Rough turning forgings made of nickel-base superalloys isn’t something that the uninitiated are likely to get into, but Heartland Enterprises Ltd. has extensive experience — and expertise — with the process.
“It’s something we do day in and day out,” said Chris Easterwood, plant manager of the production job shop in Fredericksburg, Texas. “I wouldn’t call it a challenge.”
Being in the heart of Texas enables the company to capture a lot of business from the oil and gas industry, such as machining natural gas compression parts, including piston rods and power cylinder liners, as well as components for powering fluid ends and frack pumps, said President Jay Mallinckrodt. He began that leadership role in summer after Dave Campbell, longtime president, majority owner and his father-in-law, semiretired and became CEO.
The shop also serves the aerospace industry, for which the heat-resistant alloys come into play, including 615 and 725 Inconel, Waspaloy and Hastelloy. The parts involved are primarily large discs and shafts that go into the hot section of commercial jet engines, ranging from 152.4 to 1,066.8 mm (6" to 42") in diameter and up to 1,270 mm (50") long.
“People see the Inconel forgings,” Easterwood said, “and they have never seen Inconel pieces as large as what we’re working on.”
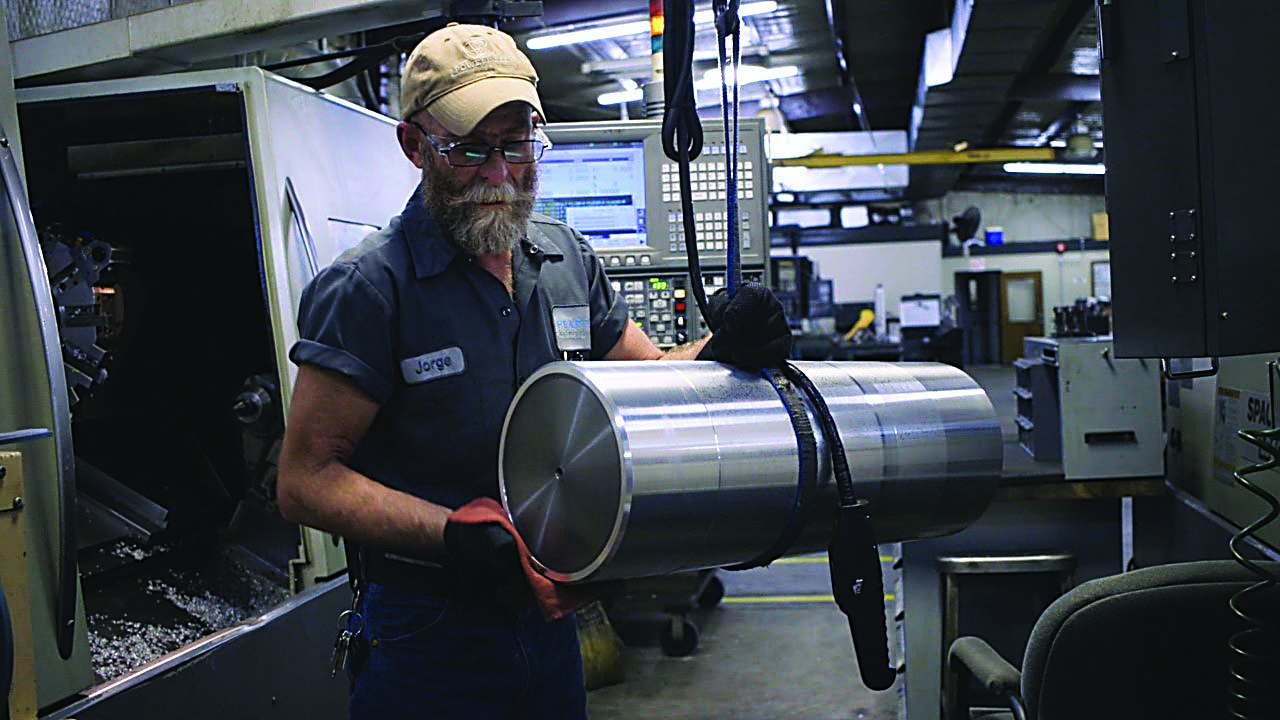
“Our objective is to work with customers long term,” Mallinckrodt said. “We love orders that are 100, 200 pieces, but a lot of work is 10-, 15-, 25-piece jobs. But we want to do those once a month or once a quarter or two or three times a year so we are not doing a lot of reprogramming, setup and design.”
