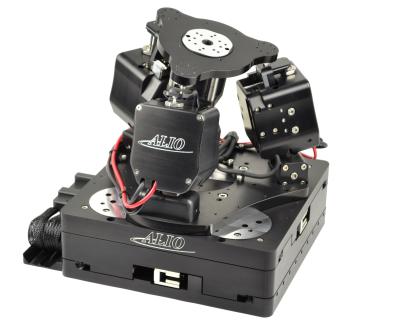
In response to the demand from industry for more and more versatile and accurate motion control systems, market-leader ALIO Industries has just received a U.S. patent on the next generation Hybrid Hexapod technology. The Hybrid Hexapod is a game-changer in the field of motion control, and will stimulate innovation as an enabler of next-generation manufacturing processes.
Hexapods have a long history in motion control applications, but in recent years traditional 6 degrees of freedom (6-DOF) positioning devices have been found wanting when confronted with the industry demand for higher accuracy, improved repeatability and better geometric performance.
Simply speaking, hexapods are devices where six links or actuators (that extend and retract) join a stationary bottom plate with a top plate that performs coordinated motion in 6-DOF. A sample, fixture, sensor or any device can be mounted on the top plate and can be manipulated to be in any location and orientation in the available range of travel.
In complex applications where high precision, 6-DOF motion is required, a hexapod is the go-to solution due to its compact size and that it is more reliable than serial stacked stages with their inherent stack-up of errors, alignment difficulties, and cable management issues.
With the exponential demand across industry for sub-micron levels of miniaturization and the requirements for process applications motion systems that move from micro to nano levels of precision, traditional hexapods cannot achieve the desired results.
This is due to performance limitations inherent in traditional hexapod designs that require the accurate coordination of the movement of all six axes to accomplish a motion profile, even if the requirement is only for a simple single-axis motion. In addition, despite the fact that the general perception is that hexapods exhibit good stiffness compared to serial stacked multiple-axis systems, this is really only in the vertical Z-axis, with weaknesses in the “xy” plane.
ALIO’s Hybrid Hexapod takes a different approach to traditional 6-DOF positioning devices and exhibits much higher performance at extremely competitive prices. Rather than six independent legs (and 12 connection joints) ALIO’s approach combines a precision XY monolithic stage, tripod and continuous rotation theta-Z axis to provide superior overall performance.
The combination of serial and parallel kinematics at the heart of ALIO’s 6-D Nano Precision stages renders traditional hexapod kinematics obsolete, with orders-of-magnitude improvements in precision, path performance, speed, stiffness and a larger work envelope with virtually unlimited XY travel, and fully programmable tool center point locations.
ALIO’s Hybrid Hexapod has less than 100 nm 3D 6-axis Point Precision repeatability, making it an essential technology for mission critical applications in the laser processing, optical inspection, photonics, semiconductor, metrology, and medical device sectors, and indeed all micromachining projects.
A major photonics customer recently commented: “We demanded an NDA to ensure ALIO does not even mention our company since the ALIO Hybrid Hexapod is a game changer in our industry.” With multiple Hybrid Hexapods in service, the high expectations of this customer have been exceeded.
Related Glossary Terms
- degrees of freedom
degrees of freedom
Number of axes along which a robot, and thus the object it is holding, can be manipulated. Most robots are capable of maneuvering along the three basic Cartesian axes (X, Y, Z). More sophisticated models may move in six or more axes. See axis.
- fixture
fixture
Device, often made in-house, that holds a specific workpiece. See jig; modular fixturing.
- metrology
metrology
Science of measurement; the principles on which precision machining, quality control and inspection are based. See precision machining, measurement.
- parallel
parallel
Strip or block of precision-ground stock used to elevate a workpiece, while keeping it parallel to the worktable, to prevent cutter/table contact.
- stiffness
stiffness
1. Ability of a material or part to resist elastic deflection. 2. The rate of stress with respect to strain; the greater the stress required to produce a given strain, the stiffer the material is said to be. See dynamic stiffness; static stiffness.
- work envelope
work envelope
Cube, sphere, cylinder or other physical space within which the cutting tool is capable of reaching.