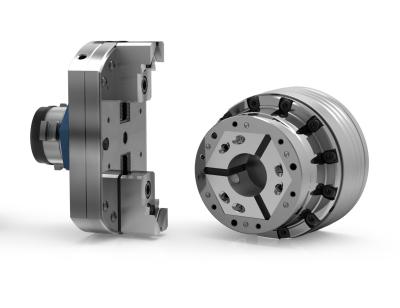
When you have a wide range of part diameters, configurations and small quantities, the dream setup would be to have maximum flexibility. Dreams turn to reality with the HAINBUCH’s modular system. Whether you’re working with round, prismatic, small or larger components, virtually any workholding configuration is possible with their modular system. The various workholding adapters can be installed in two minutes or less. HAINBUCH’s designers and engineers in Germany are constantly expanding its modular system to offer you the best workholding solutions. Something was missing though: an adaptation to clamp cubic parts. That's why HAINBUCH is pleased to introduce the 2-jaw module. Dreams do come true!
Modular system: flexible, more flexible, most flexible
Round workpieces are clamped from the outside with clamping heads (collets) within the collet chuck. Larger diameter workpieces, beyond the capacity of the collet chuck, can be clamped with the 3-jaw module. For cubic parts that are positioned centrically on machining centers and milling machines, the NEW 2-jaw module is now an option. You can change-over from clamping round parts to cubic ones in less than two minutes.
The 2-jaw module can handle turning applications up to 1,500 RPM. Due to its compact profile, it is the perfect alternative to large and heavy centric vises. The 2-jaw and 3-jaw module use the HAINBUCH collet chuck as their base. Change-over is possible without removing the collet chuck and realignment thanks to HAINBUCH’s Centrex quick-change interface.
Small, light and capable of multitasking
HAINBUCH’s modular solution, consisting of a chuck and jaw module, no longer compare to the large and heavy vises that are found in many shops and whose size is more of an obstacle than an advantage. As is often the case, the workholding is much larger than the part to be machined so interference is an issue. Special, longer tools are then needed and there’s a risk of a costly collision. The HAINBUCH modular system, on the other hand, is just as efficient and flexible as your multitasking machine tools are today.
Contact Details
Related Glossary Terms
- centers
centers
Cone-shaped pins that support a workpiece by one or two ends during machining. The centers fit into holes drilled in the workpiece ends. Centers that turn with the workpiece are called “live” centers; those that do not are called “dead” centers.
- chuck
chuck
Workholding device that affixes to a mill, lathe or drill-press spindle. It holds a tool or workpiece by one end, allowing it to be rotated. May also be fitted to the machine table to hold a workpiece. Two or more adjustable jaws actually hold the tool or part. May be actuated manually, pneumatically, hydraulically or electrically. See collet.
- collet
collet
Flexible-sided device that secures a tool or workpiece. Similar in function to a chuck, but can accommodate only a narrow size range. Typically provides greater gripping force and precision than a chuck. See chuck.
- gang cutting ( milling)
gang cutting ( milling)
Machining with several cutters mounted on a single arbor, generally for simultaneous cutting.
- milling
milling
Machining operation in which metal or other material is removed by applying power to a rotating cutter. In vertical milling, the cutting tool is mounted vertically on the spindle. In horizontal milling, the cutting tool is mounted horizontally, either directly on the spindle or on an arbor. Horizontal milling is further broken down into conventional milling, where the cutter rotates opposite the direction of feed, or “up” into the workpiece; and climb milling, where the cutter rotates in the direction of feed, or “down” into the workpiece. Milling operations include plane or surface milling, endmilling, facemilling, angle milling, form milling and profiling.
- turning
turning
Workpiece is held in a chuck, mounted on a face plate or secured between centers and rotated while a cutting tool, normally a single-point tool, is fed into it along its periphery or across its end or face. Takes the form of straight turning (cutting along the periphery of the workpiece); taper turning (creating a taper); step turning (turning different-size diameters on the same work); chamfering (beveling an edge or shoulder); facing (cutting on an end); turning threads (usually external but can be internal); roughing (high-volume metal removal); and finishing (final light cuts). Performed on lathes, turning centers, chucking machines, automatic screw machines and similar machines.