It all started when Tony Myers began asking some basic questions—first about his company’s workforce, then about how nearby schools were educating kids. The answers he got set off a chain of events that eventually put him and his firm at the forefront of an effort aimed at teaching local high school students about technologies employed by area businesses. The result was the creation of a broadly backed program that has opened up new career paths for students and provided Myers’ company and others with some well-trained young workers.
Myers is vice president of human resources at U.S. Tool Group in Farmington, Missouri. Billing itself as the largest cutting tool reconditioner in the world, the company operates a 250,000 sq. ft. manufacturing center where hundreds of reconditioning specialists process more than half a million tools each week using dozens of grinding machines and other types of equipment.
Myers’ story of the industrial program begins with a troubling conversation he had several years ago with his company’s plant manager. Asked how job candidates were evaluated, the manager told him that one way was to ask if they tinkered with their cars.
“That concerned me a little bit,” he recalled. “We resharpen cutting tools, and nobody around here has ever used the equipment or worked with the tools and other things that we have. So our evaluating and training program needs to be pretty good.”
Myers’ level of concern was elevated when, during subsequent conversations with local high school teachers and administrators, he discovered that students graduated from the schools with no marketable skill set. This was because the schools were entirely focused on preparing their students for college. But when Myers asked how many of the students actually go to college, the answer he got was about 60%. What’s more, the educators estimated that only about a third of those students ended up getting bachelor’s degrees.

The bottom line Myers delivered to the educators was stark: “I said, ‘So your (only) track is college, but only 20% of the students are achieving a bachelor’s degree, and the other 80% are screwed.’”
After these discussions, Myers organized a meeting at U.S. Tool to address the situation. The meeting included administrators from all the school districts in the region, as well as a couple of elected officials and representatives of the local community college, the vocational school and a handful of area businesses. At this meeting and several others that followed, a number of important facts emerged. Among these: none of the high schools represented had industrial arts or technical education programs, and the schools were funded to prepare students for college and measured solely on that basis. The school administrators also acknowledged that as many as half their students might be interested in careers that don’t require a bachelor’s degree, but they stressed that there was no money to set up programs for these students.
Partnership Launched
So in 2019, the Industry and Education Partnership was launched. “This jelled unbelievably, with buy-in from the entire community,” Myers said, adding that 80 to 100 people attend the partnership’s quarterly meetings. “All the school districts and multiple companies send people. State reps, senators, city administrators, people from our industrial development authorities and chambers of commerce, they all come.”
According to Myers, 15 companies are currently involved in the program, with membership limited to industrial firms. Primarily, these companies donate equipment and tools to area schools for technical training purposes, as well as instruction time and help with curriculum development. For example, he pointed out that one company donated welders to four school districts that wanted them. “The company said, ‘Take this welder and then let’s partner together, and we can help you to design your welding curriculum so it’s very practical,’” he noted.
Today, all 13 school districts in the Farmington area offer industrial education courses. In addition to welding, area students are getting training in fields such as auto repair, carpentry and electrical technology. They’re also learning how to use a variety of different tools and machines, including those deployed in U.S. Tool’s plant.
With the tools, equipment and curriculum assistance from the partnership companies, the schools simulate the jobs done at each one of the firms. Though every school district doesn’t offer training for all the companies involved, training for each firm is available in at least some of the districts, Myers explained, so students can go to a different district in the area for training that their district does not provide.
Onsite Learning
In addition to learning the skills needed to work for the companies in the program, students get regular opportunities to tour the facilities. Last year, about 600 students were bused to the participating firms, according to Myers.
