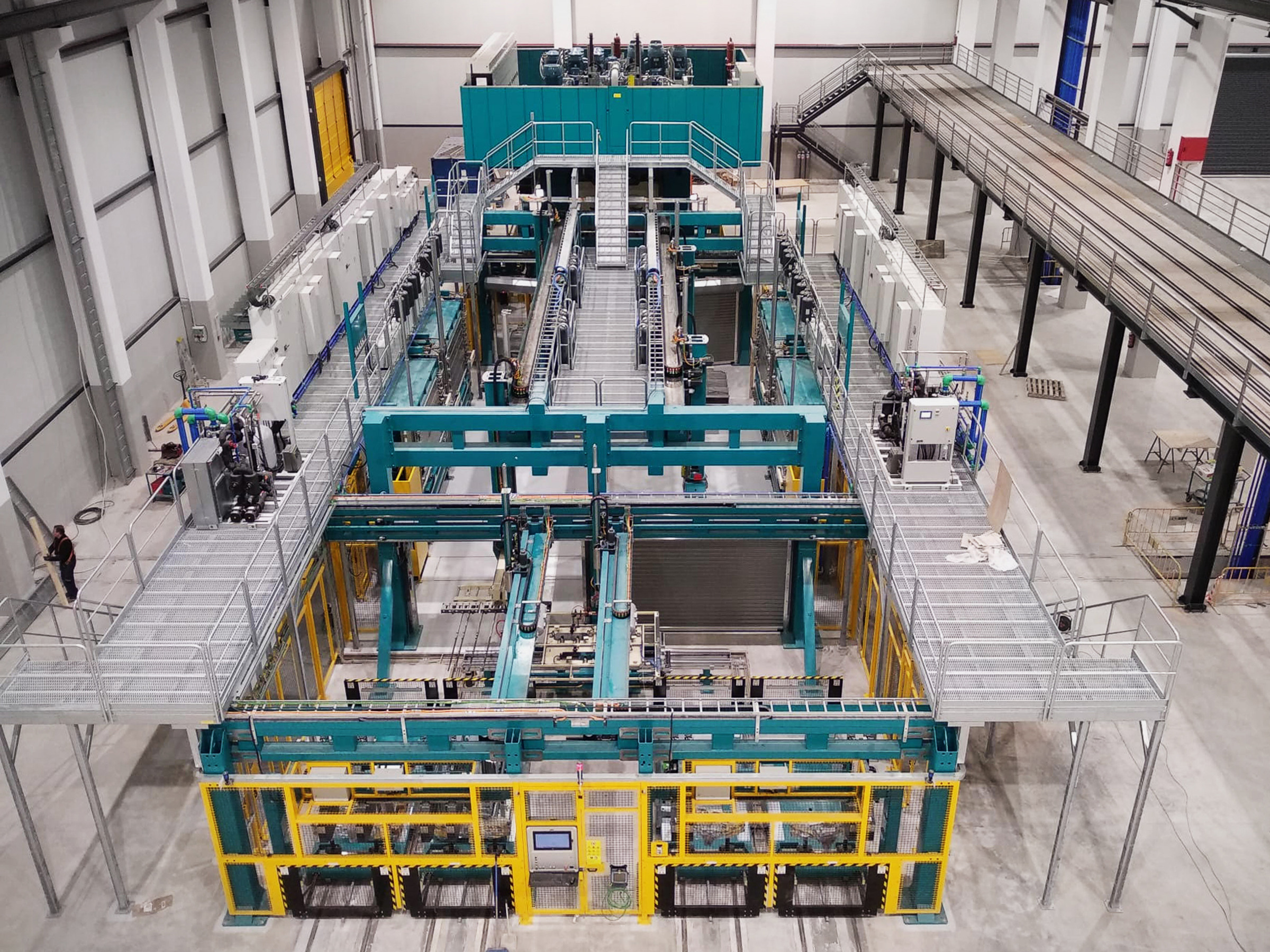
AP&T, a provider of high-performing production solutions for the sheet metal forming industry, has developed a press-hardening production solution that it says lays the groundwork for providing car manufacturers with lighter, safer, more flexible designs that are cost and energy efficient.
The solution includes AP&T's servohydraulic press, boasting up to 70% lower energy consumption than conventional hydraulic presses, and TemperBox, which enables soft and hard zones to be combined in the same finished component, according to the company.
The first commercial production line containing both innovations became operational at GEDIA in Germany in the fall of 2019. The same equipment was also later installed at the company’s facilities in Spain and the US.
GEDIA, with its headquarters in Attendorn, Germany, has been manufacturing pressed sheet metal parts for the automotive industry since the mid-1950s. In 2005, the company began to take a serious interest in the opportunities the press-hardening technology offers for manufacturing structural parts that combine strength and low weight – attributes that have made it possible for car manufacturers to improve collision safety while reducing energy consumption and climate-impacting emissions. To sound out the market, they contacted AP&T, an early leader in developing production lines for press hardening.