As a result, he said Heartland Enterprises doesn’t take on one-off, short-run jobs.
“You have to do some production work so you can see how to make these parts right,” Mallinckrodt said. “It’s hard to get up to speed making two pieces out of Inconel.”
In the Rough
The company only rough-turns the age-hardened superalloy forgings before sending them to jet engine original equipment manufacturers for finishing in-house or by a subcontractor, Easterwood said. Nonetheless, tolerances can be fairly tight at ±0.0254 mm (±0.001").
He said the process begins by removing the scale on the forgings, an interrupted turning process that breaks down inserts. Round ceramic inserts are the go-to tools because round is the strongest insert shape, but square and 55-degree inserts with four or six nose radiuses also are used, depending on the required part features. The inserts are uncoated.
“We will get the scale off using a slow surface footage, around 180 to 200 sfm (54.9 to 61 m/min.), a 0.1" (2.54 mm) DOC and a 0.01 to 0.012 ipr (0.254 to 0.305 mmpr),” Easterwood said.
He said removing the scale typically requires several passes. In addition, each pass usually doesn’t cover the entire length of a workpiece. For example, the first pass might travel half the length of the part before an insert is indexed and cutting continues.
“It depends on what the forging looks like, how clean it is and everything like that,” Easterwood said. “Once the scale is off, it’s a lot easier cutting, with no interrupted cuts.”
With the scale removed, he said Heartland Enterprises turns superalloys at a vigorous but slow cut to prevent the cutting tool from pushing off the material and to correctly produce the part dimensionally.
“We try to be pretty aggressive with the time,” Easterwood said.
Even with the assertive approach, Mallinckrodt said the company rarely scraps the pricey workpiece material.
“We’ve been machining these parts for 20 years now,” he said. “It’s almost like second nature to us how we do it. Someone coming into this cold would be like, ‘I’m not touching that stuff.’ It’s hard, and coming out of the forge, it’s a little bit nasty.”
Cycle time varies widely, depending on part size and the number of required operations.
“There are some smaller tubes that we can get 50 parts a shift,” Mallinckrodt said. “There are also some big shafts and discs where an operator may only get one or two parts a day. We might do one part with one or two operations, and another may take six operations.”
Overcoming Issues
Because nickel-base superalloys tend to workharden, turning parameters must be controlled carefully to prevent too much heat from entering a workpiece and damaging the tool, Easterwood said.
In addition, workhardening causes the tool to be pushed off the workpiece. For example, push-off might cause a 152.4-mm-dia. workpiece to measure 152.91 mm (6.02"). In that scenario, he said the tool should not be offset 0.51 mm (0.02"), because the part will be turned to its specified dimension when the tool is run at the correct speed and feed.
Heartland Enterprises also applies a semisynthetic coolant to help remove heat.
“I know some people don’t like putting coolant on ceramic,” Easterwood said, “but we put coolant pretty much on all the ceramics.”
Warping also can be a problem when turning these heat-resistant metals. To prevent warping, he said that after the first operation the shop leaves a small amount of material, such as 2.54 mm, for removal during one or more subsequent operations.
Machine Matters
Heartland Enterprises has more than 20 horizontal turning centers, vertical turning lathes and multifunctional horizontal lathes in its equipment lineup, and all are from Okuma America Corp.
“They are very rigid and reliable,” Easterwood said, adding that some machines are older than a decade. “For the amount that we have run them, day in and day out, they are very reliable and hold tolerances, especially roughing all that forging off. It is tough on the machine with the interrupted cutting and the load that you put on the machine.”
