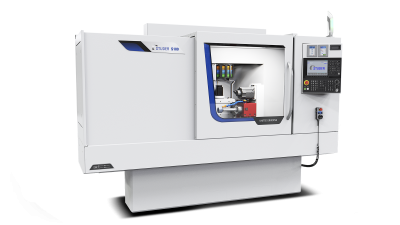
STUDER, a brand of UNITED GRINDING, presents the new S100. This high-precision, flexible and reliable universal internal cylindrical grinding machine is ideal for the entry-level market. Its excellent price-performance ratio makes it perfect for a wide range of internal grinding applications. “The S100 perfectly complements our comprehensive internal grinding portfolio”, explained STUDER CSO Sandro Bottazzo when presenting the S100 at the BI-MU Exhibition in Milan.
Like all STUDER cylindrical grinding machines, the S100 has a machine bed made of Granitan®. The outstanding dampening and thermal characteristics of this material ensure consistently good grinding results and help provide the renowned STUDER precision. During the development process, special attention was given to designing components that are uncomplicated and efficient, making operation and maintenance easy for the operator. Despite this straightforward construction, the features built into the S100 make it suitable for grinding geometrically defined basic forms and contours for a wide range of parts, all of which can be generated with the machine’s interpolating axes.
The S100 can be configured to meet each customer’s individual needs. It can be equipped with up to two internal grinding spindles, or one internal and one external spindle. In addition to a fixed wheelhead, it can be supplied with a manual wheelhead and a 2.5 degree Hirth coupling. The optimal combination consists of an automatic wheelhead with a 1 degree Hirth. A synchronous motor drives the grease-lubricated internal and external belt spindles. The machine is operated by the FANUC 0i-TF PLUS controller, together with the proven STUDER operating system.
A further advantage of the S100 is the available automation equipment options. The machine can be ordered with a loading interface and an automatic sliding door, enabling automatic operation for large production runs.
Typical workpieces for production on the S100 include collets for toolmaking, bearing rings, ball bearings and cylinders, as well as hydraulic control valves in small runs. External and internal machining of flange parts or grinding of threads or non-circular forms are also possible.
As always, the competent and reliable STUDER Customer Care service is close at hand to provide advice and technical support. “A total of more than 200 specialists worldwide ensure that the S100 will operate reliably and efficiently throughout its entire lifetime and fully satisfy all requirements,” Bottazzo said. “Customers can rely on the 110-year grinding tradition of STUDER.”
Technical data of the S100 at a glance
- Max. workpiece length: 550 mm (21.65 inches)
- Max. swing diameter: 425 mm (16.73 inches)
- Max. internal grinding diameter: 180 mm (7.08 inches)
- Max. diameter of internal grinding wheel: 63 mm (2.48 inches)
- Internal grinding spindle speeds: 20.000/40.000/60.000 rpm
- Max. diameter of external grinding wheel: 400 x 40 x 127 mm (15.74 x 1.57 x 5.00 inches) F1N
- Workhead: Chuck workhead ISO50/110 or chuck workhead MT4/70
- Machine dimensions W × D × H: approx. 3090 × 2090 × 1990 mm (121.65 × 82.28 × 78.34 inches)
- Machine weight: approx. 4500 kg (9,920 lbs.)
Contact Details
Related Glossary Terms
- chuck
chuck
Workholding device that affixes to a mill, lathe or drill-press spindle. It holds a tool or workpiece by one end, allowing it to be rotated. May also be fitted to the machine table to hold a workpiece. Two or more adjustable jaws actually hold the tool or part. May be actuated manually, pneumatically, hydraulically or electrically. See collet.
- cylindrical grinding
cylindrical grinding
Grinding operation in which the workpiece is rotated around a fixed axis while the grinding wheel is fed into the outside surface in controlled relation to the axis of rotation. The workpiece is usually cylindrical, but it may be tapered or curvilinear in profile. See centerless grinding; grinding.
- grinding
grinding
Machining operation in which material is removed from the workpiece by a powered abrasive wheel, stone, belt, paste, sheet, compound, slurry, etc. Takes various forms: surface grinding (creates flat and/or squared surfaces); cylindrical grinding (for external cylindrical and tapered shapes, fillets, undercuts, etc.); centerless grinding; chamfering; thread and form grinding; tool and cutter grinding; offhand grinding; lapping and polishing (grinding with extremely fine grits to create ultrasmooth surfaces); honing; and disc grinding.
- grinding machine
grinding machine
Powers a grinding wheel or other abrasive tool for the purpose of removing metal and finishing workpieces to close tolerances. Provides smooth, square, parallel and accurate workpiece surfaces. When ultrasmooth surfaces and finishes on the order of microns are required, lapping and honing machines (precision grinders that run abrasives with extremely fine, uniform grits) are used. In its “finishing” role, the grinder is perhaps the most widely used machine tool. Various styles are available: bench and pedestal grinders for sharpening lathe bits and drills; surface grinders for producing square, parallel, smooth and accurate parts; cylindrical and centerless grinders; center-hole grinders; form grinders; facemill and endmill grinders; gear-cutting grinders; jig grinders; abrasive belt (backstand, swing-frame, belt-roll) grinders; tool and cutter grinders for sharpening and resharpening cutting tools; carbide grinders; hand-held die grinders; and abrasive cutoff saws.