Electrical discharge machine automation is certainly nothing new, but a machine’s control is critical to enabling unattended burning. For example, John Bradford, turnkey and automation applications team manager for Mason, Ohio-headquartered Makino Inc., recalled how he was able to comfortably walk away from a running LeBlond Makino sinker EDM with an eight-station automatic toolchanger that he operated as far back as 1987.
“The technology that facilitated allowing me to run that machine unattended was the machine’s ability to adapt to the spark gap and the stability of the cut,” he said. “From the premise that you have a robust, effective adaptive control system, especially on a sinker EDM, that really is the foundation piece to allow the machine to run without an operator and without any side-assisted flushing. The machine has to be able to take care of itself in an unmanned state.”
Bradford said over more than several decades, the machine tool builder has enhanced EDM automation to store significantly larger quantities of electrodes, increase equipment utilization from between 60% and 70% to upward of 90% and extend lights-out machining.
“Now you’re talking five, six, seven, 10 days of unattended operation,” he said.
Bradford said the most commonly integrated automation platforms are off-the-shelf pallet systems from Erowa Technology Inc. and System 3R USA Inc. to complement Makino’s EDMs.
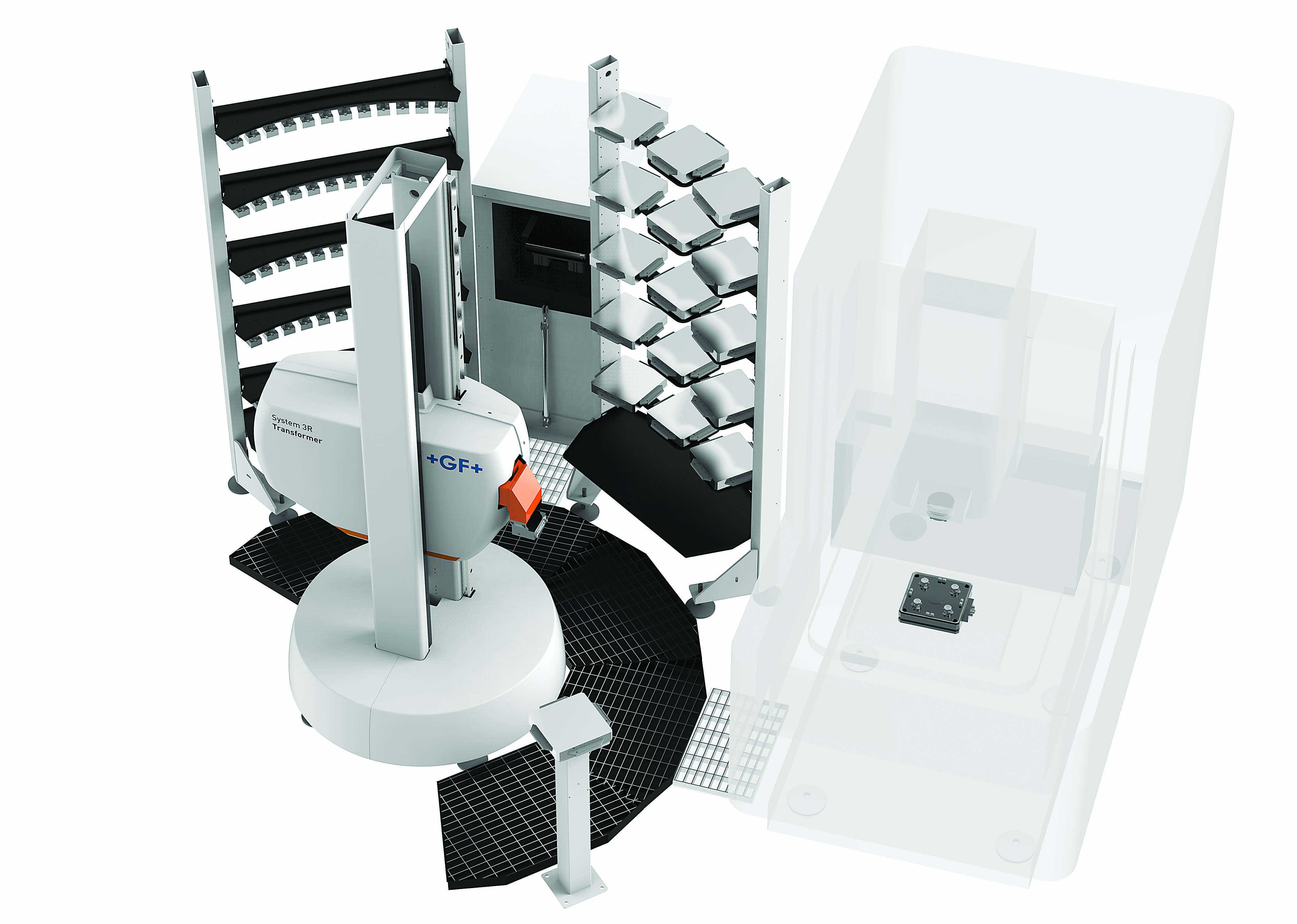
An automatic toolchanger certainly counts as a piece of automation equipment, but the device has become so ubiquitous that end users’ perception changed.