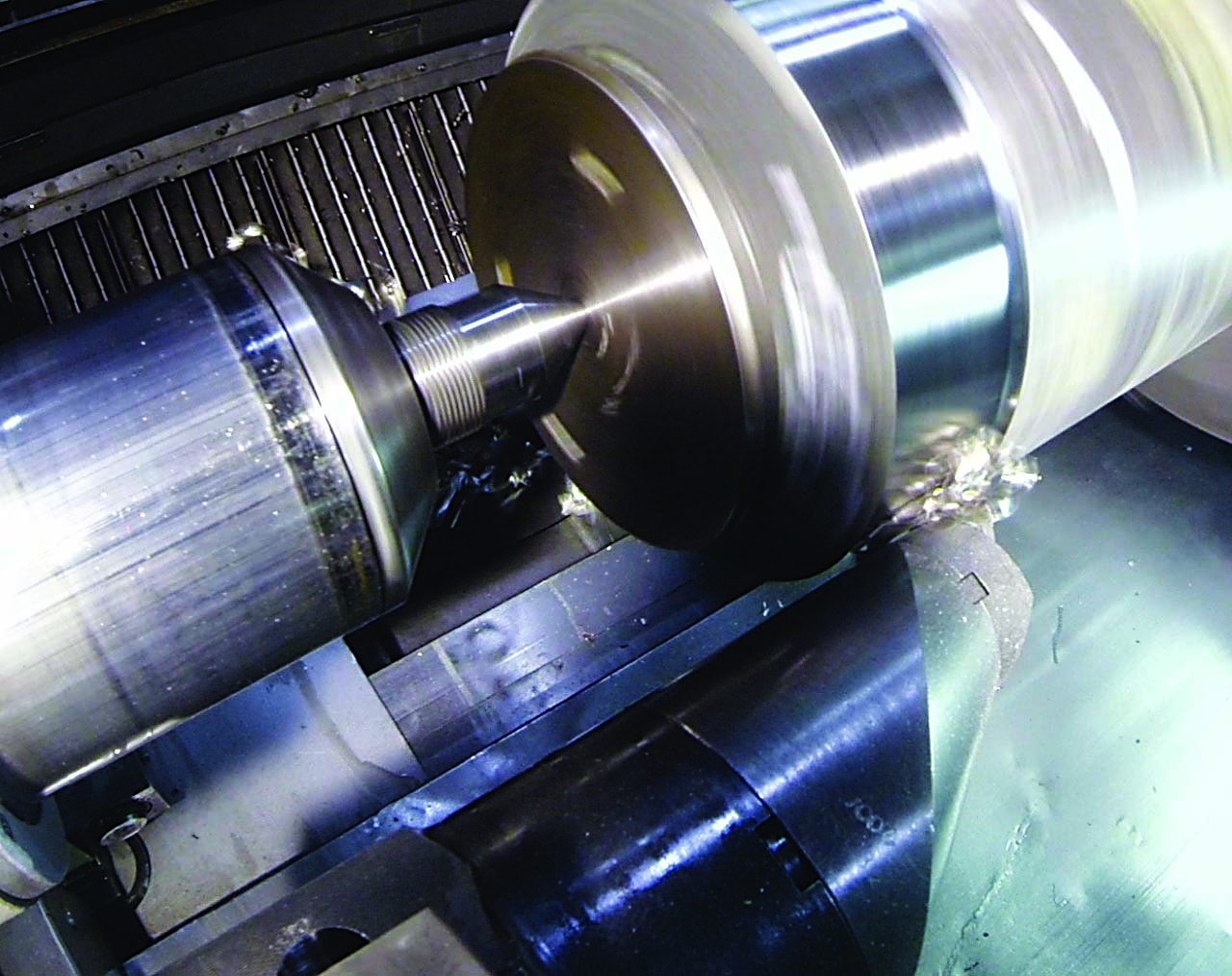
When a part measures more than 609.6 mm (24") in diameter, he said the part generally goes on one of the company’s two Okuma 1SP-V100R vertical turning lathes, which can manage parts up to 1,066.8 mm in diameter and up to 609.6 mm long.
“Our horizontal lathes are 24" chucks and can turn lengths up to 64" (1,625.6 mm),” Easterwood said.
Mallinckrodt said having turning equipment from only one builder means that controls are similar throughout the facility.
“Our guys can move from machine to machine,” he said, “and it’s relatively seamless operating each piece of equipment because it’s got the same control.”
Mallinckrodt said the dual spindle on the Okuma Multus U4000 multitasker — Heartland Enterprises’ newest machine — enables the company to reduce the amount of work in progress and enhance repeatability. However, the shop doesn’t perform milling work on superalloys.
The organization purchases Okuma machines from Hartwig Inc. in Houston.
“We get top-notch support from them,” Mallinckrodt said, “and that’s critical to our success to have them close and able to respond to our needs.”
