Related Glossary Terms
- chamfering
chamfering
Machining a bevel on a workpiece or tool; improves a tool’s entrance into the cut.
- chuck
chuck
Workholding device that affixes to a mill, lathe or drill-press spindle. It holds a tool or workpiece by one end, allowing it to be rotated. May also be fitted to the machine table to hold a workpiece. Two or more adjustable jaws actually hold the tool or part. May be actuated manually, pneumatically, hydraulically or electrically. See collet.
- collet
collet
Flexible-sided device that secures a tool or workpiece. Similar in function to a chuck, but can accommodate only a narrow size range. Typically provides greater gripping force and precision than a chuck. See chuck.
- gang cutting ( milling)
gang cutting ( milling)
Machining with several cutters mounted on a single arbor, generally for simultaneous cutting.
- milling
milling
Machining operation in which metal or other material is removed by applying power to a rotating cutter. In vertical milling, the cutting tool is mounted vertically on the spindle. In horizontal milling, the cutting tool is mounted horizontally, either directly on the spindle or on an arbor. Horizontal milling is further broken down into conventional milling, where the cutter rotates opposite the direction of feed, or “up” into the workpiece; and climb milling, where the cutter rotates in the direction of feed, or “down” into the workpiece. Milling operations include plane or surface milling, endmilling, facemilling, angle milling, form milling and profiling.
- milling machine ( mill)
milling machine ( mill)
Runs endmills and arbor-mounted milling cutters. Features include a head with a spindle that drives the cutters; a column, knee and table that provide motion in the three Cartesian axes; and a base that supports the components and houses the cutting-fluid pump and reservoir. The work is mounted on the table and fed into the rotating cutter or endmill to accomplish the milling steps; vertical milling machines also feed endmills into the work by means of a spindle-mounted quill. Models range from small manual machines to big bed-type and duplex mills. All take one of three basic forms: vertical, horizontal or convertible horizontal/vertical. Vertical machines may be knee-type (the table is mounted on a knee that can be elevated) or bed-type (the table is securely supported and only moves horizontally). In general, horizontal machines are bigger and more powerful, while vertical machines are lighter but more versatile and easier to set up and operate.
- threading
threading
Process of both external (e.g., thread milling) and internal (e.g., tapping, thread milling) cutting, turning and rolling of threads into particular material. Standardized specifications are available to determine the desired results of the threading process. Numerous thread-series designations are written for specific applications. Threading often is performed on a lathe. Specifications such as thread height are critical in determining the strength of the threads. The material used is taken into consideration in determining the expected results of any particular application for that threaded piece. In external threading, a calculated depth is required as well as a particular angle to the cut. To perform internal threading, the exact diameter to bore the hole is critical before threading. The threads are distinguished from one another by the amount of tolerance and/or allowance that is specified. See turning.