Ottobock SE & Co. KGaA, a Duderstadt, Germany-headquartered manufacturer of orthopedic systems, was building its 10th and largest manufacturing factory, located in Blagoevgrad, Bulgaria, in 2021 and wanted to pay special attention to establishing efficient, sustainable part finishing operations. For this reason, the company incorporated a specially developed Keramo-Finish process from Rösler Oberflächentechnik GmbH in Untermerzbach, Germany. The process uses an energy-efficient dryer and a centrifuge for cleaning and recycling process water. (Otto Bock HealthCare LP is in Austin, Texas, and Rosler Metal Finishing USA LLC is in Battle Creek, Michigan.)
Founded in 1919, Ottobock has more than 8,000 employees, has an annual sales volume of more than $1 billion and is represented in about 60 countries.
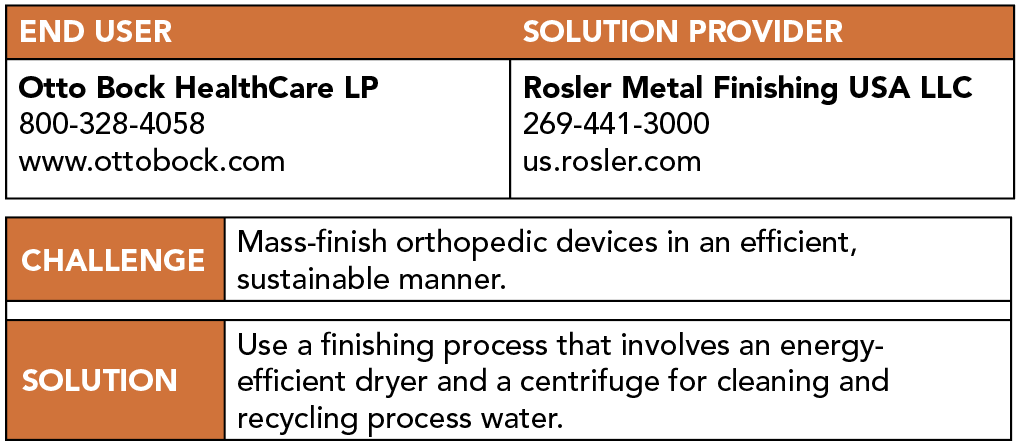
For producing its products, Ottobock uses a range of manufacturing technologies. In this context, mass finishing plays an important role. On one hand, the finishing processes must ensure that products meet all functional requirements, such as being free of burrs. On the other hand, mass finishing must produce an aesthetically pleasing surface finish. This requirement also includes the creation of a highly homogeneous surface structure on the components, which primarily are made from aluminum and stainless steel. Some products even require a high-gloss polish.
For many years, Ottobock has been using equipment and consumables from Rösler. So when Ottobock was looking for new mass finishing equipment to produce components in a more optimized, sustainable manner, it was only natural that the company turned to Rösler for help.
For the initial processing trials, the Customer Experience Center at Rösler reportedly represented the ideal platform. The center is not only equipped with the latest equipment for practically all finishing technologies but can resort to a portfolio of more than 15,000 media and compounds, which were developed and produced in-house.
