I may have said this before. If so, please excuse me. But machinists and toolmakers are an opinionated bunch. If you ask 10 machinists how to do a job, you will get 10 different answers. All the proposed solutions will be the fastest, be the easiest to set up and deliver superior quality. Each also will have a litany of reasons why the other nine solutions won’t work.
So when you ask machinists whether a new job should be set up on a vertical machining center or horizontal machining center, you will hear a collage of reasons why one is better than the other.
Truthfully, neither platform is superior as they sit on the showroom floor. Superiority is based on the application and the machine shop that will use the machine.
VMCs, as the name implies, have the spindle in a vertical orientation with a table for the workpiece that is parallel to the floor. HMCs have spindles oriented parallel to the floor with the table also parallel to the floor, which orients the parts perpendicular to the floor. Choosing the better orientation for machining depends on several factors.
The volume of parts is probably the primary consideration when picking a machining center. HMCs are more often the better choice for high-volume machining. Automotive manufacturers, for example, almost exclusively use HMCs.
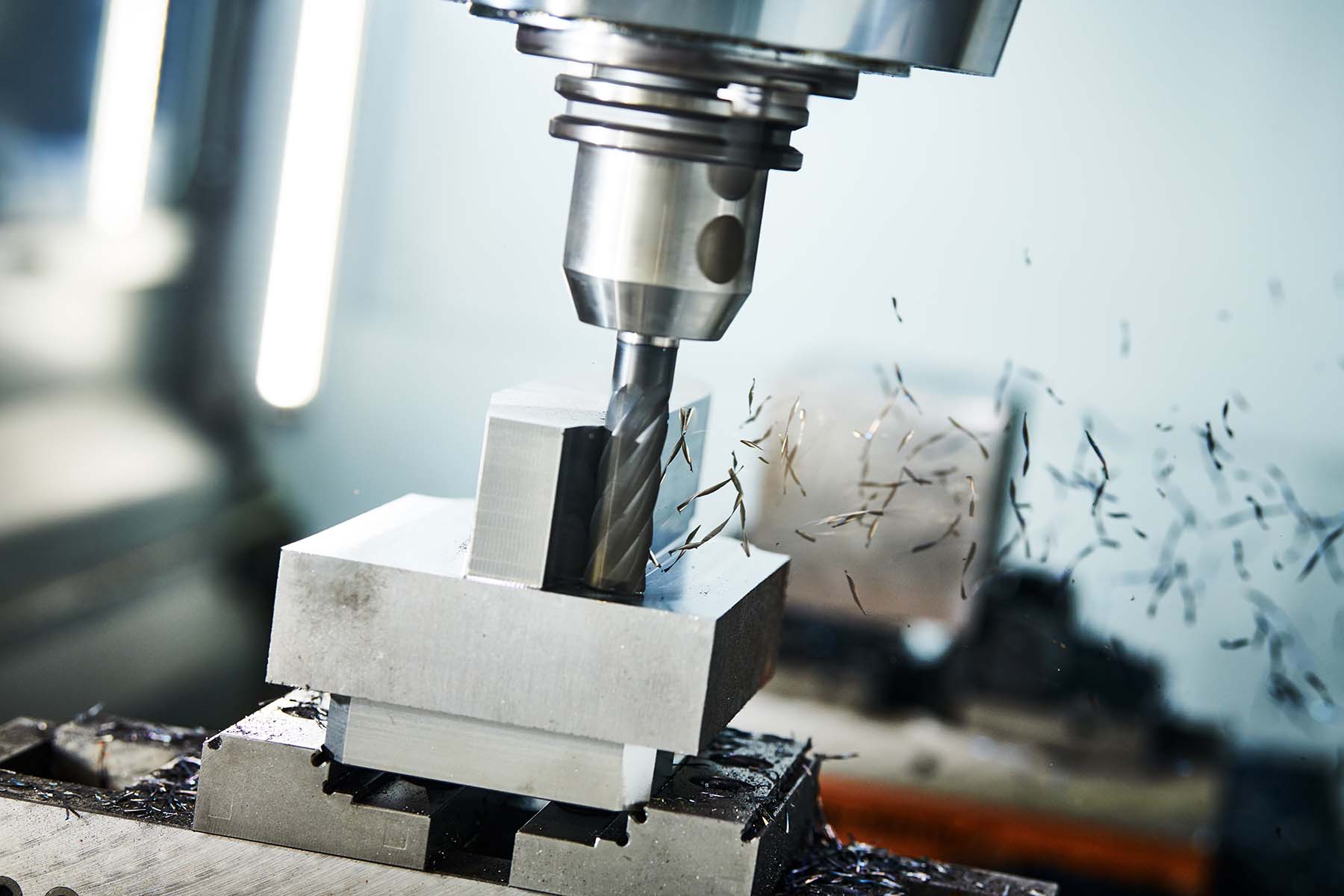
HMCs allow much higher part density. The tables typically are fitted with a multisided fixture called a tombstone that can be fitted to hold numerous parts in different orientations. HMCs also come with two tables that can be exchanged automatically after the machining cycle. This allows the operator to load and unload parts while the machine continues to run, effectively eliminating wasted machine time. Although VMCs can be fitted with tooling that mimics the HMC’s capability, they rarely come from the factory with autoloading tables. Therefore, loading and unloading the machine introduces lost machining time into the equation.