“People don’t consider it automation anymore, but when it started out people thought it was brilliant,” said Dan Zeman, automation product manager for MC Machinery Systems Inc. in Elk Grove Village, Illinois.
However, some also found the technology threatening.
“When I started out in 1985,” Zeman said, “operators were worried about toolchangers.”
Operators of manual sinker EDMs considered it their job to change electrodes and perform all the needed tasks to properly set up and position the machines, he said, adding that burning a cavity sometimes required eight to 10 electrodes. So in addition to developing productivity-boosting automation equipment, machine builders changed the generator design to lower electrode wear and reduce the number needed.
A Slow Go
Because sinker EDMing is not a fast machining process compared with milling or turning, for instance, Zeman said an EDM generally is considered a last resort for production applications. However, he said EDM automation frequently can be found in the tool, die and mold arena.
“If you go to a mold shop,” he said, “you may see a robot between two sinkers or even between a graphite milling center and a sinker EDM. What they’re trying to do in their EDM department is cut out the dead time.”
A sinker EDM’s relatively long unattended burn times typically hinder one from being added to an automation cell with milling machines with shorter cycle times to avoid creating a bottleneck, said Eric Ostini, head of business development for North America at GF Machining Solutions LLC in Lincolnshire, Illinois. Therefore, EDMs are kept in their own automation cell, maybe with a milling machine to produce electrodes, but a separate cell produces the parts.
“So there is no bottleneck going on due to the EDM process,” he said.
Bradford said there are two factors to consider for EDM automation. The first is the size and extent of the part handling system, and the second is the unmanned runtime after a part is set up. For workpieces that measure 508 mm × 508 mm (20"×20") or larger, it’s uncommon to automate the loading and unloading of those parts.
“When we are in that scenario, what’s most common is the fact that the customer will automate the electrode loading to the spindle chuck but will not automate the loading and unloading of the workpiece,” he said, adding that it is typical to shuttle both smaller workpieces and the electrode in the automation system.
Bradford said a shop also must examine its ratio of setup time relative to the unattended runtime.
“For example,” he said, “if you place a part on a table and the part takes 20 to 30 minutes to set up/locate with (the) machine and then you are able to get 12, 15, 20, 24 hours of unmanned runtime just on that single workpiece, the benefit for the cost in return value by trying to automate the loading and unloading of that workpiece generally does not pan out.”
Down to the Wire
For the three main types of EDMs — sinker, wire and hole popper — Ostini said wire EDMs tend to be added to automation cells more than the others. One reason is that hard die milling has replaced many sinker applications, though a sinker is required to produce some part features, such as a sharp corner, and other applications.
