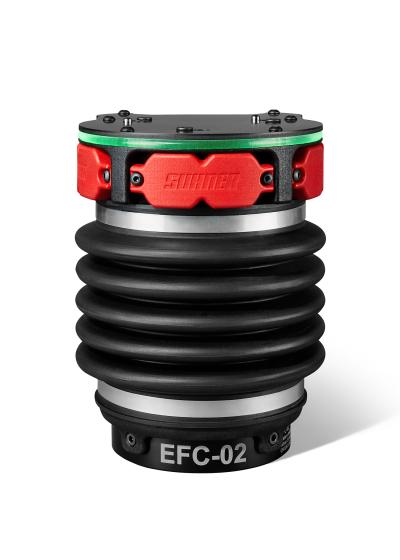
Recognizing the role robotics plays in adding efficiency and lowering production costs for manufacturers of all types and sizes, Suhner continues to expand its robotics offering. The fully electric EFC-02 delivers precise, constant force throughout robotic grinding, sanding and deburring processes – resulting in superior, consistent surface quality.
Introducing EFC-02 – Suhner's Electric Force Compliance System
Active compliance for robotic material removal
With today's supply chain and labor challenges, manufacturers of all types and sizes are looking for solutions to help them do more with fewer resources. That's what smart manufacturing is all about – and why Suhner is expanding its suite of robotic grinding accessories and tools with the fully electric EFC-02 active compliance system.
Smart Automation for High Surface Quality Results
Exact contact force with the surface is the single most crucial factor in robotic grinding, sanding and deburring processes. It's also one of the biggest challenges, especially for hard-to-reach areas. Thoughtfully designed based on Suhner's decades of material removal process know-how – the EFC-02 helps overcome that challenge.
As with any end-of-arm tooling, the EFC-02 connects a grinding machine – angle grinders, orbital sanders, angle polishers, straight grinders and others – to the robot. What makes Suhner's system unique, however, is its compact design and fully electric operation.
The lightest and smallest in its category, the EFC-02 can be used for material removal or surface finishing even in tight or narrow spaces often found when processing stainless tanks and vessels for the food and pharma industries or fiberglass bathtubs and sinks. The all-electric technology also allows high-frequency measurements to monitor force and acceleration throughout the process. An advanced control algorithm then dynamically adjusts force and automates grinding processes based on pre-programmed parameters.
The result? Constant contact force with each movement from start to finish for a consistent surface quality – regardless of the surface type, shape, size or orientation.
In Line with Industry 4.0 Standards to Support Digital Transformation
Robotic processes are no longer just for mass production. As the technology has evolved, robotics have become easier to use and more flexible – making them ideal for both small- and medium-sized manufacturers looking to add efficiency, lower production costs or both.
Suhner engineered the EFC-02 with this in mind, giving users:
- Simple robot programming for setting up even complex processes using an intuitive web-based interface or Fieldbus communication. This includes defining target force, payload and stroke values.
- Advanced functionality that is in line with the vision behind Industry 4.0. For instance, a visual LED indicator on the EFC-02 tells users whether the grinding wheel is in contact with the surface or not and when the stroke is at 50% to ensure maximum compensation, among other critical operational information. The EFC-02 even lets users know when maintenance is needed.
One stop for a custom, end-to-end solution
The end-of-arm EFC-02 active compliance system is fully compatible with Suhner's end effectors, including angle grinders, orbital sanders, angle polishers and straight grinders. Optional automatic changers for abrasives or belts, which integrate easily with the EFC-02, are also available. By storing and dispensing new abrasives for pickup by a sander – these automatic changers effectively help speed processes and increase productivity.
Suhner also gives its customers access to one of the most comprehensive ranges of abrasives in the market from all the industry's leading manufacturers. Plus, Suhner's ABRACare customized, volume-based pay-as-you-go inventory management program ensures you always have the abrasives you need.
Working with Suhner means more than having access to industry-leading tools and abrasives – manufacturers also have access to a global network of seasoned abrasives and material removal experts ready to help you solve virtually any challenge.
Put Suhner to Work for You Today
The EFC-02 combines over a century of Suhner's abrasives and material removal expertise with smart automation for the highest surface quality results. Its compact size, all-electric technology and simple programming make it possible to replicate and automate most grinding, polishing, sanding and deburring on a variety of surfaces. This gives manufacturers a cost-effective, low-maintenance solution for replacing many time-consuming and tedious manual processes – saving time and money.
Contact Details
Related Glossary Terms
- grinding
grinding
Machining operation in which material is removed from the workpiece by a powered abrasive wheel, stone, belt, paste, sheet, compound, slurry, etc. Takes various forms: surface grinding (creates flat and/or squared surfaces); cylindrical grinding (for external cylindrical and tapered shapes, fillets, undercuts, etc.); centerless grinding; chamfering; thread and form grinding; tool and cutter grinding; offhand grinding; lapping and polishing (grinding with extremely fine grits to create ultrasmooth surfaces); honing; and disc grinding.
- grinding machine
grinding machine
Powers a grinding wheel or other abrasive tool for the purpose of removing metal and finishing workpieces to close tolerances. Provides smooth, square, parallel and accurate workpiece surfaces. When ultrasmooth surfaces and finishes on the order of microns are required, lapping and honing machines (precision grinders that run abrasives with extremely fine, uniform grits) are used. In its “finishing” role, the grinder is perhaps the most widely used machine tool. Various styles are available: bench and pedestal grinders for sharpening lathe bits and drills; surface grinders for producing square, parallel, smooth and accurate parts; cylindrical and centerless grinders; center-hole grinders; form grinders; facemill and endmill grinders; gear-cutting grinders; jig grinders; abrasive belt (backstand, swing-frame, belt-roll) grinders; tool and cutter grinders for sharpening and resharpening cutting tools; carbide grinders; hand-held die grinders; and abrasive cutoff saws.
- grinding wheel
grinding wheel
Wheel formed from abrasive material mixed in a suitable matrix. Takes a variety of shapes but falls into two basic categories: one that cuts on its periphery, as in reciprocating grinding, and one that cuts on its side or face, as in tool and cutter grinding.
- payload ( workload)
payload ( workload)
Maximum load that the robot can handle safely.
- polishing
polishing
Abrasive process that improves surface finish and blends contours. Abrasive particles attached to a flexible backing abrade the workpiece.
- robotics
robotics
Discipline involving self-actuating and self-operating devices. Robots frequently imitate human capabilities, including the ability to manipulate physical objects while evaluating and reacting appropriately to various stimuli. See industrial robot; robot.