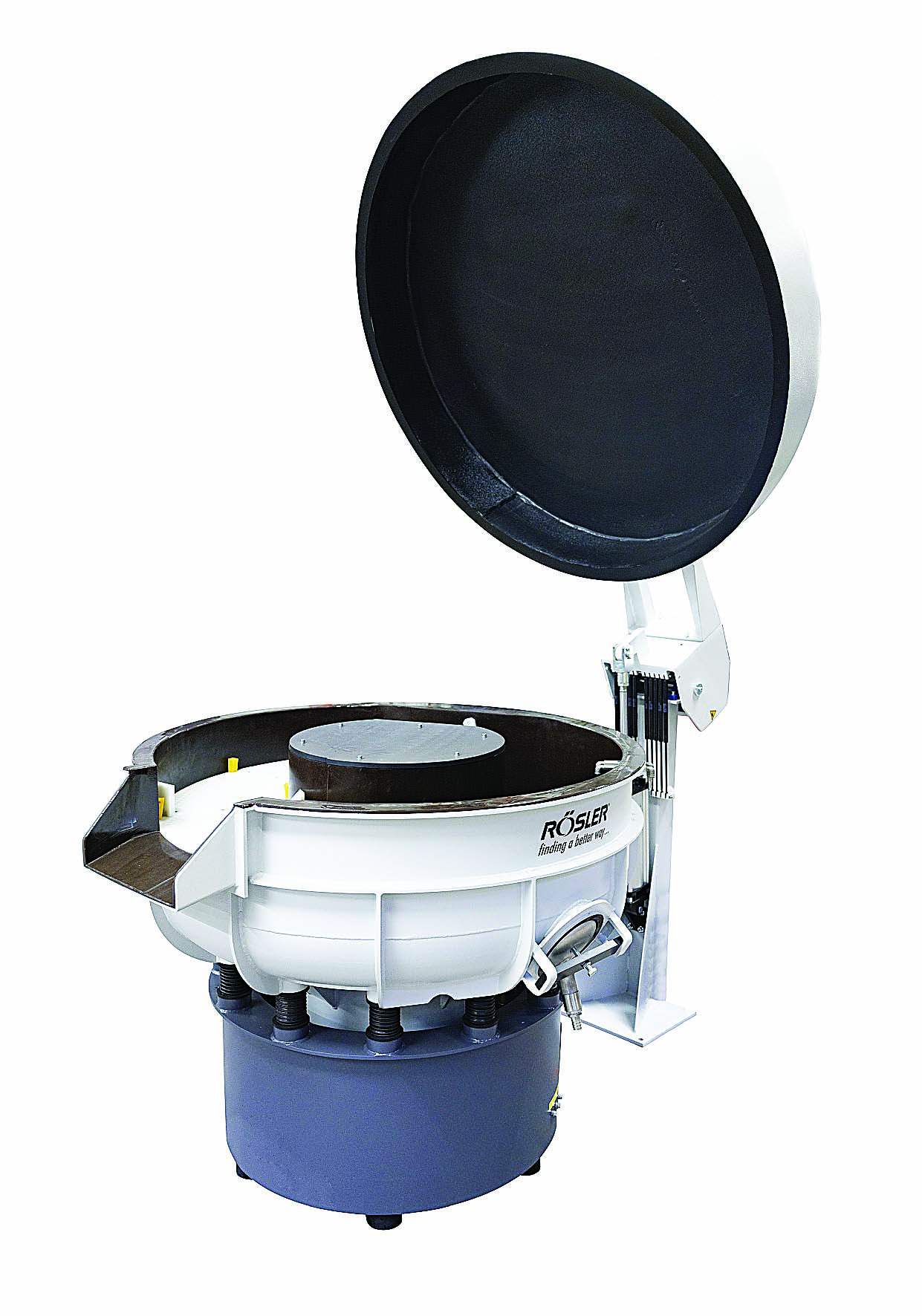
Among other measures, an acid-based process for creating a high-gloss polish was replaced with a custom Keramo-Finish operation. This includes using a porcelain polishing media combined with a special paste and a brightening compound. The acid-free process allows the process water to be recycled completely. This capability has significantly decreased consumption of water and compounds, not to mention costs.
The polishing operation takes place in a new Rösler R 780 EC rotary vibrator. The special shape of the processing bowl creates a gentle, homogeneous flow of the media/workpiece mix, according to the company. This flow ensures that small and delicate, as well as large and bulky, workpieces are polished and separated in an efficient, gentle manner. The same operational benefits also are achieved with a second new rotary vibrator from Rösler, the model R 420 EC. Together with specially selected media and compounds, Ottobock uses this machine for a broad spectrum of applications that range from deburring and edge radiusing to surface smoothing.