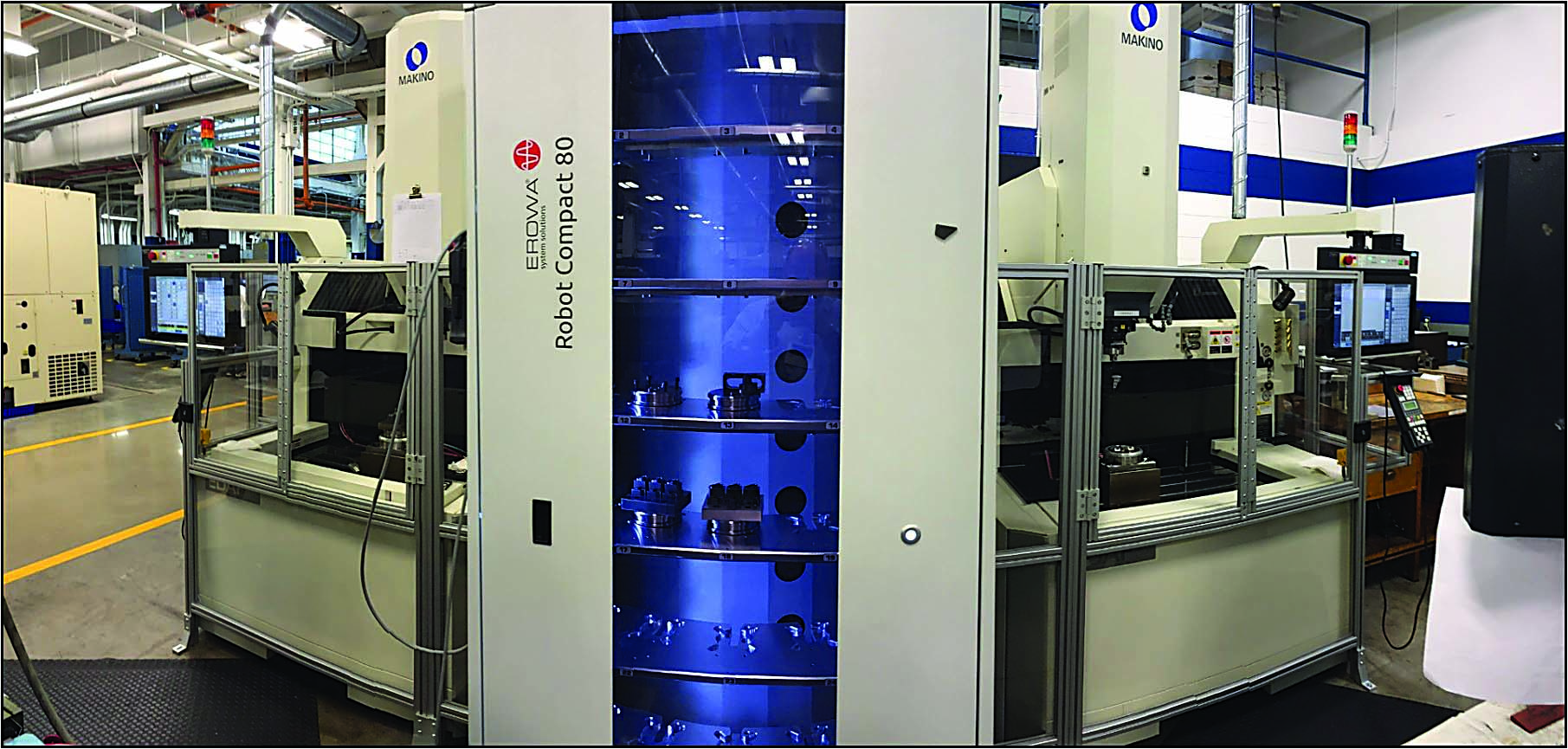
GF Machining Solutions offers a variety of automation options for wire EDMs, like the Cut P 550 Pro. The company reports that automation options include automatic slug management; automatic slug welding; a WorkPartner 1+, which is a compact robot from System 3R; and a retractable Renishaw touch probe to measure workpiece planarity and position on the machine’s worktable.
With automatic slug management, Ostini said while a lower arm remains stationary, an upper arm places a magnet over the slug and slowly moves down in the z-axis, grabs the slug and drops it into a basket.
“ASM has the ability to remove slugs in a lights-out scenario,” he said. “Of course, the slugs can’t be too small or weigh too much.”
Ideally, a slug would be bigger than 12.7 mm × 12.7 mm (0.5"×0.5") and weigh no more than 0.32 kg (0.7 lb.).
For heavier slugs, Ostini said GF Machining Solutions offers automatic slug welding to weld a slug in place so it doesn’t fall after a part is cut.
