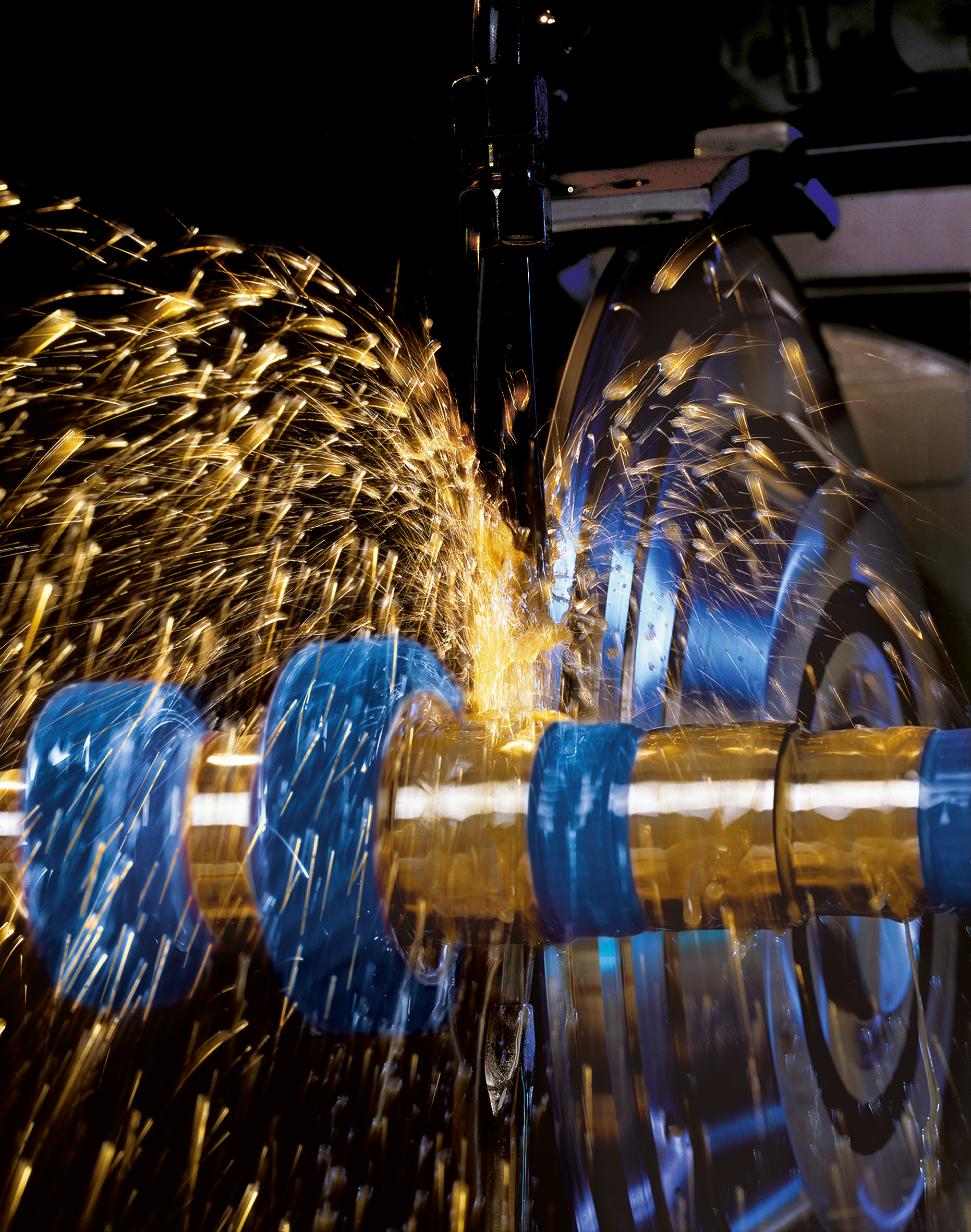
Kratzer GmbH & Co. is a Offenburg, Germany-based precision manufacturer of components made from a wide range of materials. These components are often produced in small batches and they must meet the exacting standards required by Kratzer's high-tech customers.
The company meets these specifications in part through investing in state-of-the-art equipment including flexible grinding machines, machining centers, lathes, and metrology equipment. Recently, the company invested in new grinding technology as well as a new filtration system to increase capacity and worker safety.
The company, with manufacturing facilities in Germany and the Czech Republic, integrated a Jumat cylindrical grinding machine from The Junker Group in Nordrach, Germany, to manufacture highly complex workpieces for dual-clutch gearboxes.
With the Jumat 3000, Kratzer manufactures gear parts for high-performance gearboxes for sports cars. To produce small batches of different dual-clutch components, Kratzer required flexibility with minimized tooling time and extreme precision. The three spindle 3000/60 cylindrical grinding machine proves itself as the ideal basis for production of the sophisticated components, according to Florian Kratzer, managing director at Kratzer GmbH & Co. KG.
