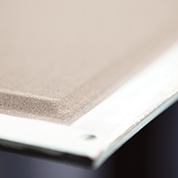
Drawing on its specialist knowledge of wear-resistant alloys, Wall Colmonoy has launched a new range of wear plates which will be marketed under the brand, ColWear. Leveraging its metallurgical expertise to develop new and innovative products, Wall Colmonoy presents a superior wear plate with lifetime beyond traditional competitors in the marketplace. ColWear plates are produced using proprietary Colmonoy® nickel and Wallex® cobalt alloys, with optional tungsten carbide. Vacuum-furnace production techniques developed over decades have been used to improve the metallurgical properties of the alloy matrix.
Wall Colmonoy’s new line of ColWear plates achieve superior resistance to wear in industries such as chemical processing, power, steel, mining and cement.
ColWear has had success within the petrochemical industry, where harsh conditions of abrasion, corrosion, heat and erosion are common. “We know that stopping production to perform maintainence in the petrochemical industry is difficult, dangerous, costly and inconvenient,” states Dr. Lewis Berry, Business Development Manager. “We have a solution that can greatly extend service life in extreme conditions, which is a game changer for these customers”. ColWear plates perform in industries where demands for wear resistance are high, such as chemical processing, power (waste to energy, biomass), steel, cement, and mining. ColWear plates extend service life - reducing costs, maintenance and downtime.
One of the big breakthroughs in developing ColWear plates was achieving superior resistance to abrasion, whilst at the same time offering excellent heat and corrosion resistant properties. ColWear plates are in strong demand for processes such as separation, grinding, conveying, where abrasive material is a key wear issue.
ColWear plates are also significantly lighter and more uniform than traditional chromium carbide or tungsten carbide plate, and early feedback suggest customers are keen to take advantage of these benefits. These properties make it ideal for applications such as industrial fans, where lighter materials improve the energy efficiency and balance.
Contact Details
Related Glossary Terms
- abrasive
abrasive
Substance used for grinding, honing, lapping, superfinishing and polishing. Examples include garnet, emery, corundum, silicon carbide, cubic boron nitride and diamond in various grit sizes.
- alloys
alloys
Substances having metallic properties and being composed of two or more chemical elements of which at least one is a metal.
- grinding
grinding
Machining operation in which material is removed from the workpiece by a powered abrasive wheel, stone, belt, paste, sheet, compound, slurry, etc. Takes various forms: surface grinding (creates flat and/or squared surfaces); cylindrical grinding (for external cylindrical and tapered shapes, fillets, undercuts, etc.); centerless grinding; chamfering; thread and form grinding; tool and cutter grinding; offhand grinding; lapping and polishing (grinding with extremely fine grits to create ultrasmooth surfaces); honing; and disc grinding.
- tungsten carbide ( WC)
tungsten carbide ( WC)
Intermetallic compound consisting of equal parts, by atomic weight, of tungsten and carbon. Sometimes tungsten carbide is used in reference to the cemented tungsten carbide material with cobalt added and/or with titanium carbide or tantalum carbide added. Thus, the tungsten carbide may be used to refer to pure tungsten carbide as well as co-bonded tungsten carbide, which may or may not contain added titanium carbide and/or tantalum carbide.
- wear resistance
wear resistance
Ability of the tool to withstand stresses that cause it to wear during cutting; an attribute linked to alloy composition, base material, thermal conditions, type of tooling and operation and other variables.