“With that type of automation,” he said, “you could use a robot, which takes the slug-welded part out of the machine and over to a station where a hammer taps out those slugs from the workpiece and then puts it back into the wire EDM to finish each cavity to size.”
The WorkPartner 1+ robot connects to one milling machine, one wire EDM or one sinker EDM with the option to connect to two machines.
“You usually see a die sinker and milling machine that is producing the electrodes,” Ostini said about the automated cell arrangement.
To connect to three machines, he said GF Machining Solutions provides System 3R’s Transformer three-axis robot. By adding a track for the robot, it can feed up to 12 machines.
“Instead of throwing away the robot because you want to hook up more machines, the robot is already invested,” Ostini said. “The robot can transform from a stationary robot feeding three machines to a track robot feeding up to 12 machines.”
He said those machines might include one for parts cleaning or a coordinate measuring machine.
With a CMM in a cell, Zeman said a part can be put automatically into the CMM to qualify the part and send the workpiece to the next process or to intervene if something is off.
“Everyone is working off of what we call ‘the numbers,’ so you are not having operators going in and measuring the setup,” he said. “That downtime of measuring and setting up work is done externally, and everything is being transferred automatically.”
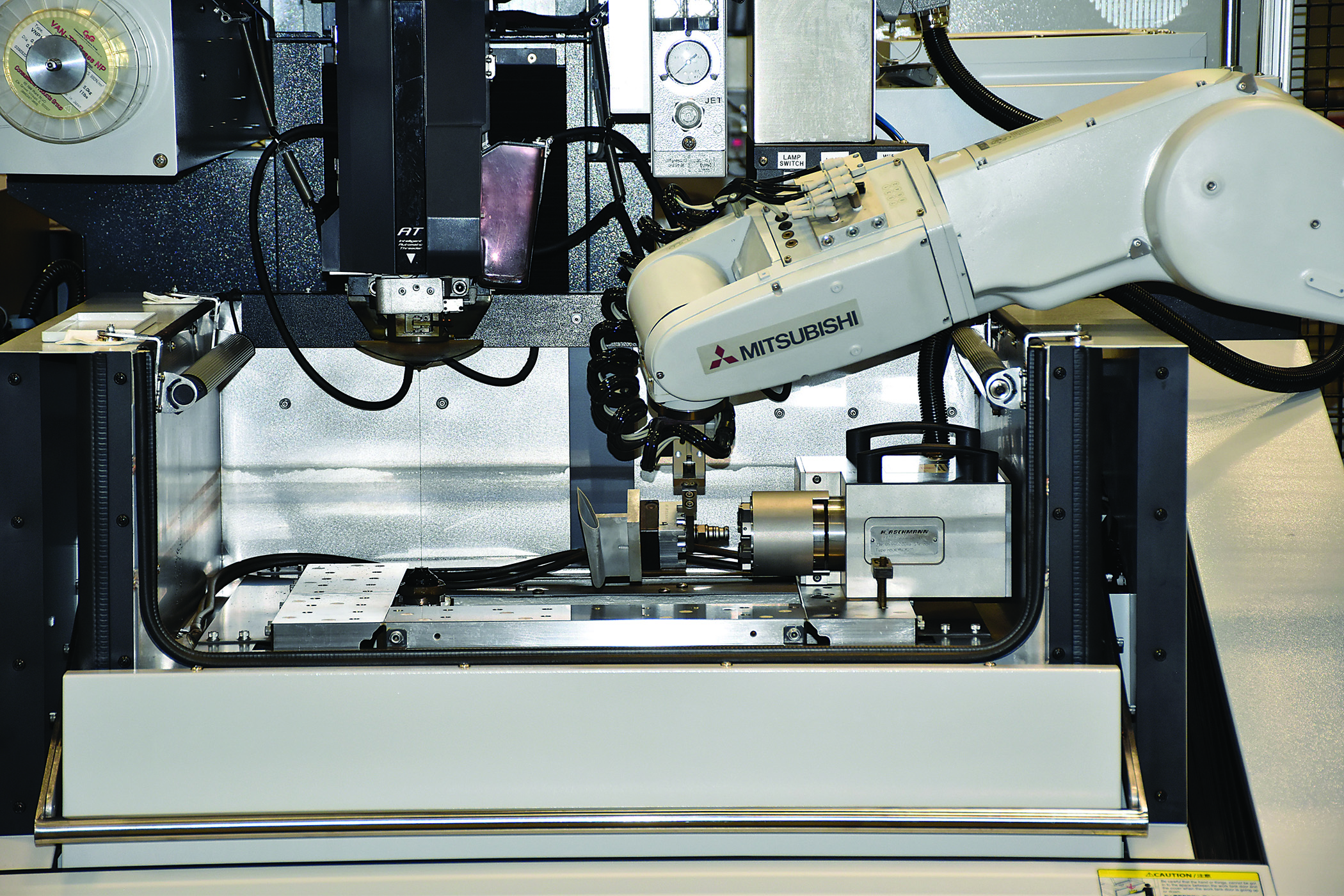
Without a CMM in a cell, an end user might opt for an in-machine mechanical touch probe. While that has long been available on GF Machining Solutions’ sinker side, Ostini said it recently was added as an option for a wire EDM to check a part both before cutting it to determine that it is within the specification and then after machining to verify size ahead of removing it from the machine.
In contrast, Bradford said Makino doesn’t have any customers that inspect parts and then possibly re-machine them in an automated state.
“Not from a die/mold perspective,” he said about the shops that are the biggest consumers of EDM automation. “That operation is not only quite expensive — it also requires a bit of inside knowledge for all of your contributing processes to understand which one you want to change and by what percentage.”
Motivating Factors
EDM automation can boost throughput and improve part quality, but those are not the primary reasons for integrating robots, pallet changers and other automation equipment into an EDM operation. Bradford said a large majority of part manufacturers do it to minimize labor costs, allowing workers to perform different tasks in different work environments instead of tending a machine.