In 2012, the two companies began to work together to ramp up their working relationship.
Order for three complete lines
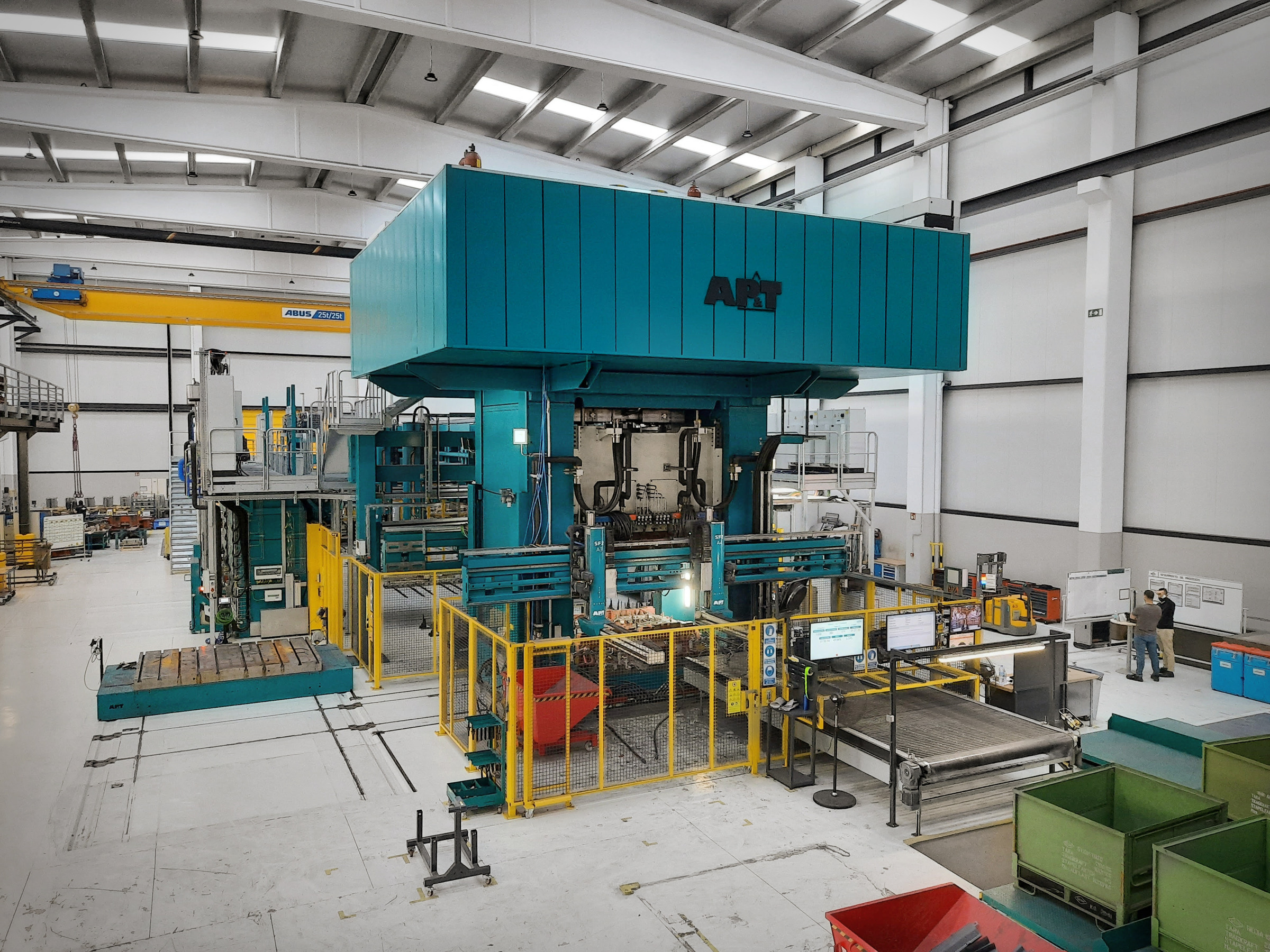
“It was our impression that GEDIA was interested in potentially investing in their first press-hardening line. When the meeting was over, we had an order for three complete lines, which was naturally a positive surprise,” said AP&T's Michael Hunger, director and head of sales and marketing Europe and key account manager for GEDIA.
The three lines became operational between 2014 and 2016; one in Attendorn and two in the company’s production facility in Nowa Sol, Poland.
“It was a technically challenging project that provided useful experiences and sparked the motivation to continue developing and testing new press-hardening technology together,” said Hunger.