Making a lot of parts also means making a lot of chips. Because parts are held perpendicular to the floor, the chips made on an HMC naturally fall away from the work due to gravity. Chips on a VMC have no place to go, so they must be removed with air, coolant or other methods. If you are going to drill deep holes or mill pockets in parts, an HMC reduces the headaches associated with chip interference.
HMCs usually come prepared for high-volume production with large-capacity tool magazines, chip conveyors and hydraulic systems for automated part clamping. These features are almost always optional equipment on VMCs. One of the most significant elements may be a fourth axis that allows machining of multiple sides. VMCs are built as three-axis machines, so a fourth axis must be added later.
HMCs are built so the components are supported by the way structure from underneath, unlike a VMC, in which some components are cantilevered over the table. The HMC structure is inherently more stable and rigid, which aids process capability. The structure of an HMC is so effective that some VMC builders have adapted the concepts to VMCs, but these are somewhat unconventional and very expensive.
VMCs are less desirable in high-production environments but excel in other areas. When compared with an HMC of similar value, a VMC has a much larger working envelope. The axis travels are two or three times longer, and they support substantially more weight.
It is much easier to load and clamp large, heavy parts on VMCs as they have wider doors that open in the front so forklifts, cranes and other material-handling machines have easy access. A VMC also occupies less space than an HMC.
Setting up a VMC is simpler than setting up an HMC as well. Because the front of the machine is open and the table is easily accessible, a machinist can comfortably get into the working area to use things like hand tools and indicators. Of course, a machinist can do similar work on an HMC, but it is not as easy since access is through a smaller opening positioned on the side of the working area.
VMCs are less complex than HMCs, which provides advantages. VMCs have fewer systems and moving parts, so they have fewer components that can fail. Plus, they are easier to work on when something fails. Programming is somewhat smoother because there is only one table and three axes. The difference in complexity also means that VMCs are less expensive than HMCs of similar capability.
So how do you decide which is better for your shop? In many cases, the cost of the machine automatically dictates the style of the machining center purchased. The lower cost of VMCs is why they are found at almost every small shop. Volume and variation are the other most significant factors. If your shop sees a lot of variation and low volume, then a VMC is far more practical. Likewise, high volume almost demands an HMC to be profitable.
In some instances, the geometry of the work dictates the course of action. Some low-volume parts, such as custom valves for petrochemical plants, often need to be machined on HMCs because it is necessary to reach all sides and fixturing the valve body for horizontal machining is far easier.
The machine tool market frequently is presented with new designs and advances. Some stay, and some disappear. But the VMC remains one of the foundational machine tools that can be found at practically every shop. The fact that VMCs have changed little in the past 20 years is a testament to their functionality. Cost, simplicity and a broad range of applications have made the VMC the workhorse of the modern shop.
Related Glossary Terms
- coolant
coolant
Fluid that reduces temperature buildup at the tool/workpiece interface during machining. Normally takes the form of a liquid such as soluble or chemical mixtures (semisynthetic, synthetic) but can be pressurized air or other gas. Because of water’s ability to absorb great quantities of heat, it is widely used as a coolant and vehicle for various cutting compounds, with the water-to-compound ratio varying with the machining task. See cutting fluid; semisynthetic cutting fluid; soluble-oil cutting fluid; synthetic cutting fluid.
- fixture
fixture
Device, often made in-house, that holds a specific workpiece. See jig; modular fixturing.
- machining center
machining center
CNC machine tool capable of drilling, reaming, tapping, milling and boring. Normally comes with an automatic toolchanger. See automatic toolchanger.
- milling machine ( mill)
milling machine ( mill)
Runs endmills and arbor-mounted milling cutters. Features include a head with a spindle that drives the cutters; a column, knee and table that provide motion in the three Cartesian axes; and a base that supports the components and houses the cutting-fluid pump and reservoir. The work is mounted on the table and fed into the rotating cutter or endmill to accomplish the milling steps; vertical milling machines also feed endmills into the work by means of a spindle-mounted quill. Models range from small manual machines to big bed-type and duplex mills. All take one of three basic forms: vertical, horizontal or convertible horizontal/vertical. Vertical machines may be knee-type (the table is mounted on a knee that can be elevated) or bed-type (the table is securely supported and only moves horizontally). In general, horizontal machines are bigger and more powerful, while vertical machines are lighter but more versatile and easier to set up and operate.
- parallel
parallel
Strip or block of precision-ground stock used to elevate a workpiece, while keeping it parallel to the worktable, to prevent cutter/table contact.