He said an EDM with a stable, robust adaptive control is the simplest, easiest and least expensive machine to automate at a tool, mold or die shop.
“To have that sinker EDM tended by a pallet changer is a no-brainer,” Bradford said. “It’s very stable and predictable without an operator for days at a time as long as you can feed it the work.”
With the ongoing shortage of skilled labor, Ostini said shops are inclined to gravitate to automation. Rather than reducing the size of the workforce, automation makes a positive change to the way that people work.
“The people in the shop who start to see automation coming in because of the skilled labor shortage are increasing the amount of work they are doing instead of decreasing the amount,” he said.
Zeman concurred that EDM automation, especially for tool, die and mold building, is not necessarily always going to eliminate workers.
“Automation does, however, make a mold builder a lot more productive,” he said. “Automation allows a mold or tool builder to take advantage of the automated processes and get the work done quicker. This allows for much higher throughput and faster deliveries.”
Zeman used the analogy of a big printer for how a shop should be coordinated to automatically build a mold instead of having many people manually managing the process and communicating back and forth.
“You have an engineer who is designing a mold,” he said, “and theoretically you hit the build-the-mold button, and it goes through this whole process in the cell, and within a shorter amount of time the mold is assembled, tested and on the loading dock. This is what they’re ultimately trying to do at a lot of mold and die building shops — have the work flow automatically.”
Zeman described the process as “not a black art anymore.”
“Everything has to be off the numbers,” he said. “I really haven’t seen anything outside of rework that I would say you couldn’t (automate).”
Nonetheless, there’s both an easier and a harder way to go about it.
Ostini said a process first must be “nailed down” before it’s duplicated with a robot.
“Customers who say, ‘I want to go to automation and hook up these nine machines, and then I’ll figure it out,’ have a much harder time of setting up and (getting) going with the automation than a person who starts out small, defines his process and then adds the robot later on,” he said.
Bradford said effective implementation of EDM automation requires managing the upstream processes and bringing all the physical parts and the digital process data together to the EDM to make the finished product.
“Your thinking, planning and standardization of all those steps have to be very clean and consistent to end up with a successful die/mold part coming out of the sinker EDM,” he said. “It’s much more sophisticated than just shuttling an electrode to the spindle chuck.”