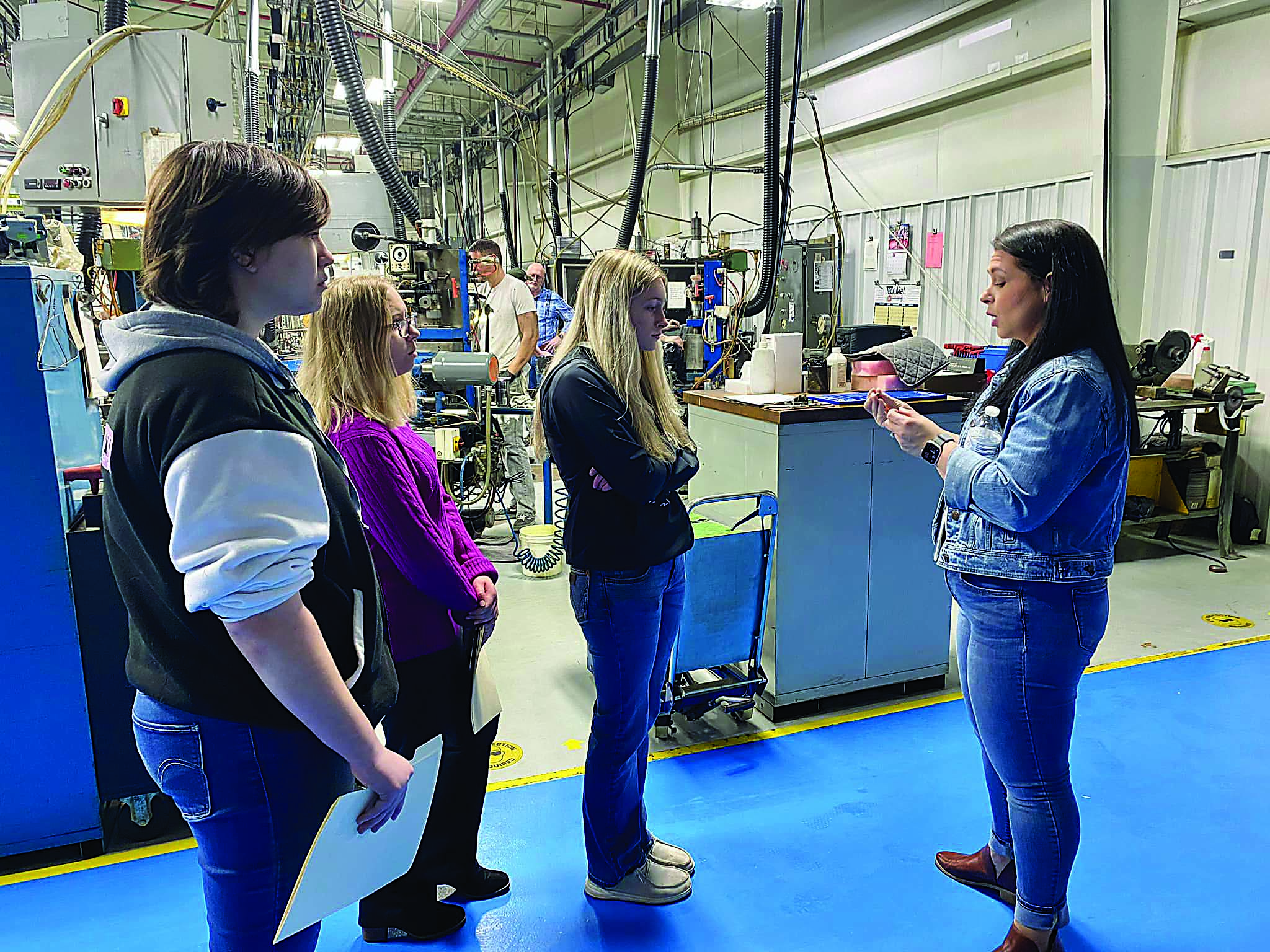
“These kids can see that if you walk into U.S. Tool, it’s not dirty, dark and unsafe,” he said. “It’s clean and bright, and we have state-of-the-art equipment. And we do some neat things for some important (programs) in aerospace and defense.”
To give students an even better idea of what different jobs are like, companies in the program also offer apprenticeship and internship opportunities. In some cases, students who avail themselves of these opportunities love the work, Myers said. “And in some instances, they don’t like it and they try something else that’s better for them.”
As an example of the latter, Myers described the case of one student who went to work for U.S. Tool as an intern. She didn’t like the work she was doing at first, he said, “so we talked to her a little bit about what she did like. And then we moved her into IT to finish her internship.” Though at the beginning of the process the girl was planning on an industrial career after high school, by the end she had changed her mind and decided to go to college to pursue a degree in IT.
Other Successes
Since its inception, Myers added, the program has also been very successful at raising funds from government entities, chambers of commerce and individuals to further industrial education in the Farmington area. Among other things, this money has been used to build a multimillion-dollar technology center on the campus of the local community college and add about 25% more floor space for expanding programs at the vocational school. Before, “the technical school wasn’t running at full capacity,” Myers said. “Now they have a waitlist.”
As for future plans, Myers would like the partnership to add more businesses and help area high schools increase the number of industrial programs for juniors and seniors. He’d also like to see local schools come up with industrial offerings for freshmen and sophomores—and perhaps even middle school students.
“When I was a kid, we had middle school shop,” he recalled. “I have fond memories of that, and I've utilized what I learned in shop in seventh and eighth grade, though I didn't take industrial arts after that. It also gives kids more opportunities to see what (career) tracks there are.”
According to Myers, six to eight young people from the program are currently working at U.S. Tool, and he estimates that around a dozen have worked for the company since the program’s inception. From a financial standpoint, he maintains that the program has not been a good investment, considering the amount of time and money the company has spent on it. But that was never the goal of CEO Bruce Williams.
“We've gotten some workers, but that’s not what it’s about for us,” he said. “Bruce is about doing what’s right for the region and for the students, and we feel good about that.”
Contact Details
Related Glossary Terms
- grinding
grinding
Machining operation in which material is removed from the workpiece by a powered abrasive wheel, stone, belt, paste, sheet, compound, slurry, etc. Takes various forms: surface grinding (creates flat and/or squared surfaces); cylindrical grinding (for external cylindrical and tapered shapes, fillets, undercuts, etc.); centerless grinding; chamfering; thread and form grinding; tool and cutter grinding; offhand grinding; lapping and polishing (grinding with extremely fine grits to create ultrasmooth surfaces); honing; and disc grinding.