Burkhard Vogt, GEDIA’s group director of engineering, agreed. “It was an exciting project. We resolved the challenges together and managed to get really good results. We also developed and deepened our collaborative relationship, got closer, and established new, useful contacts in different parts of the companies,” he said.
Industrialization of TemperBox for partial press hardening
In 2014, GEDIA was looking for a partner to help commercialize and industrialize a new partial press-hardening innovation, TemperBox, at that point a prototype, and once again turned to AP&T.
To become a commercial product, the technology needed to be tested in industrial conditions. Following initial testing by AP&T, the company built a try-out line with an integrated TemperBox for small-scale testing and manufacturing in Attendorn. The results proved promising.
When GEDIA received an order for partially press-hardened parts for one of Germany’s major car manufacturers, they needed a new industry-scale line for serial manufacturing. It was the start of a highly interesting project that would push the limits of press-hardening technology.
“Thanks to the successful process and product development, we decided to design a line for mass-manufacturing using TemperBox as an integral part of the equipment. It was a prerequisite that production would continue without extending cycle times,” said Vogt.
Stephan Gante, GEDIA’s group director of the machine and building management, was responsible for purchasing the new line and as such, was also responsible for the detailed requirement specification.
“Not only did we need to be able to produce a great number of components per hour, but we also needed to install the line in the limited space of our existing premises. The equipment also needed to be reliable and simple to maintain. It was also of great importance that the solution is energy efficient with a low electricity consumption per produced unit,” he said.
Jörgen Theander, AP&T's person responsible for the project, said “We started planning the new line in August of 2018 and set the target to have it operational by January 1, 2020.”
Two innovations, one line
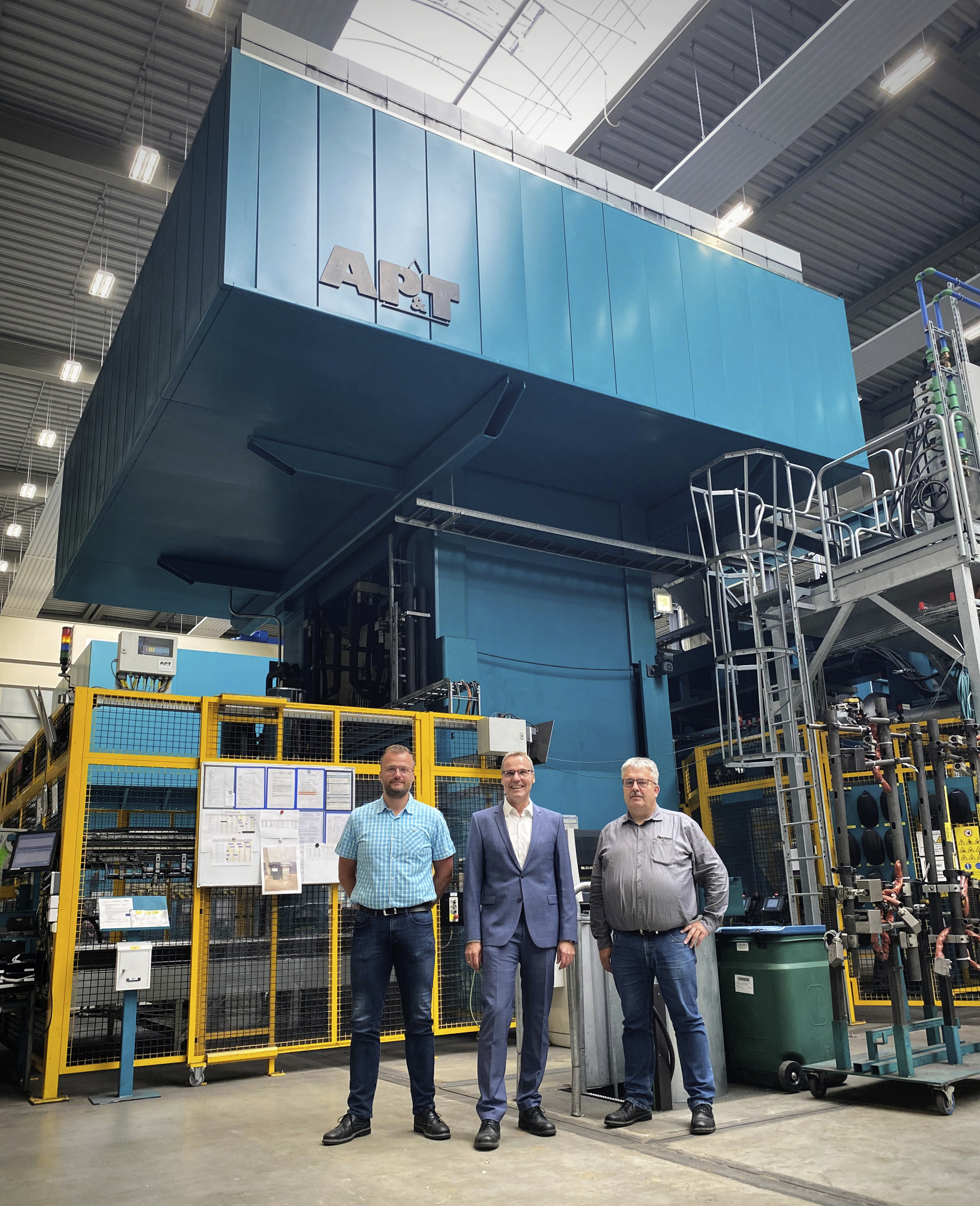
The greatest technological challenge was uniting two innovations – AP&T's servohydraulic press and TemperBox – into the same line for a process that had never before been used commercially. Organizationally, it was a challenge to put together a dedicated project team with just the right expertise, not to mention the right attitude toward the project. During recruitment, experience in the automotive industry was a must, as were excellent cooperation and listening skills.
