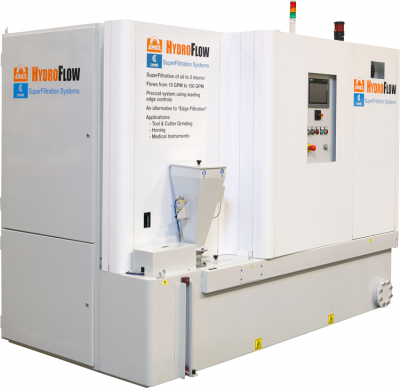
Eriez HydroFlow reports that a growing number of leading manufacturers from around the globe are utilizing the company’s Comat superfiltration systems on thousands of machine tools, superfiltering 530,000 U.S. gallons of metalworking oil every minute. This technology is opening up new opportunities for these customers by eliminating restrictions on the types of metal they can filter, decreasing costs and reducing labor requirements.
Eriez Manager, Filtration Systems Darrell Milton explains that Eriez HydroFlow superfiltration systems remove particles down to 3-micron nominal and provide a number of advantages over competitors’ offerings. He says, “Our technology eliminates the need for filter replacements, a common requirement for other companies’ filtration systems which leads to thousands of dollars of costs for users. Not only do our systems enable customers to filter any kind of metal, they also provide a consistent flow rate output. This eliminates clogging issues often associated with lower-quality systems.”
Eriez HydroFlow also gives users the power of state-of-the-art monitoring technology for greater control and flexibility. Customers can use their PC, tablet or smartphone to remotely monitor, manage and adjust their superfiltration system. Milton says, “With our remote app, it is possible to monitor our Superfiltration Systems in real time and immediately choose an Adaptive Optimization Cycle to meet different daily working conditions of machine tools.”
Eriez HydroFlow partnered with Milan, Italy-based Comat S.r.l. to bring superfiltration technology to North America in 2016 and, according to the company, the response in the marketplace has been overwhelmingly positive. Eriez HydroFlow superfiltration systems are most often connected with grinders, sharpening, lapping and honing machines. They are also commonly applied to automatic lathe units to filter oil recovered from chips centrifugation, from the periodic emptying of the tanks and for the oil used at high pressure for the drilling process. A diverse range of markets rely on superfiltration systems, including aerospace, medical, automotive, bearings, glass machining, tools manufacturing and sharpening and saw blade manufacturing.
Contact Details
Related Glossary Terms
- lapping
lapping
Finishing operation in which a loose, fine-grain abrasive in a liquid medium abrades material. Extremely accurate process that corrects minor shape imperfections, refines surface finishes and produces a close fit between mating surfaces.
- lathe
lathe
Turning machine capable of sawing, milling, grinding, gear-cutting, drilling, reaming, boring, threading, facing, chamfering, grooving, knurling, spinning, parting, necking, taper-cutting, and cam- and eccentric-cutting, as well as step- and straight-turning. Comes in a variety of forms, ranging from manual to semiautomatic to fully automatic, with major types being engine lathes, turning and contouring lathes, turret lathes and numerical-control lathes. The engine lathe consists of a headstock and spindle, tailstock, bed, carriage (complete with apron) and cross slides. Features include gear- (speed) and feed-selector levers, toolpost, compound rest, lead screw and reversing lead screw, threading dial and rapid-traverse lever. Special lathe types include through-the-spindle, camshaft and crankshaft, brake drum and rotor, spinning and gun-barrel machines. Toolroom and bench lathes are used for precision work; the former for tool-and-die work and similar tasks, the latter for small workpieces (instruments, watches), normally without a power feed. Models are typically designated according to their “swing,” or the largest-diameter workpiece that can be rotated; bed length, or the distance between centers; and horsepower generated. See turning machine.
- metalworking
metalworking
Any manufacturing process in which metal is processed or machined such that the workpiece is given a new shape. Broadly defined, the term includes processes such as design and layout, heat-treating, material handling and inspection.
- sawing machine ( saw)
sawing machine ( saw)
Machine designed to use a serrated-tooth blade to cut metal or other material. Comes in a wide variety of styles but takes one of four basic forms: hacksaw (a simple, rugged machine that uses a reciprocating motion to part metal or other material); cold or circular saw (powers a circular blade that cuts structural materials); bandsaw (runs an endless band; the two basic types are cutoff and contour band machines, which cut intricate contours and shapes); and abrasive cutoff saw (similar in appearance to the cold saw, but uses an abrasive disc that rotates at high speeds rather than a blade with serrated teeth).