The dual-clutch gearboxes for sports cars must meet the highest standards and therefore require extremely tight tolerances. The Jumat combines precision and process stability with flexibility and speed, he said.
The gear components are ground in batch sizes of around 3,000 pieces. From the outset, the retooling required between the different workpiece jobs was included in the development of the process and, in the end, reduced to a minimum. “The old machine has to be retooled several times a week,” said Kratzer. “With the Jumat, we have found a flexible cylindrical grinding machine that covers these many different grinding operations with reduced tooling time.”
Clean air with central extraction
Kratzer also invested in new filtration technology for new production space at its facility in Offenburg. The system from LTA Lufttechnik GmbH, a member of the The Junker Group of companies, was installed for the extraction of particles from 21 emulsion machines and four oil machines.
Central extraction removes harmful particles between 0.001µm and 100µm from a wide range of machine tools such as lathes and grinding machines with oil and emulsion. Central filtration systems also maximize space and optimize maintenance. This individual, centralized solution means that Kratzer can achieve optimal air supply in its new hall.
The 5,000m² production space is divided into three hall sections and includes the central filtration system. An additional filtration system cleans the exhaust from four oil machines in Hall 1. A blower with 16,000 m3/h power also ensures constant extraction via a piping system with an average length of around 150 meters. An automatic volume flow control regulates each filtration system for maximum energy efficiency. The central extraction can then use a signal line to detect the operating status of the different machines and automatically set the ideal operating point by specifically regulating the blower and different butterfly valves, said Kratzer.
During the planning phase, LTA and Kratzer identified the most crucial aspects of this project, which were safety, seamless installation of the future-proof systems, and reliable service. With an innovative and sustainable concept, LTA Lufttechnik GmbH developed the perfect solution for this new production hall, he said.
“We wanted to continuously improve the workplace and machine conditions.” he added. “With the new production hall, we have therefore opted for a central extraction system from LTA Lufttechnik GmbH because the entire package simply works for us.”
The Junker Group, which is based in Nordrach, Germany, manufactures CBN high-speed grinding machines and other manufacturing technologies through its group of companies. The company can be reached at +49 (0) 7838 84-0 or by visiting them at www.junker-group.com.
Contact Details
Related Glossary Terms
- centers
centers
Cone-shaped pins that support a workpiece by one or two ends during machining. The centers fit into holes drilled in the workpiece ends. Centers that turn with the workpiece are called “live” centers; those that do not are called “dead” centers.
- cubic boron nitride ( CBN)
cubic boron nitride ( CBN)
Crystal manufactured from boron nitride under high pressure and temperature. Used to cut hard-to-machine ferrous and nickel-base materials up to 70 HRC. Second hardest material after diamond. See superabrasive tools.
- cylindrical grinding
cylindrical grinding
Grinding operation in which the workpiece is rotated around a fixed axis while the grinding wheel is fed into the outside surface in controlled relation to the axis of rotation. The workpiece is usually cylindrical, but it may be tapered or curvilinear in profile. See centerless grinding; grinding.
- emulsion
emulsion
Suspension of one liquid in another, such as oil in water.
- grinding
grinding
Machining operation in which material is removed from the workpiece by a powered abrasive wheel, stone, belt, paste, sheet, compound, slurry, etc. Takes various forms: surface grinding (creates flat and/or squared surfaces); cylindrical grinding (for external cylindrical and tapered shapes, fillets, undercuts, etc.); centerless grinding; chamfering; thread and form grinding; tool and cutter grinding; offhand grinding; lapping and polishing (grinding with extremely fine grits to create ultrasmooth surfaces); honing; and disc grinding.
- grinding machine
grinding machine
Powers a grinding wheel or other abrasive tool for the purpose of removing metal and finishing workpieces to close tolerances. Provides smooth, square, parallel and accurate workpiece surfaces. When ultrasmooth surfaces and finishes on the order of microns are required, lapping and honing machines (precision grinders that run abrasives with extremely fine, uniform grits) are used. In its “finishing” role, the grinder is perhaps the most widely used machine tool. Various styles are available: bench and pedestal grinders for sharpening lathe bits and drills; surface grinders for producing square, parallel, smooth and accurate parts; cylindrical and centerless grinders; center-hole grinders; form grinders; facemill and endmill grinders; gear-cutting grinders; jig grinders; abrasive belt (backstand, swing-frame, belt-roll) grinders; tool and cutter grinders for sharpening and resharpening cutting tools; carbide grinders; hand-held die grinders; and abrasive cutoff saws.
- metrology
metrology
Science of measurement; the principles on which precision machining, quality control and inspection are based. See precision machining, measurement.