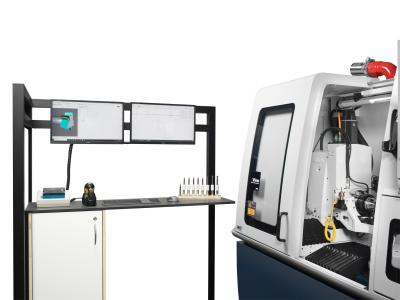
Automated regrinding solutions have gained popularity among tool service providers due to their efficiency and cost-effectiveness in saving time, manual labor, and resources.
With the ANCA RFID (Radio Frequency Identification) regrinding solution, tools of various types and diameters and from different orders can be dynamically loaded, rather than having to sort them by diameter or customer as was previously necessary in mixed batches.
ANCA recently introduced its new FX-RFID solution, extending the popular RFID workflow to the FX Linear platform, unveiling it at IMTS 2022.
Tool service providers are increasingly turning towards automated solutions for unattended regrinding. Australian tool manufacturer Carbitool, cite the process efficiencies, ease of use, and lights out capabilities gained with the automation solution. This first installation in Australia provides valuable insights into the technology and its advantages.
Andreas Sommer, ANCA Product Manager explains: “ANCA provides a range of automated regrinding solutions for mixed batches, including collet loading with Nikken collets. This entry-level solution is available on the FX5 with the AR300 robot and allows for the tool and collet to be changed together. The Loadermate software sets up a mixed batch of tools for unattended operation.”
Regrinding solutions to fit your needs
ANCA also provides the option of collet changing with RFID technology, which was previously only available on the MX platform. This feature has now been extended to the FX5 and FX7 models, allowing customers to select the regrinding solution that best fits their business needs in terms of both capacity demands and budget.
While some resharpening services aim to run their machines unattended for a brief period with only a small mixed batch of tools, many medium-sized companies seek to enhance their tool loading capacities and flexibility. ANCA's RFID solution is designed to meet the needs of medium-sized tool service providers, enabling them to run their machines unattended for several hours, or even overnight.
How the RFID automation solution works
The FX-RFID solution uses two pallets and a pallet top with a maximum capacity of 88 tools. According to Andreas, “Regrinding an endmill or a similar cutting tool takes an average of five to six minutes. With a rate of 10 tools per hour, it's easy to estimate the potential for unattended lights-out regrinding to increase machine utilization and productivity.”
ANCA's Dynamic Tool Group Manager programming station enables preparation of any combination of tools from different customers for regrinding. With the RFID workflow, tools can be loaded into the machine without the need for pre-programming individual pallet pockets. The RFID and tool carrier can be placed anywhere on the RFID pallet top, and the tool holder's RFID code is used to locate the assigned program.
Every tool will be assessed at the workstation, where skilled operators select and modify the required grinding program. The individual program reference is then encoded onto an RFID tool holder, which is placed in a pallet along with the tool for the grinding machine. Customer names and job numbers can be added to each tool holder, making it easier to identify the original customer order after grinding.
During the running schedule, tools can be added, removed, or rearranged within the pallet. The job will terminate when an empty pocket is detected, indicating the end of the pallet.
When the machine picks up the tool with the RFID tool holder, it scans the RFID code and automatically retrieves the corresponding grinding program, sets all grinding parameters, and loads the correct wheel pack. If a collet change is needed, the machine executes it automatically.
The RFID tool holder is then parked at an interchange station, and the tool is loaded for regrinding. Meanwhile, the robot picks up the next tool and scans the RFID code, all while the previous tool is being automatically reground.
Every FX machine with an RFID package comes with an extension to the machine canopy and is fitted with a Fanuc 200iD robot. The following components enable the dynamic loading:
- Dynamic Tool Group Manager
- RFID assembly (Sick reader, interchange station)
- Bench mounted scanning station
- Schunk collet adapter, collet rack to hold up to 6 bayonet collets
- RFID pallet top (88 tool capacity) and RFID tool carriers
Contact Details
Related Glossary Terms
- collet
collet
Flexible-sided device that secures a tool or workpiece. Similar in function to a chuck, but can accommodate only a narrow size range. Typically provides greater gripping force and precision than a chuck. See chuck.
- endmill
endmill
Milling cutter held by its shank that cuts on its periphery and, if so configured, on its free end. Takes a variety of shapes (single- and double-end, roughing, ballnose and cup-end) and sizes (stub, medium, long and extra-long). Also comes with differing numbers of flutes.
- grinding
grinding
Machining operation in which material is removed from the workpiece by a powered abrasive wheel, stone, belt, paste, sheet, compound, slurry, etc. Takes various forms: surface grinding (creates flat and/or squared surfaces); cylindrical grinding (for external cylindrical and tapered shapes, fillets, undercuts, etc.); centerless grinding; chamfering; thread and form grinding; tool and cutter grinding; offhand grinding; lapping and polishing (grinding with extremely fine grits to create ultrasmooth surfaces); honing; and disc grinding.
- grinding machine
grinding machine
Powers a grinding wheel or other abrasive tool for the purpose of removing metal and finishing workpieces to close tolerances. Provides smooth, square, parallel and accurate workpiece surfaces. When ultrasmooth surfaces and finishes on the order of microns are required, lapping and honing machines (precision grinders that run abrasives with extremely fine, uniform grits) are used. In its “finishing” role, the grinder is perhaps the most widely used machine tool. Various styles are available: bench and pedestal grinders for sharpening lathe bits and drills; surface grinders for producing square, parallel, smooth and accurate parts; cylindrical and centerless grinders; center-hole grinders; form grinders; facemill and endmill grinders; gear-cutting grinders; jig grinders; abrasive belt (backstand, swing-frame, belt-roll) grinders; tool and cutter grinders for sharpening and resharpening cutting tools; carbide grinders; hand-held die grinders; and abrasive cutoff saws.
- turning
turning
Workpiece is held in a chuck, mounted on a face plate or secured between centers and rotated while a cutting tool, normally a single-point tool, is fed into it along its periphery or across its end or face. Takes the form of straight turning (cutting along the periphery of the workpiece); taper turning (creating a taper); step turning (turning different-size diameters on the same work); chamfering (beveling an edge or shoulder); facing (cutting on an end); turning threads (usually external but can be internal); roughing (high-volume metal removal); and finishing (final light cuts). Performed on lathes, turning centers, chucking machines, automatic screw machines and similar machines.