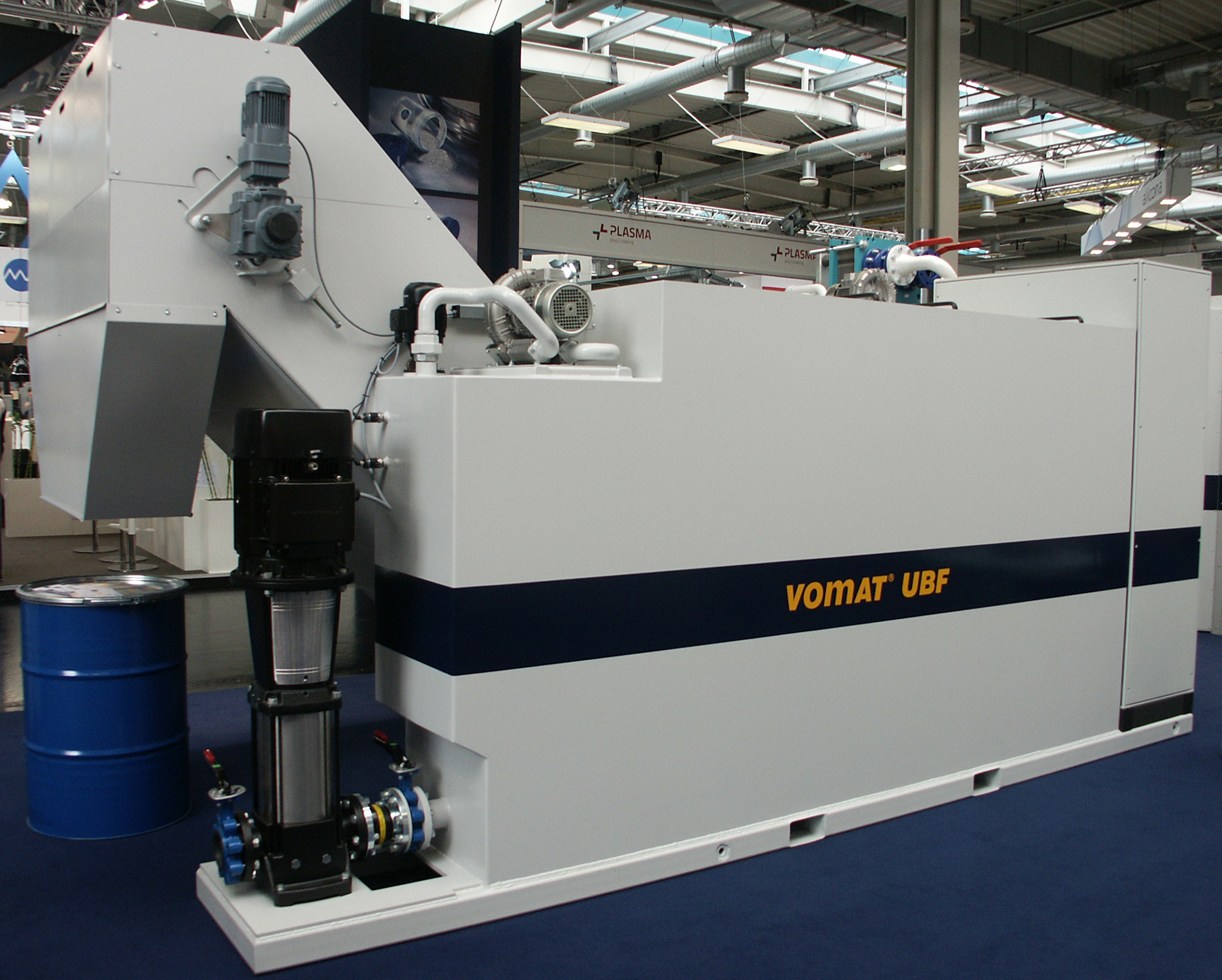
Saving energy, conserving resources and reducing operating costs are major challenges for tool grinders and thus also tasks for their machine and component suppliers. One example is ultrafine filtration of coolants.
At the GrindTec show in Leipzig, which will be held March 7-10, Vomat, the filter manufacturer from Treuen, will show machine solutions that the company says will meet the high demands of the industry for cost efficiency with simultaneous sustainability aspects.
