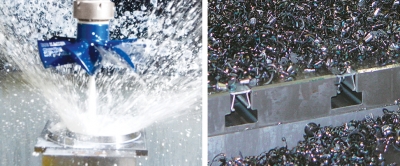
BIG KAISER has two powerful accessories crafted to improve in-process efficiency: ChipFans and T-slot covers. When used together with a machine that delivers on speed and accuracy, these accessories help machines reach maximum levels of productivity—even during downtime.
Chip fans offer many benefits when it comes to mitigating production issues and providing visible results. Mounting securely in either a collet chuck or end mill holder, chips fans are designed to integrate seamlessly into current machining cycles. In-process cleaning is created without halting production. Chip fan cycles can even be programmed to minimize spindle downtime and maximize operator efficiency.
A pre-drilled hole allows spindles to shoot coolant through the center of the fan to rinse tables, fixtures and workpieces. Two cleaning operations in one happen as the fan rotates, removing the chips and coolant. This makes a safe and economical alternative that requires little to no operator interaction.
Similar to the ChipFan, the T-slot cover tool accessory serves to optimize machine performance, minimize manual operations and keep things running smoothly. The protection plates are designed with productivity in mind, preventing chips and coolant from collecting in machining centers and interfering with work. The covers easily keep slots clear of debris when not in use.
The T-slot covers are easy to remove as soon as the machine slots are ready to be used, allowing access to a clean fixturing surface and quick setup changes. Both the T-slot cover and ChipFan are part of BIG KAISER’s extensive offering of efficiency, safety and durability-boosting accessories.
Contact Details
Related Glossary Terms
- centers
centers
Cone-shaped pins that support a workpiece by one or two ends during machining. The centers fit into holes drilled in the workpiece ends. Centers that turn with the workpiece are called “live” centers; those that do not are called “dead” centers.
- chuck
chuck
Workholding device that affixes to a mill, lathe or drill-press spindle. It holds a tool or workpiece by one end, allowing it to be rotated. May also be fitted to the machine table to hold a workpiece. Two or more adjustable jaws actually hold the tool or part. May be actuated manually, pneumatically, hydraulically or electrically. See collet.
- collet
collet
Flexible-sided device that secures a tool or workpiece. Similar in function to a chuck, but can accommodate only a narrow size range. Typically provides greater gripping force and precision than a chuck. See chuck.
- coolant
coolant
Fluid that reduces temperature buildup at the tool/workpiece interface during machining. Normally takes the form of a liquid such as soluble or chemical mixtures (semisynthetic, synthetic) but can be pressurized air or other gas. Because of water’s ability to absorb great quantities of heat, it is widely used as a coolant and vehicle for various cutting compounds, with the water-to-compound ratio varying with the machining task. See cutting fluid; semisynthetic cutting fluid; soluble-oil cutting fluid; synthetic cutting fluid.
- milling machine ( mill)
milling machine ( mill)
Runs endmills and arbor-mounted milling cutters. Features include a head with a spindle that drives the cutters; a column, knee and table that provide motion in the three Cartesian axes; and a base that supports the components and houses the cutting-fluid pump and reservoir. The work is mounted on the table and fed into the rotating cutter or endmill to accomplish the milling steps; vertical milling machines also feed endmills into the work by means of a spindle-mounted quill. Models range from small manual machines to big bed-type and duplex mills. All take one of three basic forms: vertical, horizontal or convertible horizontal/vertical. Vertical machines may be knee-type (the table is mounted on a knee that can be elevated) or bed-type (the table is securely supported and only moves horizontally). In general, horizontal machines are bigger and more powerful, while vertical machines are lighter but more versatile and easier to set up and operate.