Heartland Enterprises arranges its machines into work cells, enabling one person to operate two machines. He said the cellular configuration is especially beneficial when turning large discs on the vertical turning lathes, which frequently require two operations.
“We run the first one and then flip it into the next machine,” Mallinckrodt said, “and the operator can efficiently run two machines.”
Managing Chips
Because nickel-base superalloys are a relatively expensive class of materials, Mallinckrodt pointed out that it’s important to keep chips from each alloy separated.
“You want to keep this material segregated for the recycling process to get top dollar for your chips,” he said.
Mallinckrodt said the segregation process requires cleaning chips from the machine, hopper and conveyors before turning the next material. The chips are dumped into a cardboard baler for the customer to collect.
“When we’re blowing and going and busting at the seams on our storage,” he said, “they’ll come with a truck and trailer and take them back to their reprocessing facility to recycle them back into their parts.”
Mallinckrodt said machine operators are trained to manage the different materials.
“It’s an ongoing process to make sure everyone understands that it’s got to be segregated,” he said.
After parts are machined, Heartland Enterprises packs them as efficiently as possible to meet customer specifications, Mallinckrodt stated in a company blog post.
“We ensure that each box/crate is sturdy and durable with cardboard protection inside to ensure parts do not come in contact with each other during transit,” he wrote. “Heartland has a full woodshop that enables us to produce custom packaging for the secure transit of diverse sized parts.”
For more information about Heartland Enterprises, call 830-997-9434 or visit www.heartlandmachining.com.
Related Glossary Terms
- alloys
alloys
Substances having metallic properties and being composed of two or more chemical elements of which at least one is a metal.
- centers
centers
Cone-shaped pins that support a workpiece by one or two ends during machining. The centers fit into holes drilled in the workpiece ends. Centers that turn with the workpiece are called “live” centers; those that do not are called “dead” centers.
- ceramics
ceramics
Cutting tool materials based on aluminum oxide and silicon nitride. Ceramic tools can withstand higher cutting speeds than cemented carbide tools when machining hardened steels, cast irons and high-temperature alloys.
- coolant
coolant
Fluid that reduces temperature buildup at the tool/workpiece interface during machining. Normally takes the form of a liquid such as soluble or chemical mixtures (semisynthetic, synthetic) but can be pressurized air or other gas. Because of water’s ability to absorb great quantities of heat, it is widely used as a coolant and vehicle for various cutting compounds, with the water-to-compound ratio varying with the machining task. See cutting fluid; semisynthetic cutting fluid; soluble-oil cutting fluid; synthetic cutting fluid.
- feed
feed
Rate of change of position of the tool as a whole, relative to the workpiece while cutting.
- gang cutting ( milling)
gang cutting ( milling)
Machining with several cutters mounted on a single arbor, generally for simultaneous cutting.
- milling
milling
Machining operation in which metal or other material is removed by applying power to a rotating cutter. In vertical milling, the cutting tool is mounted vertically on the spindle. In horizontal milling, the cutting tool is mounted horizontally, either directly on the spindle or on an arbor. Horizontal milling is further broken down into conventional milling, where the cutter rotates opposite the direction of feed, or “up” into the workpiece; and climb milling, where the cutter rotates in the direction of feed, or “down” into the workpiece. Milling operations include plane or surface milling, endmilling, facemilling, angle milling, form milling and profiling.
- superalloys
superalloys
Tough, difficult-to-machine alloys; includes Hastelloy, Inconel and Monel. Many are nickel-base metals.
- turning
turning
Workpiece is held in a chuck, mounted on a face plate or secured between centers and rotated while a cutting tool, normally a single-point tool, is fed into it along its periphery or across its end or face. Takes the form of straight turning (cutting along the periphery of the workpiece); taper turning (creating a taper); step turning (turning different-size diameters on the same work); chamfering (beveling an edge or shoulder); facing (cutting on an end); turning threads (usually external but can be internal); roughing (high-volume metal removal); and finishing (final light cuts). Performed on lathes, turning centers, chucking machines, automatic screw machines and similar machines.
- workhardening
workhardening
Tendency of all metals to become harder when they are machined or subjected to other stresses and strains. This trait is particularly pronounced in soft, low-carbon steel or alloys containing nickel and manganese—nonmagnetic stainless steel, high-manganese steel and the superalloys Inconel and Monel.