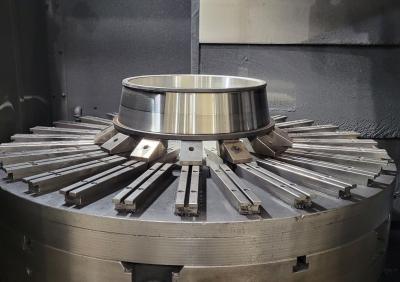
MW Autoblok, a world leader in the design and manufacture of rotational chucks, stationary and magnetic workholding, automation, tooling, and custom engineered solutions, introduces the Radial Pole permanent electromagnetic chuck for precision turning applications.
The Radial Pole permanent electromagnetic system from the Mag Autoblok, a division of SMW Autoblok, is used for vertical turning and grinding of thin wall parts such as bearings, rings, gears, and flanges. Unique to this magnetic system is that when using three solid pole extensions, and using the remainder with spring-loaded pole extensions, this allows the chuck to clamp workpieces with non-distortional clamping from the base surface. Therefore, there are no obstacles to the tool path for three sides of the part and no deformation which does occur with mechanical clamping. Parts can be machined with extremely high accuracies of 10 to 20 microns which can in many cases eliminate grinding.
Since users are holding the part for the base, setups are dramatically reduced. Pole extensions allow users to raise the piece from the magnet surface making the top, inner and outer diameters fully machinable. This process dramatically reduces part distortion due to clamping with ZERO distortion and allowing for far more accurate part processing.
Additional features of the Radial Pole Magnetic Chuck include:
- Full use of machine table
- Complete machining operation in a single setup
- Automatic shimming for stress free operations
Contact Details
Related Glossary Terms
- chuck
chuck
Workholding device that affixes to a mill, lathe or drill-press spindle. It holds a tool or workpiece by one end, allowing it to be rotated. May also be fitted to the machine table to hold a workpiece. Two or more adjustable jaws actually hold the tool or part. May be actuated manually, pneumatically, hydraulically or electrically. See collet.
- grinding
grinding
Machining operation in which material is removed from the workpiece by a powered abrasive wheel, stone, belt, paste, sheet, compound, slurry, etc. Takes various forms: surface grinding (creates flat and/or squared surfaces); cylindrical grinding (for external cylindrical and tapered shapes, fillets, undercuts, etc.); centerless grinding; chamfering; thread and form grinding; tool and cutter grinding; offhand grinding; lapping and polishing (grinding with extremely fine grits to create ultrasmooth surfaces); honing; and disc grinding.
- magnetic chuck
magnetic chuck
Workholding device used on surface grinders and milling machines for holding ferrous parts with large, flat sides. Holding power may be provided by permanent magnets or by an electromagnetic system. See chuck.
- turning
turning
Workpiece is held in a chuck, mounted on a face plate or secured between centers and rotated while a cutting tool, normally a single-point tool, is fed into it along its periphery or across its end or face. Takes the form of straight turning (cutting along the periphery of the workpiece); taper turning (creating a taper); step turning (turning different-size diameters on the same work); chamfering (beveling an edge or shoulder); facing (cutting on an end); turning threads (usually external but can be internal); roughing (high-volume metal removal); and finishing (final light cuts). Performed on lathes, turning centers, chucking machines, automatic screw machines and similar machines.