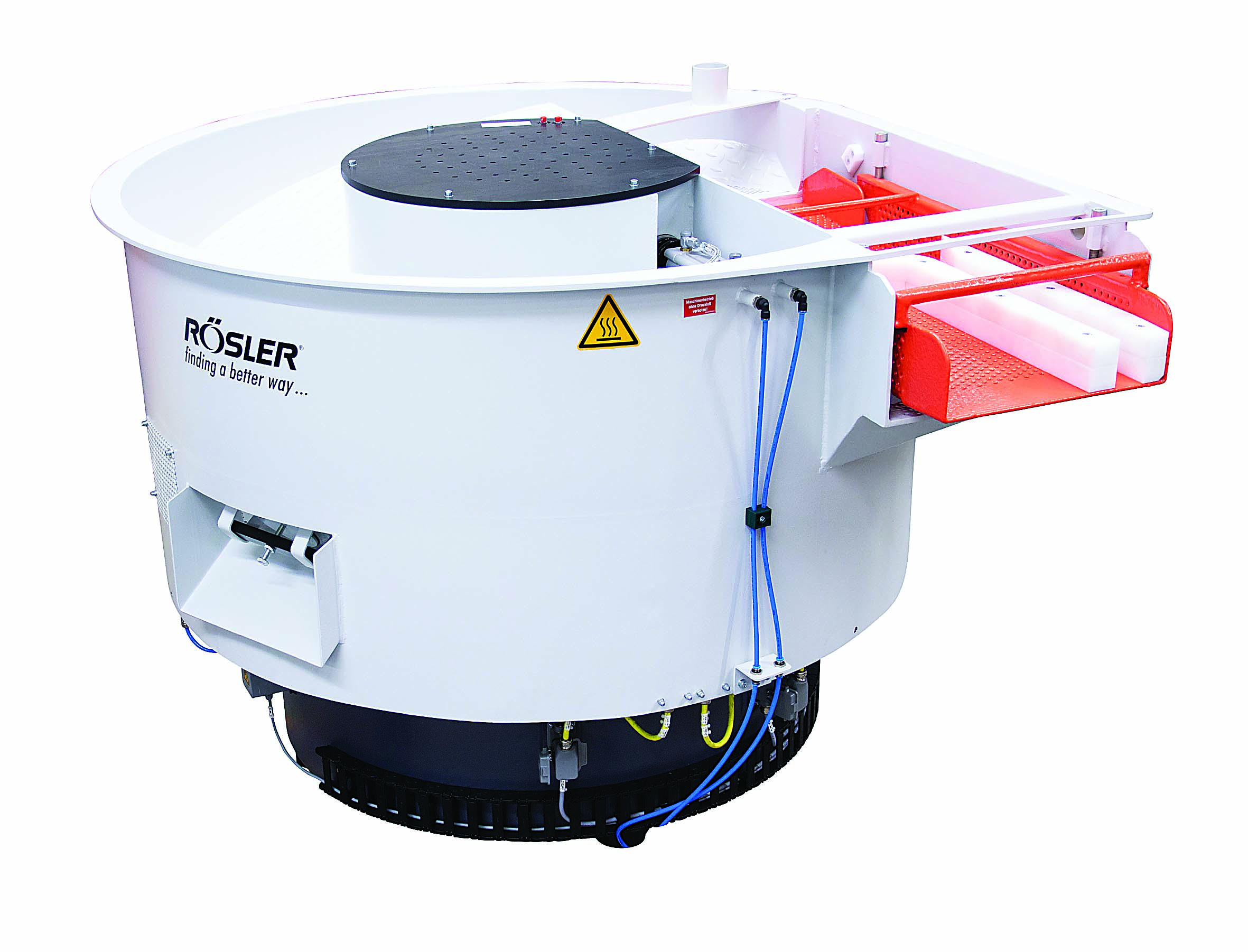
To clean and recycle the process water, the two mass finishing machines are connected to a semi-automatic Rösler centrifugal cleaning system, the model Z 800.
For drying finished workpieces, Ottobock chose the latest version of the RT 550 Euro-DH rotary dryer from Rösler. This direct-heat dryer is equipped with a heat-block heating system directly mounted to the base plate of the processing bowl. The configuration ensures highly efficient heat transfer with minimal heat loss. Thus, the dryer guarantees quick, reliable and spot-free drying and allows energy savings of up to 40% compared with conventional drying systems.
The new dryer also helps reduce carbon dioxide emissions, representing an important contribution toward achieving Ottobock’s environmental and climate targets.
Contact Details
Related Glossary Terms
- centrifuge
centrifuge
Filtering device that uses a spinning bowl and the differences in specific gravities of materials to separate one from another. A centrifuge can be used to separate loosely emulsified and free oils from water-diluted metalworking fluid mixes and to remove metalworking fluids from chips.
- polishing
polishing
Abrasive process that improves surface finish and blends contours. Abrasive particles attached to a flexible backing abrade the workpiece.