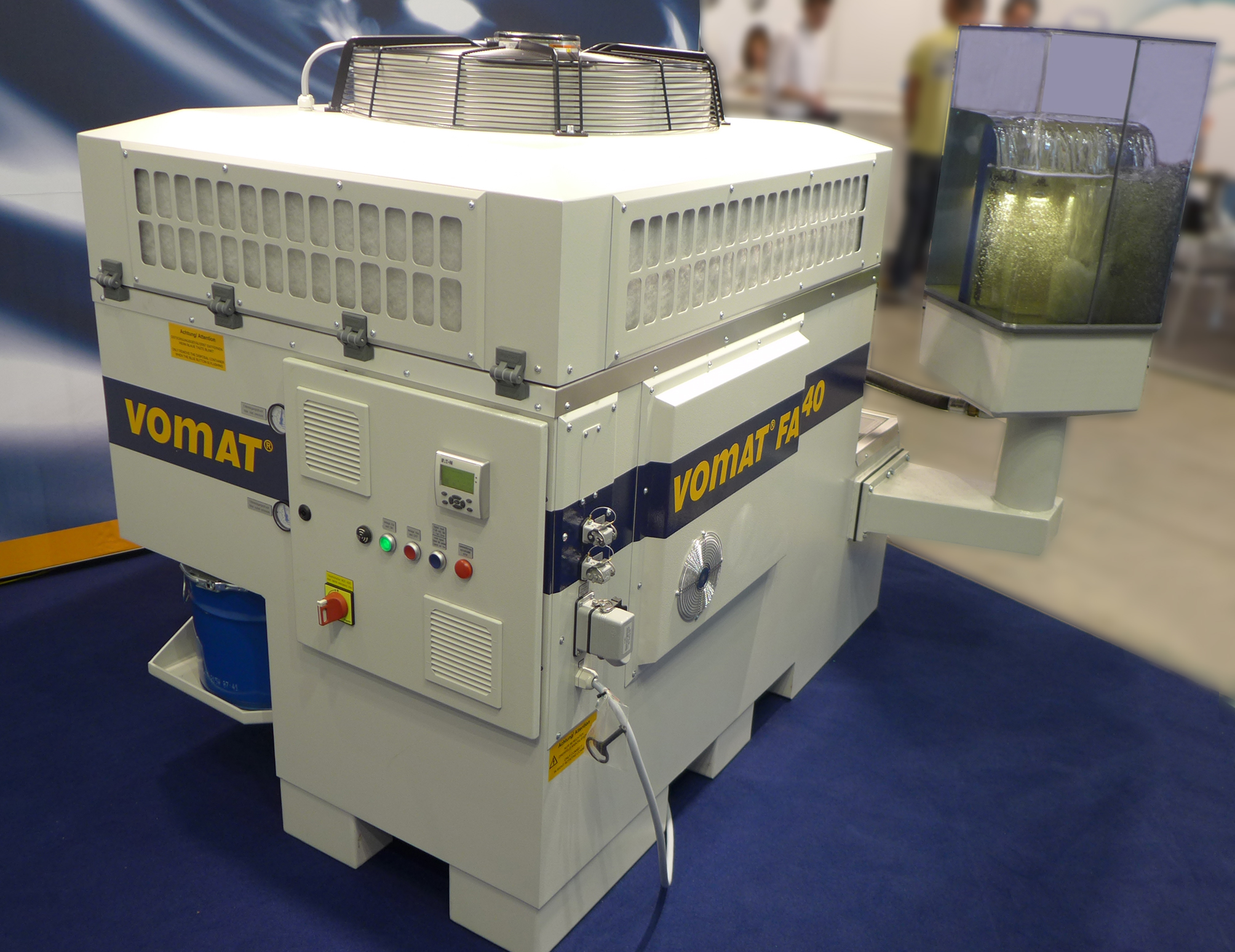
Ultrafine filtration of coolant represents an indispensable component and value-adding factor in the overall tool grinding system. Steffen Strobel, sales manager at Vomat, said "The operating costs of cooling lubricants in tool grinding often exceed the expenses for the grinding tools. Tool manufacturers who address this issue can save money - with innovative, high-performance ultra-fine filtration technology that is optimally adapted to the respective capacities and requirements. And those who rely on the right cooling lubricant filtration in addition to state-of-the-art grinding technology can produce more sustainably."
To ensure a high level of production and quality - but also to exploit rationalization and sustainability potential - Vomat provides high-performance filtration systems from the FA series or the vacuum belt filter (UBF), which combine special technical advantages despite a compact design with a small footprint.
For example, Vomat manufactures FA filter solutions - from single units to large-scale industrial central plants - which separate 100 percent dirty and clean oil in full flow using long-life high-performance precoat filters. The purity is in quality class NAS 7 (3 - 5 µm). State-of-the-art filter, cooling, and disposal technology - including HSS pre-filters for mixed processing if required - ensure economic and ecological success in harmony.