“It was crucial that everyone, from the project team to R&D, really understood the expectations our customer and their customers had on the line. The goal was to manufacture on industrial scale products with tailored, repeatable attributes with short cycle times, high availability, and optimized energy consumption. That was what we were striving for,” said Theander.
To improve efficiency, GEDIA also put together a project team with the corresponding expertise under the lead of Björn Müller, who both participated in the installation of the lines in Nowa Sol and was responsible for the work on the try-out line in Attendorn.
“I already had positive experiences working with AP&T, and these were confirmed when we now embarked on a new project together. During this journey, we developed a close relationship based on trust, which meant we could solve our tasks very smoothly. Nothing was left to chance,” said Björn Müller.
Jörgen Theander highlights the importance of close cooperation as well. “Throughout the project, we worked closely together and spoke regularly, oftentimes in person at GEDIA in Germany. Doing so made it easier to catch problems and tackle challenges efficiently. We worked together like one big, close team, all striving for the same target,” he said.
The project's starting point was the documentation from the existing production lines and the try-out line installed in Attendorn. Questions such as what proven design solutions could be used in the new line, what needed to be improved, and what would be replaced by the new technology were asked. Using this analysis, a requirement specification was made and efforts to realize the new line could be started in earnest. In the fall of 2019, it was installed and commissioned in the Attendorn production facility.
“Since it was the first commercial press-hardening line of its kind, it was important to maintain a presence for some time to ensure that it was functioning properly, tweak the equipment and be able to rectify any problems that might arise,” said Theander.
Even before the first line was completely installed, AP&T received an order for an identical line for GEDIA’s Spanish production facility outside Barcelona.
“We were able to draw on our experiences from the first line from the very beginning of working on the second. So just 17 months later, we were able to deliver a solution optimized for the Spanish facility together with GEDIA's German organization.”
In January of 2020, GEDIA ordered a third production line of this type. This time, it was for their Dalton, Georgia, factory in the US and was to be installed in the fall of 2021.
More efficient
The new lines are considerably more energy efficient, much because the servohydraulic press consumes up to 70% less energy than conventional hydraulic presses. The latest generation of multi-layer furnaces, consuming 40% less energy than its predecessors, also makes an important contribution.
In addition, the new lines make it possible to shorten the manufacturing cycle times of certain products by up to 20%, freeing up time for more production.
In the design process, increased availability and a reduced need for maintenance were in focus. Here, the multi-layer furnaces have posed several challenges, which the teams resolved together. Now, the collaboration will continue in an attempt to significantly increase annual production hours.
“We have also developed our method of verifying the CQI-9 process repeatability of the furnaces so that it goes significantly faster than before. This makes room for more valuable production time,” said Theander.
For Gante, the original requirement specification has been practically applied three times over. “We now have a user-friendly, space-efficient solution with a high degree of process reliability and excellent energy efficiency. Aside from TemperBox itself, AP&T’s servohydraulic press, with its considerably lower cooling requirements and energy consumption per stroke compared to conventional hydraulic presses, plays a central role in the result. We are very satisfied,” he said.
Contact Details
Related Glossary Terms
- hardening
hardening
Process of increasing the surface hardness of a part. It is accomplished by heating a piece of steel to a temperature within or above its critical range and then cooling (or quenching) it rapidly. In any heat-treatment operation, the rate of heating is important. Heat flows from the exterior to the interior of steel at a definite rate. If the steel is heated too quickly, the outside becomes hotter than the inside and the desired uniform structure cannot be obtained. If a piece is irregular in shape, a slow heating rate is essential to prevent warping and cracking. The heavier the section, the longer the heating time must be to achieve uniform results. Even after the correct temperature has been reached, the piece should be held at the temperature for a sufficient period of time to permit its thickest section to attain a uniform temperature. See workhardening.