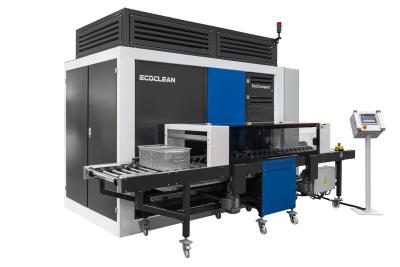
With features such as a large batch capacity, improved washing mechanics and wash fluid reconditioning, as well as energy- optimized system technology with effective heat recovery, the new generation of EcoCcompact machines keeps unit cleaning costs low even when cleanliness requirements are high. The small footprint and flexible changeover between hydrocarbons and modified alcohols also contribute to the excellent economic efficiency and future-proof concept of the compact plug & play cleaning system from Ecoclean.
Ever-stricter demands on component quality and rising product diversity are calling for increasingly complex and versatile solutions in the parts cleaning sector. To keep production competitive, it is also essential to minimize resource consumption and unit cleaning costs while maximizing cleaning performance. The latest generation of the cost-efficient EcoCcompact solvent-based system has been adapted to meet these requirements. Requiring a space of just 3,200 x 1,600 x 2,450 mm (L x W x H), the compact plug & play solution allows you to switch easily between hydrocarbons and modified alcohols (semi-polar solvents) during ongoing operation without any conversion work.
Optimal cleaning results achieved faster and more cost-effectively The machine comes with two or three fully-integrated flood tanks, each fitted with a filtration system in the supply and return lines in the form of bag-type or high-performance filters and bypass filtration. This flexibility enables optimum results to be achieved in short cycles, all the way from pre-cleaning and intermediate cleaning tasks to final cleaning and preservation. On the one hand, the working chamber’s standard diameter of 550 mm results in a batch capacity which is ten percent higher than that of conventional systems in this segment. On the other hand, the high flooding volume means that parts are fully immersed in the wash fluid during the process. In addition, the powerful, frequency-controlled flood pumps not only ensure that the working chamber is filled and emptied quickly; they also achieve a high mechanical cleaning effect during the standard injection flood washing step. This can be further enhanced by integrating an optional, frequency-controlled rotary drive to rotate and position the parts to be cleaned in a specific way.
Besides the high capacity and effective washing mechanism, the EcoCcompact’s energy-optimized system technology makes the machine even more economically efficient. For example, the second and third flood tanks are warmed by heat recovered from the distillation process. Among other things, this has led to a significant reduction in energy consumption. Thanks to the efficient distillation process, the machine also has impressively low solvent requirements. This has been attained by installing the distillation unit in a vertical position, which requires hardly any mounting fixtures.
The design reduces sump formation, prevents dirt build-up and results in an extended bath life. A seven-inch HMI touch panel and self-explanatory pictograms guarantees simple, safe and fast operation. Integrated parts visualization also makes process tracking and maintenance easier and more intuitive. With these features, the EcoCcompact not only meets the requirements of factories with comparatively low production capacities and varying cleaning requirements but also those of large factories with decentralized cleaning stations.
Contact Details
Related Glossary Terms
- recovery
recovery
Reduction or removal of workhardening effects, without motion of large-angle grain boundaries.