For more information about EDM automation from Makino and MC Machinery Systems, view a video presentation here: cteplus.delivr.com/2tfus
Contact Details
Contact Details
Contact Details
Related Glossary Terms
- automatic toolchanger
automatic toolchanger
Mechanism typically included in a machining center that, on the appropriate command, removes one cutting tool from the spindle nose and replaces it with another. The changer restores the used tool to the magazine and selects and withdraws the next desired tool from the storage magazine. The changer is controlled by a set of prerecorded/predetermined instructions associated with the part(s) to be produced.
- burning
burning
Rotary tool that removes hard or soft materials similar to a rotary file. A bur’s teeth, or flutes, have a negative rake.
- chuck
chuck
Workholding device that affixes to a mill, lathe or drill-press spindle. It holds a tool or workpiece by one end, allowing it to be rotated. May also be fitted to the machine table to hold a workpiece. Two or more adjustable jaws actually hold the tool or part. May be actuated manually, pneumatically, hydraulically or electrically. See collet.
- electrical-discharge machining ( EDM)
electrical-discharge machining ( EDM)
Process that vaporizes conductive materials by controlled application of pulsed electrical current that flows between a workpiece and electrode (tool) in a dielectric fluid. Permits machining shapes to tight accuracies without the internal stresses conventional machining often generates. Useful in diemaking.
- feed
feed
Rate of change of position of the tool as a whole, relative to the workpiece while cutting.
- gang cutting ( milling)
gang cutting ( milling)
Machining with several cutters mounted on a single arbor, generally for simultaneous cutting.
- milling
milling
Machining operation in which metal or other material is removed by applying power to a rotating cutter. In vertical milling, the cutting tool is mounted vertically on the spindle. In horizontal milling, the cutting tool is mounted horizontally, either directly on the spindle or on an arbor. Horizontal milling is further broken down into conventional milling, where the cutter rotates opposite the direction of feed, or “up” into the workpiece; and climb milling, where the cutter rotates in the direction of feed, or “down” into the workpiece. Milling operations include plane or surface milling, endmilling, facemilling, angle milling, form milling and profiling.
- milling machine ( mill)
milling machine ( mill)
Runs endmills and arbor-mounted milling cutters. Features include a head with a spindle that drives the cutters; a column, knee and table that provide motion in the three Cartesian axes; and a base that supports the components and houses the cutting-fluid pump and reservoir. The work is mounted on the table and fed into the rotating cutter or endmill to accomplish the milling steps; vertical milling machines also feed endmills into the work by means of a spindle-mounted quill. Models range from small manual machines to big bed-type and duplex mills. All take one of three basic forms: vertical, horizontal or convertible horizontal/vertical. Vertical machines may be knee-type (the table is mounted on a knee that can be elevated) or bed-type (the table is securely supported and only moves horizontally). In general, horizontal machines are bigger and more powerful, while vertical machines are lighter but more versatile and easier to set up and operate.
- toolchanger
toolchanger
Carriage or drum attached to a machining center that holds tools until needed; when a tool is needed, the toolchanger inserts the tool into the machine spindle. See automatic toolchanger.
- turning
turning
Workpiece is held in a chuck, mounted on a face plate or secured between centers and rotated while a cutting tool, normally a single-point tool, is fed into it along its periphery or across its end or face. Takes the form of straight turning (cutting along the periphery of the workpiece); taper turning (creating a taper); step turning (turning different-size diameters on the same work); chamfering (beveling an edge or shoulder); facing (cutting on an end); turning threads (usually external but can be internal); roughing (high-volume metal removal); and finishing (final light cuts). Performed on lathes, turning centers, chucking machines, automatic screw machines and similar machines.
- wire EDM
wire EDM
Process similar to ram electrical-discharge machining except a small-diameter copper or brass wire is used as a traveling electrode. Usually used in conjunction with a CNC and only works when a part is to be cut completely through. A common analogy is wire electrical-discharge machining is like an ultraprecise, electrical, contour-sawing operation.
Contributors
GF Machining Solutions LLC
800-282-1336
www.gfms.com
Makino Inc.
513-573-7200
www.makino.com
MC Machinery Systems Inc.
630-860-4210
www.mcmachinery.com