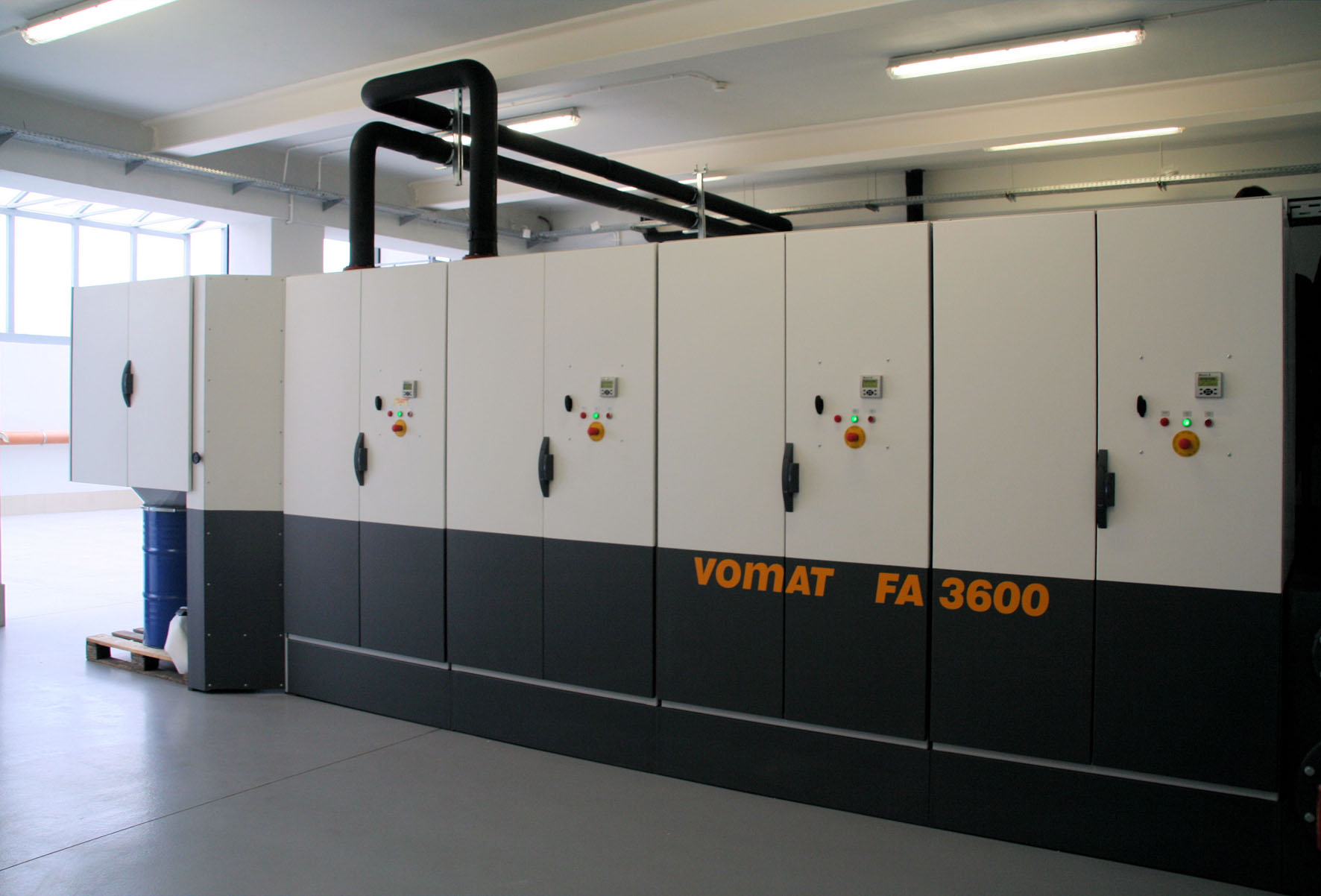
Strobel said: "Cleaning in a full-flow process, back flushing as required, highly accurate, constant temperature control, tailor-made recycling concepts, etc.: Our filtration technology ensures that the coolant media can remain clean in the system for longer. The cleaner and finer the filtration, the better the production quality. This makes the grinding process more economical. Furthermore, MWFs that don't have to be changed as often not only help reduce non-productive time but also lower costs in the acquisition, storage, recycling, and energy consumption."
Contact Details
Related Glossary Terms
- coolant
coolant
Fluid that reduces temperature buildup at the tool/workpiece interface during machining. Normally takes the form of a liquid such as soluble or chemical mixtures (semisynthetic, synthetic) but can be pressurized air or other gas. Because of water’s ability to absorb great quantities of heat, it is widely used as a coolant and vehicle for various cutting compounds, with the water-to-compound ratio varying with the machining task. See cutting fluid; semisynthetic cutting fluid; soluble-oil cutting fluid; synthetic cutting fluid.
- grinding
grinding
Machining operation in which material is removed from the workpiece by a powered abrasive wheel, stone, belt, paste, sheet, compound, slurry, etc. Takes various forms: surface grinding (creates flat and/or squared surfaces); cylindrical grinding (for external cylindrical and tapered shapes, fillets, undercuts, etc.); centerless grinding; chamfering; thread and form grinding; tool and cutter grinding; offhand grinding; lapping and polishing (grinding with extremely fine grits to create ultrasmooth surfaces); honing; and disc grinding.
- high-speed steels ( HSS)
high-speed steels ( HSS)
Available in two major types: tungsten high-speed steels (designated by letter T having tungsten as the principal alloying element) and molybdenum high-speed steels (designated by letter M having molybdenum as the principal alloying element). The type T high-speed steels containing cobalt have higher wear resistance and greater red (hot) hardness, withstanding cutting temperature up to 1,100º F (590º C). The type T steels are used to fabricate metalcutting tools (milling cutters, drills, reamers and taps), woodworking tools, various types of punches and dies, ball and roller bearings. The type M steels are used for cutting tools and various types of dies.