While CNC machine shops have experienced significant growth in recent years, a number of challenges could impact future growth. Here are eight potential barriers to growth for machine shops:
1. Skilled workforce shortage. The most obvious challenge is finding and retaining skilled machinists and CNC operators. The overall manufacturing industry, including machining, faces a shortage of qualified workers with the necessary technical skills and experience.
2. Failure to automate. CNC machine tending technology is evolving at a rapid pace. Staying up to date with the latest automation advancements by acquiring robotic machine tending solutions and training employees in these technologies requires a decent amount of investment in time and resources. Failure to deploy automation could lead to a competitive disadvantage.
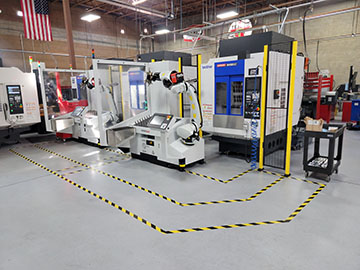
3. Capital investment. CNC machines and robotics are capital-intensive investments. Expanding and upgrading the capabilities of a shop may take substantial capital investment, which can be a barrier for small and medium-sized shops lacking the necessary financial resources. Alternatives to a large capital outlay to consider are equipment-as-a-service or robots-as-a-service subscription models.
4. Intense competition. The CNC machining industry is highly competitive, with numerous shops competing for the same clients and programs. Differentiating oneself from competitors and maintaining a strong customer base require continuous improvement, best-in-class technologies, automation, exceptional quality, competitive pricing, workforce sustainability and strong customer relationships.
5. Market saturation. In some regions of the United States, the market for CNC machining services may become saturated. The presence of many shops could lead to severe price competition and reduced profit margins. Expanding into new markets or diversifying
services might be necessary to overcome saturation in a particular market segment.
6. Global economic factors. Shops can be influenced by broader economic trends, including recessions or downturns in specific industries. Economic fluctuations may impact customer demand, investment decisions and the overall health of the manufacturing sector, affecting the growth of shops.
7. Supply chain disruptions. As proven during the pandemic, disruptions in the global supply chain, such as material shortages, price volatility or geopolitical trade restrictions, can significantly burden the operations of shops. Reliance on specific suppliers or geographical dependencies may expose shops to supply chain risks and have consequences for the ability to deliver projects on time and maintain profitability.
8. Regulatory and compliance requirements. Compliance with regulations related to safety (that is, OSHA standards), environmental impact and data security can add complexity and costs to shop operations. Keeping up with evolving regulations and ensuring compliance may pose challenges, particularly for smaller shops with limited resources.
To overcome these barriers, shops should consider strategies, such as investing in workforce development, embracing CNC automation and advanced technologies, cultivating strategic partnerships, diversifying the client base and market segments, and staying agile to adapt to changing market conditions and customer demands.
Related Glossary Terms
- computer numerical control ( CNC)
computer numerical control ( CNC)
Microprocessor-based controller dedicated to a machine tool that permits the creation or modification of parts. Programmed numerical control activates the machine’s servos and spindle drives and controls the various machining operations. See DNC, direct numerical control; NC, numerical control.
- robotics
robotics
Discipline involving self-actuating and self-operating devices. Robots frequently imitate human capabilities, including the ability to manipulate physical objects while evaluating and reacting appropriately to various stimuli. See industrial robot; robot.